Rehabilitation Project of the Year
October 1, 2008
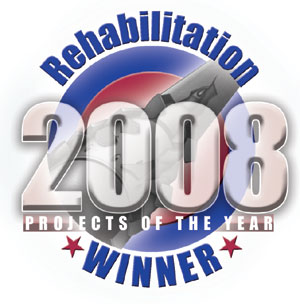
The 2008 Trenchless Technology Project of the Year winner for Rehabilitation was just one of those projects. It was full of complicated, steep bends and a long uphill inversion in an isolated, wooded area. It also introduced CIPP to a previously untapped market in hydroelectric power.
The Bear Creek hydroelectric generating station near Shingletown, Calif., owned and operated by Enel North America, resulted in the rehabilitation of a badly deteriorated 48-in. pipe approximately 1,900 ft in length, handled by Michels Pipe Services, Brownsville, Wis. CIPP was selected as the rehab method after project officials ruled out dig-and-replace. The penstock crossed under a narrow road at a common point with a high pressure gas main and high-tension transfer lines overhead. Excavation would have been extremely risky.
“When we first contacted Michels, we were looking for a price to dig-and-replace around 500 ft of our penstock, beginning at the diversion structure,” explains Patrick Strickland, Enel operations manager for its California projects. “We had approximately 1,900 ft to replace in this section and planned to spread it out over several years. After describing the job, it was suggested that it might be a good candidate for the cured-in-place process… [Michels] came up and inspected the site and determined it could be done using [CIPP] and that it would make more sense and cost less overall if we repaired the entire 1,900 ft at one time.”
Using CIPP also eliminated environmental issues such as stream alteration permits, grading plans, erosion control plans and water quality issues normally encountered when working so closely to a stream.
The Bear Creek power generating station is a 3.2-megawatt run-of-the-river hydro plant. The plant operates in the fall, winter and spring when there is excess water in the stream, using runoff from the Sierra Nevada Mountains. A diversion structure in the stream directs the water into a pipe called a penstock, which runs down the hill to the power house. The water flows through a turbine before being returned to the stream. The electricity that is generated is sold to Pacific Gas & Electric for distribution and is enough to run about 900 homes when the plant is going full strength.
The pipe was 48-in., spiral-ribbed, 16-gauge galvanized pipe that is commonly used in low-pressure penstock applications. Strickland says that inspection of the 23-year-old pipe showed cracking around many of the ribs and holes rusted through the pipe anywhere the galvanized coating had been scratched or damaged during installation. These problems meant that the pipe wasn’t running at its full capacity and the plant’s output was decreasing.
The Bear Creek project is located in the foothills of the Shasta Cascade region of California, about 25 miles east of Redding. It is a rural area made up of mostly mountain pastures and forest land. Project officials describe the area as “being in the middle of nowhere,” forcing crews to truck their equipment and incidentals to the site and making sure they brought everything they needed.
“It was pretty much a gas station and a store,” Michels project superintendent Chris Tavernier says of the area. “We had to drive about 30 minutes away to access cell phone service. So it was imperative that we brought everything we needed to the jobsite every day.”
Getting the Bends
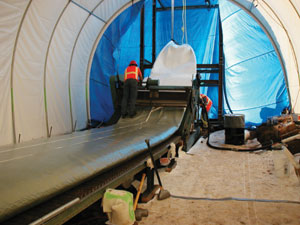
The pipe couldn’t be repaired until the last of the available runoff for power generation was used and the project had to be finished prior to the first snow in the mountains to allow access. The end of October was selected as the best window for the rehab work, as it is historically dry enough to minimize impact to native soils and maintain low flow levels in Bear Creek.
To reduce time onsite, Michels decided to do the CIPP work in a single inversion (approximately 1,850 ft) with the wetout process being performed onsite. Because the finished pipe would weigh about 150,000 lbs, it couldn’t be hauled from an offsite wetout location. So the wetout facility that was constructed at Michels’ Woodland, Calif.-facility, was trucked in on 3 ½ semis and erected onsite and covered with a climate-controlled tent to protect the liner from the elements.
The remoteness of the project location, while beautiful and scenic to the eye, allowed Michels no choice but to handle the inversion against the flow of the creek and uphill, as crews could not mobilize their equipment at the upper end of the creek where the diversion structure was located, Tavernier says. The uphill inversion added another dimension to the level of difficulty the Michels team faced as it forced addressing four sharp bends (a 60-degree, two 45-degree and a 30-degree bend) at the beginning of the shot instead of the end.
“Overcoming the friction was one of the biggest things we faced, because of the amount of drag that is caused on a liner going through those bends,” explains Kelly Odell, Michels Pipe Services vice president, who oversaw the project’s design. “Typically if you have bends in a normal CIPP job, you want them at the end of your run so you don’t have a long tail that you are dragging behind through those bends, creating friction. In this particular case, it wasn’t feasible. They were right at the beginning of the inversion, so now you are dragging the 1,900-ft of bag along through each one of those bends.”
Odell explains that the bend locations required crews to construct a much taller than usual tower to attach the liner to in order to overcome the drag and friction caused by the bends and the rise in elevation. Instead of the typical 13-ft tower, a 36-ft one was erected to ensure that there was enough head pressure to push the liner uphill to the intake.
But once the equipment was mobilized and the site was ready to go, the inversion went smoothly. Tavernier and Odell note that the prep work done over a period of three months was key to ensuring that was the case.
Due to the limited access, coordination of the resin and water tankers was important. Three 40,000-lb tankers of Interplastic Corp. resin were catalyzed onsite and pumped into the 1,900 ft of 48-in. felt tube, which was 21 mm thick. Crews pumped 1.5 million lbs of water to push the pipe into place. Two hot water heat exchangers, totaling 26 million BTUs of heating capacity, brought the water to curing temperature, burning 200 gals of diesel per hour in the process. A containment system was set up at the head wall, where the liner ended and where the creek diverted to capture any water that might come out of the liner during curing; that water was contained and hauled away.
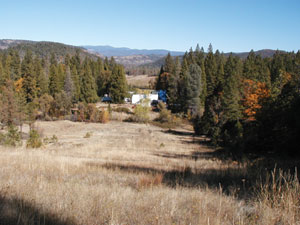
“The entire project went very well and was completed on time and in a fraction of the time that would have been required to dig-and-replace even a small section of the pipe,” Strickland says.
Projects like Bear Creek are few and far between in the CIPP market but that could be changing as hydroelectric, nuclear power, clean coal and the like begin to see how trenchless can help. “[In this case,] Bear Creek is just a start in [the hydroelectric] industry in doing these types of large diameter lines,” says Steve Johnson, Michels West Coast business manager. “The biggest problem for these power companies is that many are way out in the woods where you have limited access.”
“It’s a market we’ve been trying to break into for some time,” Odell says. “There are not a lot of people doing CIPP work in hydroelectric facilities, nuclear power facilities, clean coal fired facilities and the like. Our position is ‘Let’s get into those plants and show them that we can accomplish this with a lot less disruption and downtime than dig-and-replace.’”
Sharon M. Bueno is managing editor of Trenchless Technology.
Project owner: Enel North America
Contractor: Michels Pipe Services
Engineer: Enel North America