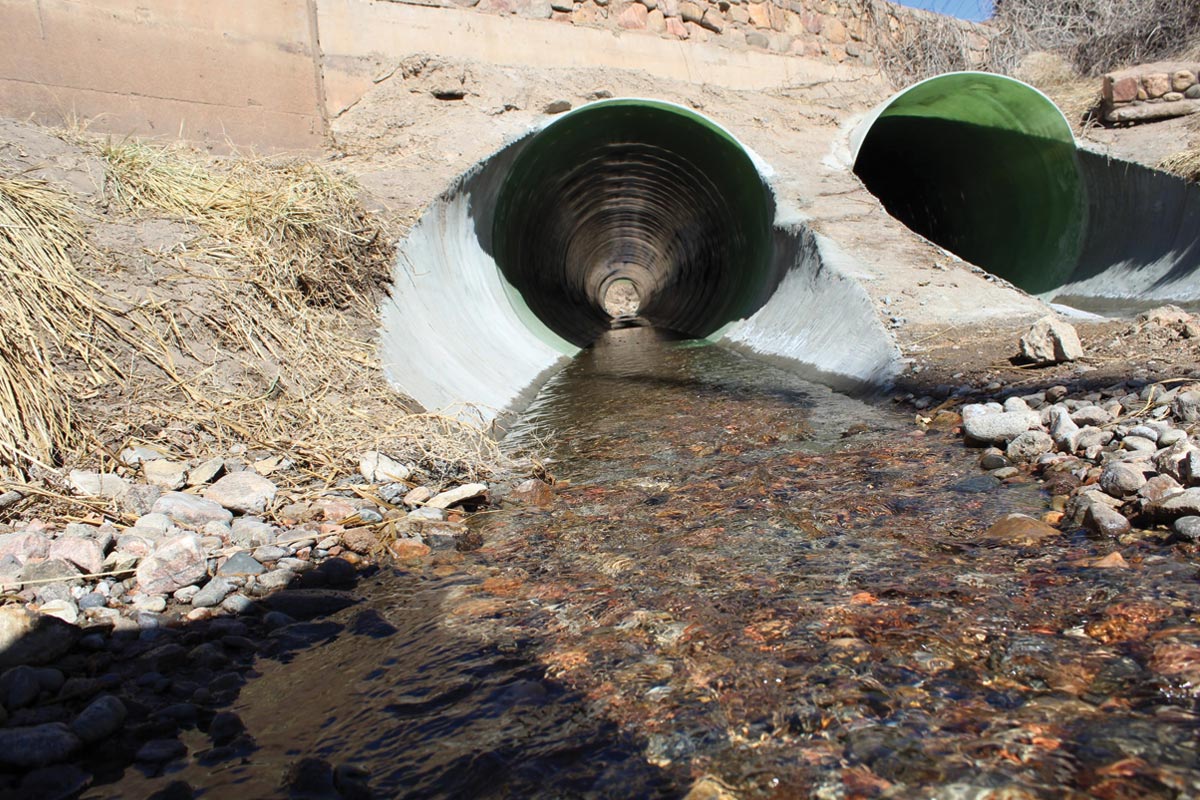
Rehabilitating Irrigation Conveyance Barrels with UV CIPP
This article highlights a recent trenchless rehabilitation project in Colorado. Two 72-in. irrigation conveyance barrels were lined with ultraviolet (UV) cured, pull-in-place, fiberglass-reinforced cured-in-place pipe (CIPP), as per ASTM F2019.
As of writing, 72-in. (~1,800-mm) is still the largest nominal diameter of UV CIPP rehabilitation yet completed in North America. A handful of other installations of this size had taken place prior to this project.
UV CIPP in Colorado
The project took place in Cañon City, in Colorado Department of Transportation (CDOT) Region II. The barrels route the area’s primary mountain-runoff irrigation ditch underneath East US Highway 50.
The jobsite is in proximity to the CO Territorial Correctional Facility and the historic Royal Gorge railroad.
The barrels in question were circular 72-in. CMP originally installed in the 1940s, partially collapsing on the downstream ends.
