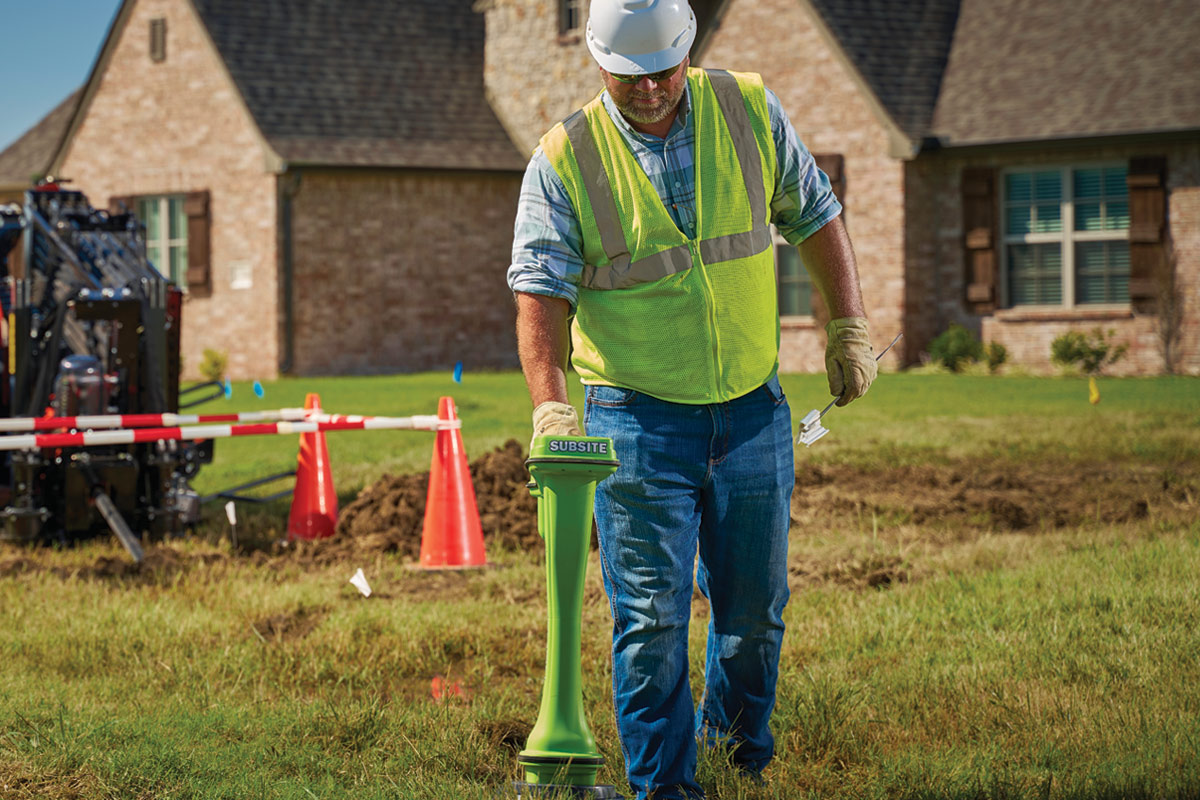
Navigating Nuances – Optimizing Jobsite Setup for Effective HDD Guidance
A directional drilling jobsite is a complex one, requiring knowledgeable operators who are well-versed in managing the intricate combination of mechanical and electronic systems that comprise the HDD process.
For a successful directional drilling installation, every component of the jobsite must function seamlessly. One of the most critical features of a directional unit is its downhole maneuverability, making the HDD guidance system indispensable.
This is particularly true as underground environments become increasingly congested, heightening the risk of damaging utilities or existing infrastructure.
Given the challenging nature of underground environments, HDD guidance best practices and jobsite procedures should aim to simplify rather than complicate operations.
OEMs like Subsite are continuously innovating their products to streamline the HDD locating process, enhancing productivity, safety and efficiency.
