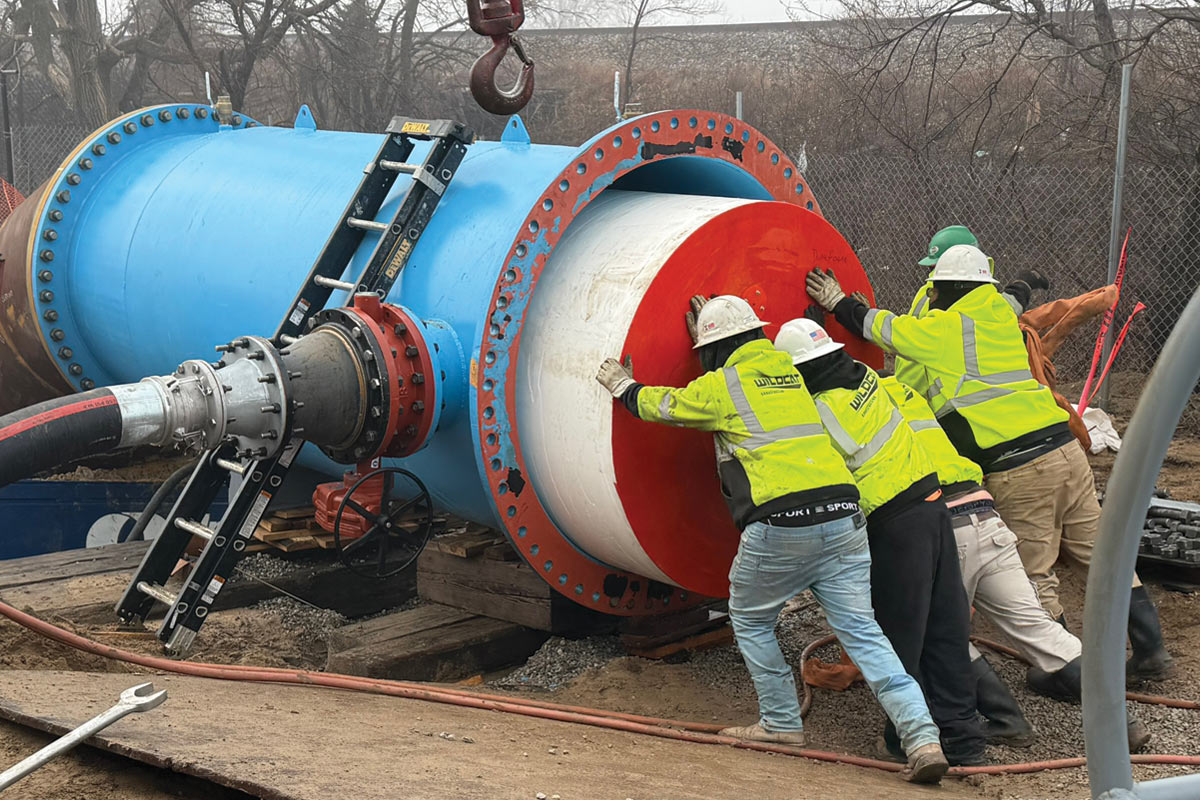
Progressive Pigging a 64-in. Raw Water Line in Wichita, Kansas
A four-mile stretch of a 64-in. diameter raw water pipeline in Wichita, Kansas needed cleaning. The pipelines is a critical component of the City of Wichita’s water system upgrades.
The City is replacing the City’s 80-year-old facility with a state-of-the-art water treatment plant. It will provide clean drinking water to more than 500,000 residents. With the capacity to treat up to 120 million gallons of clean drinking water daily, the Northwest Water Facility represents the largest capital investment in the city’s history at $500 million.
The pipeline in question required thorough cleaning before conversion to a potable water line. The large-diameter pipeline had accumulated significant silt buildup, necessitating a specialized pigging process. Wichita Water Partners enlisted American Pipeline Solutions (APS) for their expertise in pigging large-diameter pipelines.
Preparations
The pipeline, made of ductile iron and prestressed concrete cylinder, was assessed for condition, deposits, and geometry. APS proposed a series of progressive pig runs using different types of pigs to remove the debris. This method was chosen to safely clean the pipe without causing any damage.
With a tight timeline of 10 weeks, there were immediate logistical challenges. Specialized launchers and receivers to accommodate the oversized pigs had lead times of up to twenty weeks. To meet the shortened timeline, APS fabricated a launcher and receiver and modified the design.
Site preparations included the pipeline being brought to the surface at the launch site and attached to the modified launcher. An external pump ensured adequate flow for inserting the pig. Meanwhile, a snubber held the pig in place to prevent it from slipping backward.
