Mud Systems: Use of a Centrifuge Can Play Key Role in Mud Success
October 1, 2008
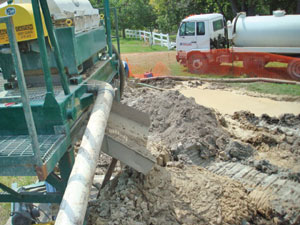
The mud systems market has noted a significant increase in activity by HDD contractors to employ new technology to stay ahead of solids control, drilling fluid and disposal related problems. Recently, Kem-Tron Technologies worked with Parker Lane Drilling, Euless, Texas, to tackle some mud disposal issues driven by out-of-control mud weight.
The Dallas Fort Worth (DFW) Metroplex is an absolute hotbed of drilling projects, fueled by the oil and gas activity in the Barnett Shale. Typical soil formations range from hard rock and sand and almost every shot will include a substantial section of clay. These clays tend be reactive in nature and break down rather quickly through both hydraulic functions (turbulence from circulating in the mud) and mechanically. This breakdown of clays leads to many fluid-related problems.
The most obvious problem associated with clay breakdown is the increased mud weight. The cleaning systems employed will vary widely in performance, based on screening area available and what size mesh count can be utilized. The tighter mesh that can be used on the scalp cut will generally be the basis for performance. Where the goal is to eliminate the clays as soon as possible to limit the mechanical breakdown associated with centrifugal pumps, hydrocyclones, mud guns and hoppers, mesh count is key.
The knee jerk response to mud weight build up is to dump and dilute the system in an attempt to keep the fluids from resembling pancake batter. A better response would be to dump the entire system and start fresh, but the cost of disposal prevents this action. The problem with dilution is the creation of more drilling waste. Once the clays have broken down below 20 micron, they can no longer be removed with conventional mud systems and will quickly turn the dilution water into more heavy weight drilling waste.
The heavy fluids create unstable boreholes due to increased annular velocities and increased downhole pressures, which often lead to a frac-out along with a decreased rate of penetration and reduced carrying capacity of fluids. Parker Lane was tackling all these problems but was more concerned about downtime and disposal.
When working in the DFW area, Parker Lane workers found themselves hauling spoiled drilling fluids one to two and a half hours round trip for disposal with two vac trucks running all day, everyday. So, putting the cost of fuel, disposal and manpower and liabilities aside, the time consumed hauling and waiting on fluids created a significant cost in downtime.
To counter this problem, Kem-Tron rigged its KT-1448 centrifuge package, capable of a 2-micron cut point. Centrifuges, will in addition to controlling mud weight, increase ROP, and reduce downhole pressures and the risk of a frac-out. The pilot bore was drilled in two days without any substantial buildup of clays and no water additions other than to account for hole volume.
According to Brent Lane, crews would have hauled 12,000 to 20,000 gals to the disposal facility just to complete the pilot bore. Speaking with Parker Lane personnel, on a typical bore the water pump pressure would gradually begin working up toward 100 to 150 psi, at which point the drilling fluids had become so solid laden and thick that they needed to be hauled off. On this demonstration of the KT-1448, the water pump pressure never exceeded 50 psi and the drilling operation was able to run continuously without waiting on water to make up new mud or to haul off old mud.
Parker Lane, operating a 330,000-lb rig was moving substantial amounts of fluids, in excess of 300 to 400 gpm. The KT-1448 has a hydraulic rating of 180 to 200 gpm and when handling high solids content, will actually only handle 80 to 120 gpm. Despite the difference between the circulating volume in the borehole and the KT-1448 handling capacity, the equipment was successful. Particle distributions are rarely considered on most HDD projects but it is clear that in the DFW area, there is a large percentage of solids in the 25 micron and below range, also termed low gravity solids.
Normal operations would allow these low gravity solids to accumulate in the fluids and become the predominant particle size in the distribution. Utilizing the centrifuge, Parker Lane was able to prevent the buildup altogether by capturing low gravity solids (LGS) down to 2 micron on a continual basis and without recirculation.
So despite the flow rate disparity, it is clear that by handling the LGS on a continual basis, the flow rate is not the most critical aspect to consider.
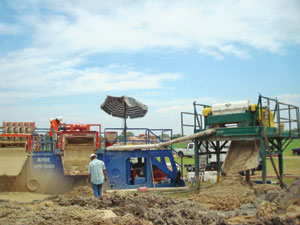
Kem-Tron utilizes a progressive cavity feed pump to move the drilling fluids into the bowl. PC pumps allow for a constant feed pressure and gpm with very little fluctuation. In order to maximize the efficiency of the centrifuge, feed pressure and gpm should remain constant. PC pumps will also allow for easy control of the feed rate. Pending the soil conditions, feed rates can be adjusted at the pump in seconds without having to pinch valves or guess at the gpm.
The liquid discharge of a centrifuge is also a gravity process. The liquid is discharged into the skid and typically plumbed back to the active system with PVC pipe or flexible hose.
The demonstration was considered by both Parker Lane employees and Kem-Tron to be a huge success. Parker Lane was able to drill a 24-in. diameter hole over 1,500 ft in length in just seven days from rig up to pulling pipe. Throughout the bore, not one drop of drilling fluid was hauled off as waste. Mud weight never exceeded 9.0 ppg, sand content of the system was kept at or below 1/8 percent and viscosity was kept at a prescribed 50 to 55 seconds.
In addition to the success of this bore, Parker Lane was also operating a 100,000-lb rig nearby. This crew completed a 400-ft shot and hauled all the mud to the 330,000-lb site and dumped. Lane was able to pick this mud up and clean it, allowing him to avoid disposal from two rigs using only one centrifuge.
When cost of disposal and wear parts are prohibitive, dump sites too distant or you just like to keepĀ your drilling rods turning to the right, a centrifuge may be your next step.
Chuck Skillman is business development manager at Kem-Tron Technologies, based in Houston.