Here are some key insights to keep in mind.
White Lining for Damage Mitigation
White lining the intended bore path is a crucial step in mitigating damage during HDD projects. By marking the bore path, utility owners can better understand where the drilling will occur, allowing them to identify and locate utilities that need to be addressed before drilling begins.
This preemptive measure ensures that utilities are properly marked and potholed, reducing the risk of accidental damage.
Additionally, walking the bore path helps in planning for potential obstacles and utilities that may be encountered, further enhancing the safety and efficiency of the drilling operation.
Understand Interference Types
Interference on a jobsite is a crucial factor when HDD professionals decide which frequency to use. It is imperative that underground professionals fully understand the two types of interference: active and passive.
Active interference includes any infrastructure with a live current running through it. Common examples are power lines, fiber-optic lines and cellular lines. While underground construction professionals primarily focus on what lies beneath the surface, it is also essential to identify any overhead active interference, that could impact frequency.
Passive interference often results from current or previous structural developments, such as metal, guard rails, chain link fencing, underground steel drains, reinforced concrete, or rebar. Like active interference, sources of passive interference can also be above ground, causing disruptions to your guidance equipment.
Understanding these types of interference is essential for ensuring that HDD professionals operate guidance equipment correctly, thereby contributing to jobsite success.
Seamless Steering
To drill straight ahead, rotate the drill string and drill head while applying forward thrust. To change direction, stop the rotation and position the slant face or bent sub housing opposite of the desired path. With traditional slant face technology, the drill head moves away from the slant when thrust is applied without rotation.
Bent sub housing systems, used with two-pipe or mud motor systems, move in the direction of the bend when thrust is applied without rotating the outer pipe. The operator must monitor the drill head’s orientation using electronic tracking and HDD guidance systems for precise direction changes.
There are two basic guidance systems: walkover and non-walkover wireline. Walkover systems use a transmitter in the drill head and a handheld receiver operated by a crew member above the drill head, relaying data to the drill operator. Non-walkover wireline uses a cable to transmit data from the drill head to the surface.
Input Utilities into a Bore Plan
To ensure the accuracy and safety of HDD operations, it is crucial to establish appropriate setback distances and meet minimum separation requirements to avoid intersecting with existing utilities.
Utilizing pre- and post-inspection/locate reports will aid in generating a precise bore plan. Additionally, validating the plan by exposing utilities to confirm their diameter and depth before inputting them into the bore plan is key for mitigating risks and ensuring a safe and successful project.
Prepare the Beacon
To optimize the performance of the HDD guidance system, connect to the beacon via Bluetooth to configure the frequency and power settings. Carefully place the beacon or sonde in the drill head, ensuring the electronics are oriented towards the intended target.
By utilizing bore path analysis (BPA) outputs and conducting a thorough visual inspection of the jobsite, HDD operators can select the appropriate frequency to ensure the job is completed safely and effectively. This meticulous approach enhances the precision and reliability of the drilling operation.
With a wide range of unique variables on any jobsite, underground construction professionals will want to ensure that their HDD guidance equipment has two key features to help them successfully complete the job. The first is to select HDD guidance equipment that has a wide range of frequencies and the ability to change frequencies in the middle of a job.
The second key feature is selecting equipment that has multiple, simplified interfaces. These interface options ensure that operators can quickly and easily select the correct frequency, increasing operator productivity.
Having the right tools on hand will help ensure that HDD professionals are able to select the right frequency or frequencies needed for the jobsite, resulting in damage mitigation and increased efficiency.
Connected Calibration Process
To ensure accurate calibration of the HDD guidance system, it is essential to perform the calibration in a clean environment, away from utilities and other metallic objects that could interfere with the process.
To simplify the calibration process, Subsite’s Marksman+ automatically populates selected frequencies using the suggestions from the Bore Path Analyzer. With active Bluetooth communication and the depth confirmation screen, operators can select and verify each calibrated frequency without putting the beacon in sleep mode, a traditionally laborious process.