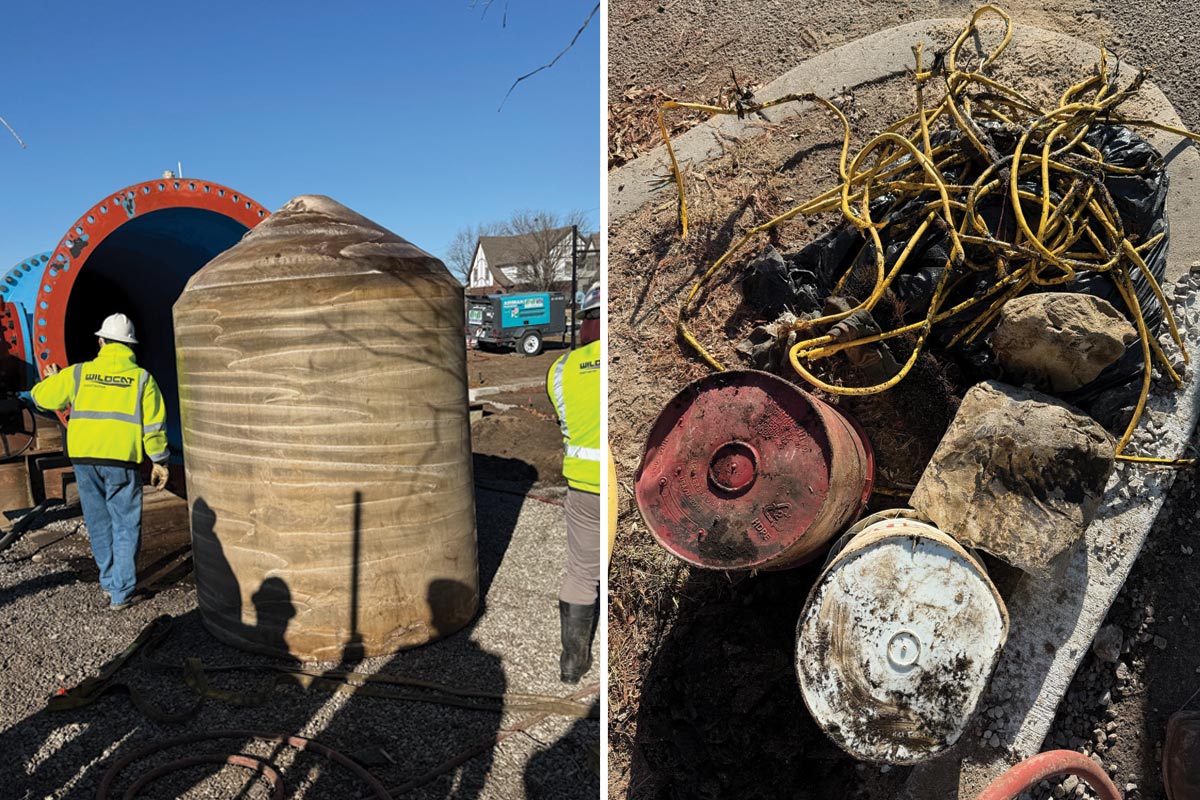
Progressive Pigging
A series of pig runs were performed, with each run using a slightly larger and more aggressive pig than the previous one. Pigs were selected based on their size, material and aggressiveness to effectively loosen silt. They also flushed debris and cleared the pipeline.
The first pigs used were LB Light-Density Bare Swabs, designed to dislodge initial silt buildup gently. These soft foam pigs ensured safe passage through the pipeline without causing damage.
Next, a medium-density bare pig was deployed to remove tougher accumulations. This flexible foam pig adapted to the pipeline’s contours. It effectively removed construction debris, including chunks of concrete, extension cords, five-gallon drums, and excess grout.
The final pigging runs utilized medium-density, crisscross foam pigs with bullet noses. These pigs provided more aggressive cleaning action to remove any remaining loose debris while preserving the integrity of the internal lining. The durable polyurethane crisscross coating enhanced abrasion resistance and scraping efficiency.
Each pig was inserted and secured before the system’s flow rate was activated. This propelled the pig through the pipeline. The pigs navigated around sharp bends, underneath the Arkansas river and maneuvered through a complex manifold system. They then made a final 90-degree turn at the retrieval point. Using a transmitter, pig locations were tracked to ensure pig progress. Crewmembers monitored the progress and reported on any anomalies. Most of the silt and buildup were removed within the first three runs.
