Refurbishing and Strengthening an Aging Highway Culvert with UV Lining
April 2, 2014
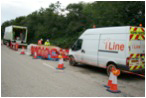
This team brings with it a fresh ‘can do’ attitude and an in-depth new approach that offers clients a level of confidence which is claimed to be previously unseen in the industry. Working in virtually all pipeline sectors, the company utilizes the latest GRP UV (Glass Reinforced Plastic Ultra Violet) cured pipe lining system that offers liners that are some 40 percent thinner while being more than three times times stronger than conventional felt liners.
One area in which the GRP UV liners show significant advantages is that of culvert rehabilitation. Ageing culverts beneath highways can be problematic if they are not replaced or refurbished in a timely manner. To ensure continued operation of its trunk routes the UK’s Highways Agency is undertaking an on-going program of work to ensure that culverts running beneath its roadways continue to operate effectively and efficiently.
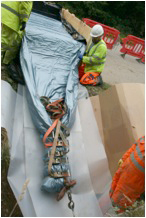
The lining project, initiated on behalf of the Highways Agency by the main contractor, was awarded to iLine Technologies which was required to design a suitable lining to meet the needs of the culvert refurbishment whilst minimizing disruption to the road operation.
With project consulting engineer Kate Sutton, and given the ground investigation results and traffic loading information procured, iLine proposed to utilize a CIPP lining technique with UV (Ultra Violet) curing for the 58-m long lining run in the 1,000-mm diameter culvert. The design called for a liner wall thickness of 9.3 mm.
As well as offering a quick, low foot-print site operation, as compared to other CIPP options, including hot water cure and steam cure, the UV option was also deemed to be far more environmentally friendly with less potential for pollution down-stream of the site due to the absence of run-off wastewater subsequent to the cured liner being opened at the culvert ends post-curing. This design was ultimately accepted by the main contractor, which then gave the go-ahead for the works to begin.
The UV equipment used for the installation was an REE2000 curing unit supplied by Reline Europe, which on this occasion utilized a UV light source comprising of six 2,000 watt UV bulbs. The liner itself was also provided by Reline Europe and was precisely manufactured and factory impregnated with the UV sensitive resin to fit the lining run.
Lining Works
The lining project started on Sept. 9, 2013, and was completed with the iLine crew off the site by Sept. 12.The beauty of the UV system in situations such as this is its speed of operation. On the Monday, the crew mobilized to the project and set up the necessary equipment and work site. On the Tuesday, civil’s works to remove the old head wall on the culvert were completed. On the Wednesday, subsequent to inspecting the culvert to ensure it was clear to line, the UV liner was installed in just 8 hours, including the curing process.
On the day of lining, work started at 8 a.m. The liner was inverted into the culvert using compressed air. The UV light train was then inserted, the liner re-inflated and the curing run started. On average the cure was completed at a speed of some 6 m every 10 minutes or a complete cure in under two hours.
On the final day, the head wall was reinstated and the crew demobilized from the site and the culvert was available and open for operation.
The only aspect of the project that involved outside agencies was that a land agent had to be contacted because the downstream section of the culvert ended in a farmer’s field with the farmer having to be informed of the works. The upstream section of the culvert lay within the boundary of the highway so did not cause a problem.
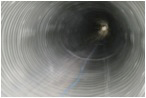
According to iLine business development manager John Beech, “Some of the biggest advantages of using the UV method utilised here were the speed of the installation, with the whole project being completed in just under four days and the fact that the use of the UV also meant that, given the proximity to farm land, the potential for pollution was eliminated from the site because no liquid run-off is generated using the UV system.”
Beech went on to say: “UV lining is a technique that is currently not the most widely available in the UK as there are only a few installers using the system. We at iLine pride ourselves that we have crews that are some of the most experienced in the field in the UK today with numerous successful projects under their belts.”
This article was provided by IGroup, Northhampton, United Kingdom.