The tracker automatically selects four frequencies based on the BPA scan, with calibration taking approximately one minute for each selected frequency, depending on the noise environment. It’s important to note that the beacon will not calibrate high power if the battery power is insufficient.
Once calibration is complete, the Marksman+ switches to the depth calibration screen, allowing operators to confirm the calibration distance by highlighting each frequency.
Additionally, to perform down hole frequency changes, operators can use the set beacon feature on the display to follow a roll sequence and set or chance the beacon frequency.
Verification of calibration should be conducted by checking the depths at 10- and 15-ft intervals. It is important to confirm these depths within the calibration screen rather than in walkover mode to ensure precise measurements. This step is essential for maintaining the reliability and effectiveness of the guidance system.
Checking Noise Floor
The noise floor is the depth at which communication (pitch/roll) is lost between the beacon and tracker. Ensure the beacon is “off” or “asleep” and force depth on the tracker throughout the intended bore path every 20 to 30 ft or at known points of potential interference.
Pitch and roll measurements are fundamental for effective HDD guidance. However, new technology allows HDD operators to work even smarter as they navigate crowded underground environments. Paired together, the knowledge of pitch and roll and the latest HDD guidance technology will ensure even the most convoluted jobsite is sufficiently prepared to drill.
Monitoring Roll
All brands of HDD guidance equipment use a clock face to monitor roll, which appears on displays of handheld and remote receivers. Most models divide the clock face into 12 segments, although some divide it into 24 segments.
The position of the slant face is indicated on the clock face. To change the bore path, the operator slowly rotates the drill string until the “hand” on the clock is in the position that will result in the desired direction change.
- 12 o’clock takes the drilling head up.
- 6 o’clock is down.
- 3 o’clock is right.
- 9 o’clock is left.
The face can be positioned at any point on the clock face — 2 o’clock takes the head up and to the right, 8 o’clock is down and to the left, and so on. A remote display is useful for making precise direction changes, reducing the opportunity for mistakes during radio communication between the crew member with the receiver and the drilling unit operator.
Understanding Pitch
Pitch is displayed using an up or down arrow and the percentage of deviation. Pitch is calculated as rise or fall divided by length. For example, a 1 percent change in pitch over a distance of 100 ft is the rise or fall of 1 ft.
Pitch informs the operator of the downward angle necessary to take the drill head to the depth where the bore path will level off. Pitch information is also used when the drill head needs to be aimed upward toward the targeted exit point or to avoid obstacles. Additionally, pitch helps the operator maintain the drill pipe bend radius within acceptable tolerances.
Bending the pipe more than the allowable maximum bend radius will damage the pipe or cause breaks at joint connections. The minimum bend radius varies with the size and model of the machine and the brand and size of the pipe, so it is essential to know manufacturers’ specifications before beginning any installation.
Ensure Drill to Tracker Communication
To maintain effective communication between the drill and the tracker, it is essential to verify that both the tracker and the display are operating on the same channel. Additionally, ensure that the drill lock codes are set for “lock out tag out” to adhere to safe practices when changing tooling. Finally, confirm both are operating on the same channel by checking the communication sync bars on both the tracker and the display.
Underground Awareness
The successful execution of HDD projects hinges on the seamless integration of best practices for HDD guidance systems. The labyrinth of modern underground environments, with their myriads of utilities and potential interferences, underscores the necessity for precise and reliable HDD guidance.
By implementing strategies such as white lining, understanding and mitigating interference, and ensuring robust drill-to-tracker communication, HDD professionals can navigate these challenges effectively.
The continuous advancements by manufacturers like Subsite in enhancing the locating process further empower operators to achieve higher levels of safety, efficiency, and accuracy. Embracing these best practices not only protects existing infrastructure but also ensures the overall success and productivity of HDD operations.
Braxton Smith is a product manager at Subsite.