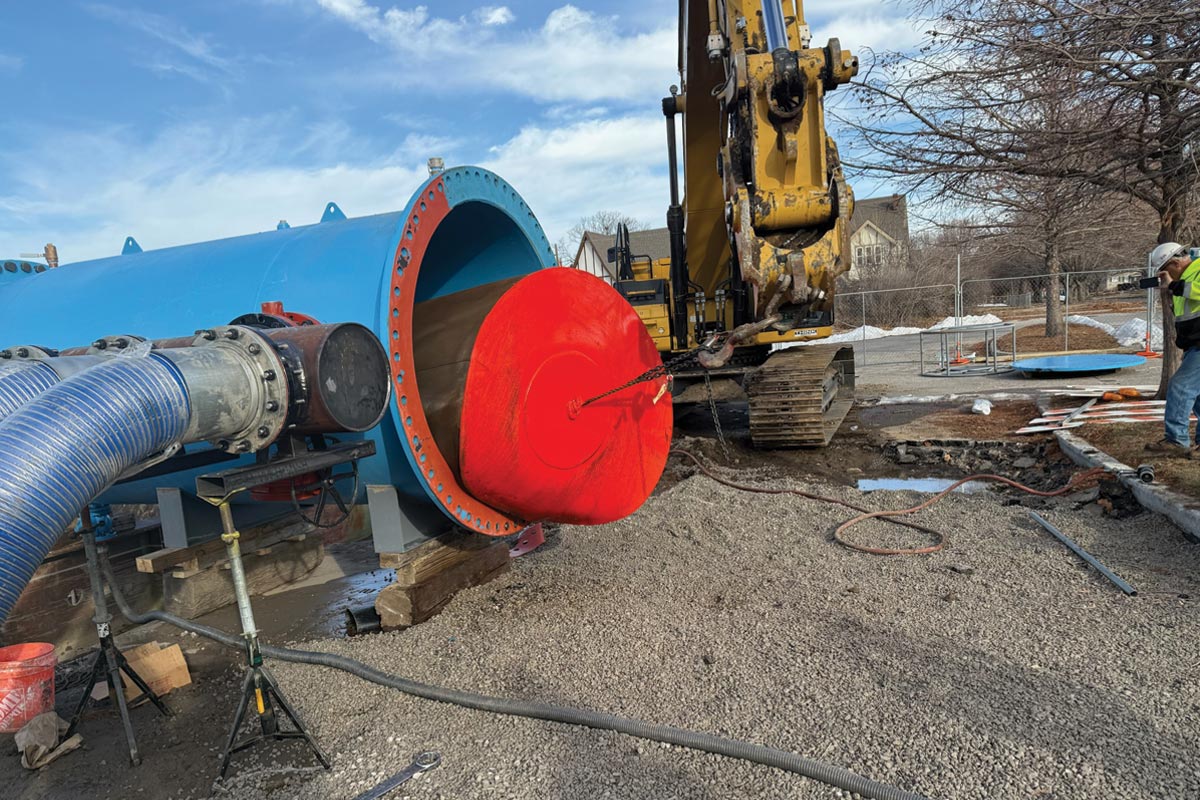
Challenges
The proposed retrieval site lacked sufficient space for the equipment and crews. An alternate location was identified that required diverting pigs into a newly constructed 2,000-ft section of pipeline that was not yet operational. The custom-built receiver was installed, and the site prepared.
Flow rates were skillfully controlled for each pig. This allowed a turn at a 90-degree angle through a tee and into the last section of pipe. There were also 48-in. butterfly valves at the retrieval point that needed to be shut to divert the pigs towards the receiver.
Elevation changes and multiple 90-degree bends added further complications. At approximately 2,000 ft before the final retrieval point, a crew member confirmed each pig’s passage through a critical turn. Water was diverted into a filter to slow the pig’s movement and control its final approach.
Working with specialized equipment and managing dynamic factors, such as ensuring sufficient flow rate for pig propulsion, required extensive planning and expertise. APS senior project manager Mitch Howe led the project. He recommended the use of an external pump to launch the pig into the pipeline. The pump was used beyond the point the system water flow could take over and push the pig through. After each pig run, Mitch evaluated the collected debris and the pig’s condition. Based on this, he determined the next pig type and the need for further runs.
Pigging Results
Five pig runs were successfully executed within the ten-week deadline on the largest-diameter pipeline APS has pigged. Careful selection and sequencing of pigs, with precision management of water pressure and flow, achieved thorough cleaning. They removed debris without compromising the pipeline’s integrity.
Final preparations included sanitizing, treating, and reinstalling butterfly valves. The Northwest Water Facility is expected to be fully operational after testing and securing the final permits.
Blake Murphey is president of American Pipeline Solutions.