StraightLine’s Custom Reamer Service Fills Large American Augers Order
November 1, 2008
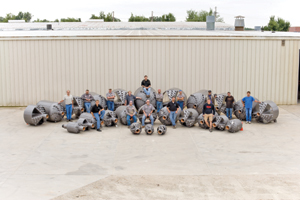
This order, which was the largest single custom reamer job StraightLine has completed to date, consisted of 26 reamers in two different styles — the Maxi-Fly and Maxi-Barrel. The reamers ranged in size from 18 to 64 in. and were built on 9.5-ft diameter shafts with 6 5/8-in. FH connections. The biggest reamer in the order was a 64-in. Maxi-Fly that tipped the scales at 6,640 lbs. The custom order took less than 21 days to complete and weighed a massive 50 tons.
“This particular order is going out with a maxi rig and it is being used for the installation of pipeline,” said Don Cary, president of StraightLine. “There are 13 Maxi-Barrel reamers and 13 Maxi-Fly reamers, which is a design that’s unique to us. The soil conditions call for an open-bodied style of tool like the Maxi-Fly. The wide variety of the reamers this client ordered indicates that a crew will be working in similar ground installing a variety of pipe sizes, from 12 to 54 in.”
StraightLine began its custom reamer manufacturing service in 2002 and quickly grew by 2005, accounting for 30 percent of all the company’s reamer production. In just 2008 alone, the company has fabricated more than 400 custom reamers for clients in need of job-specific tools in its 70,000-sq ft facility, located in Hutchinson, Kan.
Currently StraightLine employs 31 machine operators, welders and fabricators in its manufacturing facility and offers 12 different, standard reamer styles that are also available for client customization. In order to create a unique reamer for a specific project, the company works with its clients to design the tools required to get a job done.
“Our custom services are provided through collaboration between us and our clients,” said Cary. “In the field, our clients are performing the work every single day and know what conditions they are dealing with and what types of challenges these conditions create. On the other side of the collaboration, you have us. We understand ground conditions as they relate to appropriate tool design so together we seek to understand the ground conditions and choose a tool design that will, in the end, maximize their productivity.”