Pipe Relining Project at the U.S. Naval Air Station
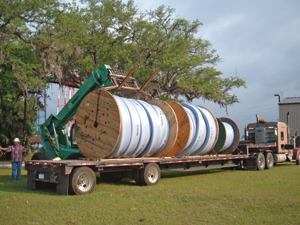
Ultraliner pipe delivered to the U.S. Naval Air Station
At the U.S. Naval Air Station (NAS) in Jacksonville, Fla., nothing can be permitted to interfere with the “mission.” So when culverts under the airfield needed rehabilitation, NAS Jacksonville had to find the least disruptive solution possible.
As Bill Meyer, the Navy’s airfield facility manager for both NAS Jacksonville and the Outlying Field [OLF] of the White House, explains: “I can’t close down the airport to fix the infrastructure by excavation and replacement. Airports can’t afford to tear up areas in the clear zone of the runways.”
NAS Jacksonville is familiar with pipe rehabilitation and had previously used trenchless pipeliners with some success. However, there were subsequent concerns related to quality control, risk of installation failure and, most critically, the risk of disruption to the mission of the air station. For current and future projects, NAS Jacksonville was actively looking for a solution.
SBagby & Co. Inc. proposed the use of Ultraliner PVC Alloy Pipeliner from Ultraliner Inc., Oxford, Ala. As a pre-manufactured pipe, all design properties — including flexural modulus, wall thickness and corrosion resistance — are established at the manufacturing facility under ASTM-prescribed quality control procedures. Field crews and site conditions have negligible impact upon design compliance. This higher level of quality control and consistency enables PVC pipeliners to be governed by ASTM product standards in addition to ASTM installation standards. Compliance with ASTM product standards helps to ensure that the product “as constructed” consistently complies with the engineer’s design assumptions, just as is the case with direct burial PVC pipes. The relative simplicity of installation also requires less experience to achieve a successful project.
After reviewing proposals from SBagby, NAS Jacksonville first awarded a smaller scale $380,000 pipelining contract to more fully evaluate the PVC pipeliners.
According to Steve Bagby, the first project consisted of approximately 4,000 lf of 15- to 30-in. pipe installed under roads and at the airfield, including a 500-lf stormwater pipe under runway 9/27. SBagby teamed with Engineered Lining Systems (ELS), Jacksonville, Fla., for this and subsequent pipelining projects.
Although an experienced pipelining contractor, use of PVC pipeliners was new to ELS. As a result, Ultraliner sent a field service crew to assist with the initial PVC pipeliner installations and to provide additional training support to ELS’ field crews. Everyone has been pleased with the results.
“We use other lining systems as well, but now we generally don’t even bring them up unless they have a specific advantage for a project,” explains ELS vice president Gary Pender. “We now use the PVC pipeliners almost exclusively. We did check out all of the other available lining systems; but other systems just don’t compare. The Ultraliner PVC Alloy Pipeliners are a proven technology. When problems do occur, they are easy to correct with very little losses. We had an initial learning curve, but it was very short.”
NAS Jacksonville was equally pleased. As the engineering tech for the Navy’s facilities engineering and acquisition department, Bob Cabral handles the relining of pipes on NAS Jacksonville.
“Our driving force is to restore the pipe to its original or better condition while mitigating the maintenance costs of repairing roads and pipes. I believe PVC pipeliners are going to be the solution to that problem,” explains Cabral. “The PVC pipeliner appears to be a high-quality material with no seams and good laminar flow of the fluid. It is non-biodegradable and can handle the harsh environment. The PVC pipeliners have stopped the infiltration, erosion and pothole problems.”
Subsequent to the initial successes, two more projects with additional add-ons have been awarded for a total of more than $3.5 million worth of trenchless rehabilitation completed for NAS Jacksonville by the team of SBagby and ELS to date.
The second project consisted of more than 12,000 lf of 8- to 15-in. sewer pipe, and the third and current project consists of approximately 8,000 lf of 24- and 30-in. pipe. The projects have become increasingly challenging as the team of SBagby and ELS have proven their responsiveness, as well as the capabilities of PVC pipeliners to NAS Jacksonville. And with less than 25,000 lf of PVC pipeliner installation experience, the ELS crews are already proving capable of meeting all of NAS Jacksonville’s needs.
Two-thirds of the current pipelining contract are within the sensitive airfield area.
“We’ve had no negative impact on the flight operations. With other forms of repairs we’ve had to shut down runways for days, and with excavation in the past, we’ve had weeks and months of shutdowns, which is not acceptable. With the PVC pipeliners, we can shut down for an evening, weekend or holiday and come the next working day, everything is fixed and it is like they weren’t even there. The speed makes scheduling so much easier,” says Meyer.
“There has been minimal disruption to NAS Jacksonville activity. We went out and put a pipeliner in under the airfield while planes were landing and taking off. The runway never had to shut down. Flight time is valuable and the mission would have been impossible to continue if we had closed the runway for pipe repairs,” Cabral adds.
“There has been no barricading or detouring, but rather we have been able to line while the roads and runways are in service. It is a major help to get things repaired without disrupting operations. We have been able to line the pipes without anyone knowing we’ve been out there.”
And Cabral gave high marks to the ELS and SBagby teams. “That’s an extremely good crew of guys. They believe in the PVC pipeliner product and are doing an outstanding job,” Cabral says. “Any problems get resolved immediately. You can usually tell when there are difficulties by how the crews behave. With these crews, you never hear anyone yelling; everyone is easy going. The productivity has doubled as the project has progressed. The learning curve appears to be almost behind them now. They are very proficient. It is like an automatic machine.”
Despite ELS’ success installing the PVC pipeliner on its own, Ultraliner Inc. recently sent one of its top field service managers, Lee Trotter, to assist with a particularly challenging installation. NAS Jacksonville needed to line a 30-in. pipe running more than 500 ft under a runway.
The resulting PVC pipeliner was approximately 17,000 lbs in weight and had to be coiled on a specially manufactured 10-ft wide reel.
“The installation started at 6 a.m. and was 100 percent processed by 3 p.m,” Pender says. “Lee [Trotter] has a good feel for it; he knew how to make adjustments. I really appreciate his help. I like the support Ultraliner gives; they always find a way to get someone down to help us when we feel we need it.”
L. Grant Whittle is vice president of Ultraliner Inc., based in Oxford, Ala.