
Proactive Repair Improves Twin Siphons Under Sturgeon Creek in Winnipeg
Through routine inspections of its sewer system, the City of Winnipeg Water and Waste Department looks to avert the disaster of an unexpected break and better plan for a routine rehabilitation or replacement of its aging underground infrastructure.
It was through these routine inspections that the department found that a pair of 450-mm steel and asbestos cement siphon lines – approximately 200 m in length – installed in the mid-1960s, were beginning to fail under Sturgeon Creek just before its outfall into the Assiniboine River. The discovery was made in 2019 and a plan was put into works to repair the siphons using cured-in-place pipe (CIPP).
“The one forcemain was in more delicate condition. The pipe had been reduced to within less than 10 per cent of what its original wall thickness,” says Brian Ratchford. “They were concerned it could start leaking at any time.”
Ratchford is the chief operating officer for Capital Sewer Services Inc., the contractor on the $1.1 million project. Capital Sewer Services (CSS) is a division of Capital Infrastructure Group (CIG), of Vaughan, Ontario.
The work took place in Fall 2019 and Winter 2020 to better avoid major wet weather events to avoid max flows in the lines and offering the contractor the ability to avoid bypassing the siphons. By working during low level events, one siphon was sufficient to carry effluent from Assiniboine Crescent, under Sturgeon Creek to a gravity sewer on Ashcroft Point.
The Water and Waste Department specified that the project be completed using CIPP and suggested products to be used, but at the end of the day it was up to the contractor to provide a certified design with a product that processes a long history of performance in similar applications.
Selecting the Right Product
“The cured-in-place product was chosen because of its versatility in terms of being able to be installed in a continuous, long, length and its ability to negotiate bends and offsets,” says Ratchford. “There were five vertical deflections varying between 12 and 22-degrees and then also a 45-degree elbow on the backside of the installation.”
CSS looked at its vast toolbox and decided that the optimal solution for this pressure pipe application would be the AquaCure RP liner from Applied Felts and vinyl ester resin from AOC.
“We used an enhanced tube from Applied Felts that has an inner layer of fiberglass reinforcement to give it additional hoop strength needed in a pressure pipe. I believe the internal operating pressure on this main was in the neighborhood of 15 psi,” says Ratchford. “That enhanced tube gives you superior physical properties, which means that it is also a thinner liner, which is important for flow characteristics. You’re keeping the cross-sectional area reduction to a minimum.”
Looking at the choice of resins, Ratchford says, “Most of our day-to-day CIPP work uses polyester resins, that’s the workhorse of the industry and used primarily in gravity applications. When we get into pressure pipe lines, we go to a vinyl ester resin. That gives you more flexibility, which is important in a pressure pipe. Utilizing a vinyl ester-based resin also provided superior elongation properties allowing the liner to accommodate varying pressures being applied particularly at the bends and offsets.”
RELATED: Rehabbing a Pair of Egg-Shaped Sewers in Winnipeg with Sliplining
Using this combination, according to Ratchford, restores structural integrity, provides long-term chemical resistance, improved flow characteristics, much smaller carbon footprint and, of course, little excavation, seamless, joint-free construction from end to end.
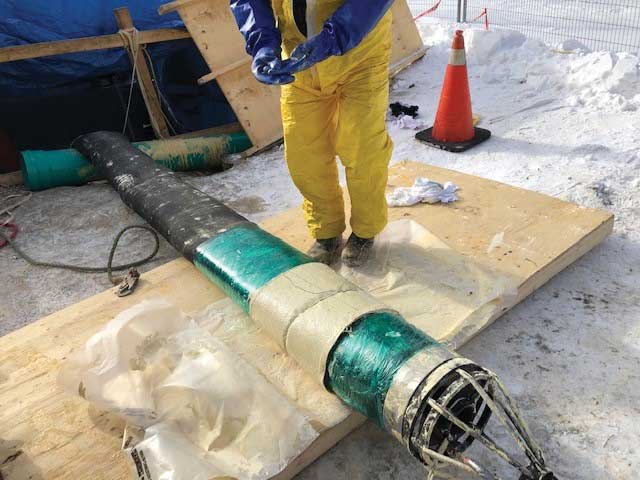
Prepping the Lines
When the crews arrived onsite for the project, the first order of business was one temporary shaft excavation needed to gain access to the upstream portion of the forcemains. Temporary access was gained through spool pieces that has been previously installed. These spool pieces were exposed, the lines drained, and the spool pieces removed providing the necessary access for cleaning and lining.
Cleaning a siphon, Ratchford notes, is trickier than a gravity sewer because the water is not carried away down the line leaving a clear view for the camera operator monitoring the operations. Instead, as the cleaning commences, the siphon fills with water.
To combat this, the Capital Sewer Services team used a flusher and vacuum truck for cleaning, operating on opposite ends of the line. Reaming operations were performed blind by progressing the reamer at a pre-determined rate.
Care was taken to ensure that the reamer was never stationary to avoid damaging the host pipe in its reduced structural capacity. Once a pass was completed, the reamer was removed, the line drained and inspected to gauge the degree of removal. This process was repeated until the degree of pipe preparation needed was achieved. “That was a little bit of a tricky affair,” says Ratchford.
RELATED: Capital Infrastructure Group Grows to Become a One-Stop Shop for Underground Construction Services
Ingenuity in the End
While the CIPP lining process was relatively straightforward, the Capital Sewer Services team relied on its experience to engineer an in-field fix to create an end seal for the project. The end seals are necessary to prevent effluent of migrating between the newly installed liner and the host pipe.
Initially, the crews tried off-the-shelf end seals. However, because of the thickness transition between the host pipe and the newly installed liner, those did not work. They ended up using an epoxy-based fiber reinforced product created in the field from its spot repair kits. These in-house end seals were able to maintain the forcemain’s pressure rating requirements while providing a smooth transition from the host pipe to the newly installed liner.
“The first forcemain took a little longer to complete as we worked on the end seal solution. The second one was right by the numbers and done in three to four days. We learned a few valuable lessons that we will be able to use on projects in the future,” says Ratchford.
Mike Kezdi is the managing editor of Trenchless Technology Canada.