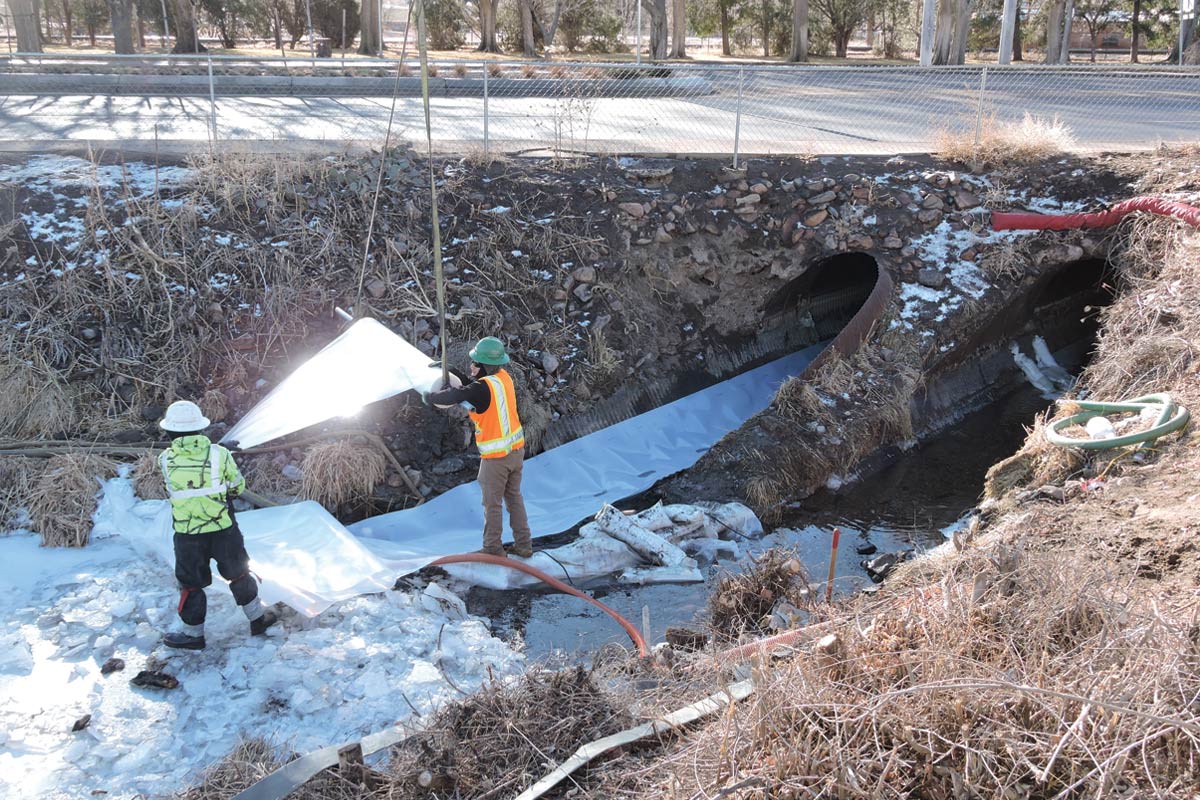
Each shot was about 140 lf, basically straight, with 12-ft tapers at each end. The highly competitive bid included water control, cleaning of each culvert, and removal and disposal of accumulated sediment around the tapered ends. Additionally, traffic control and lining were included.
Initially the water control portion was anticipated to be a major project consideration. The expected flow height was around 4.5 ft. However, cooperation with the irrigation ditch owners led to an agreement to shut off the line to the extent possible. This reduced the height to around 2 ft.
Bypassing for the installation days — Feb. 14 and 20, 2025, respectively — was achieved via placing sandbags approximately 20 ft from each pipe. Workers created a hole and used a 2-in. pump to divert the flow through the barrel not presently being lined.
Protecting Wetlands
One challenge for project staging was the presence of protected wetlands on the upstream end that could not be disturbed. Additionally, power lines infringed on this part of the work area. For this reason, the liners had to be pulled from the downstream end to the upstream end. This is atypical for this type of installation.
Proper use of a protective sliding sheet was especially important in this circumstance to prevent damaging the outer surface of the liners. This was crucial while pulling them at a slight grade, against the grain of the flowline. A crane was used to deposit the liner crates in the ditch bed for pull-in.
As the jobsite footprint by necessity had to be small given the above circumstances, required traffic control was minimal. No refrigeration trucks were required since the UV-cured liners utilized photo-initiated resins. A large tarp was draped over the liner crate and used for additional UV protection during staging.
The first of the two installations saw a considerable weather-related challenge in the form of high winds during the light train introduction. UV CIPP installations often require an external airlock (also called sluice bag) during the insertion of the light train through the packer and into the liner. This is before the faceplate of the packer can be fully sealed and the liner brought to working pressure. This process is more complicated during large diameter installations.
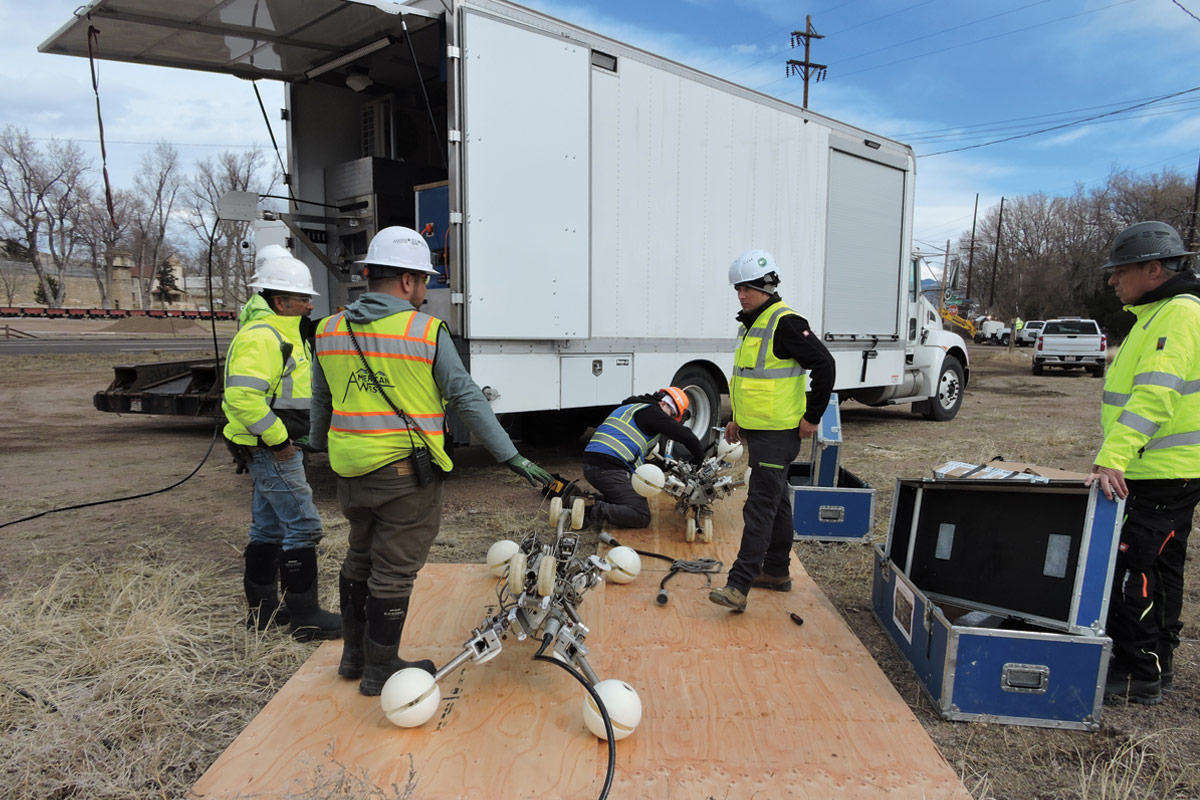
The liner, which is packed flat in the crate, needs to be partially inflated so that the light train can be inserted. Pressure must be maintained due to the risk of the incredible weight of a large liner falling on and damaging the light train. As the light train itself is also very heavy, this means a large sluice bag permitting manned entry and manual insertion of the light train under a safe, managed air pressure is required. The winds were strong enough to displace a jobsite tent. Consequently, working with the low-weight reusable fabric airlock was challenging. This stage of the installation was delayed but ultimately successful.
Liner Design
The liner designs were realized with the ASCE MOP 145 design methodology, as referenced in the Appendices of ASTM F2019. Wall thickness for each fiberglass-reinforced liner was set at 10.1 mm.
Apart from keeping the liner weight (and thus transport costs and footprint concerns) down and minimizing any reduction of flow capacity, the installer reported anecdotally that the slight reduction in required wall thicknesses yielded by this design methodology has the added benefit of minimizing wrinkles in bends. They cited a previous installation of a 60-in. UV CIPP liner with considerable bends, which was designed with MOP 145 and ultimately processed with negligible wrinkles.
The 72-in. liners were cured with a UV light train with two appropriately “jumbo” size cores – additionally fitted with extension legs – which each held six 1,000-watt bulbs. This yielded 12,000 total watts of curing power. It was essential that the light train be both large enough to be centered in the pipe (and thus cure evenly) and have an adequate UV output to penetrate the entire 10.1-mm wall thickness. Curing took about five hours total for each barrel.
One barrel had a lateral connection which had to be beaten down smooth before lining and was reinstated afterwards. An expansion limiter sleeve was fitted at this linear footage mark on the liner to prevent over-expansion at this section. Each installation also utilized expansion limiter sleeves to run out the liner for part of the length of the tapers. The remainders were eventually finished with a high strength, fine aggregate concrete product designed for storm culvert rehabilitation.
This successful rehabilitation was overseen by CDOT, with the installation carried out by American West Construction LLC. The curing equipment was built by ProKASRO Services USA. The fiberglass-reinforced UV CIPP liners were manufactured in the Richmond, Virginia, plant of IMPREG LLC.
Andrew Siegel is technical claims manager/sales and communications coordinator at IMPREG Americas.