Microtunneling in Montgomery
February 1, 2009
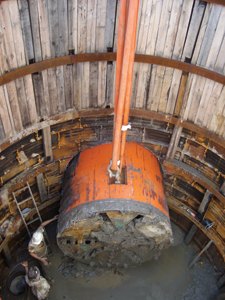
One recent project was the Lower Catoma Interceptor Replacement, part of the Wet Weather Improvements Phase III program. The project was designed to replace an aging interceptor and increase conveyance capacity to the Catoma Wastewater Treatment Plant. The Lower Catoma Interceptor Replacement project, which involved 37,000-lf of sewer pipeline construction, was awarded to SJ Louis Construction of Texas Ltd. The route of the pipeline crossed CSX railroad tracks in two locations, as well as Old Selma Road and Mobile Highway.
To avoid shutting down these routes, the board, CH2M HILL and the general contractor opted to employ microtunneling. “Microtunneling was an attractive option because it works in saturated soils where conventional boring methods won’t work,” said Bill Henderson, MWWSSB assistant general manager.
Bradshaw Construction Corp. of Ellicott City, Md., was the subcontractor for the microtunnel crossings. Bradshaw is a specialty construction firm with a long history of tunneling. The company has made a name for itself for completing difficult projects in all types of ground using all types of methods. This project was particularly challenging given difficult ground conditions and shallow cover for the crossings.
Bradshaw’s scope of work involved the construction of eight liner plate shafts — four launch shafts 24 ft in diameter and four receiving shafts 16 ft in diameter. The four crossings ranged from 114 to 213-ft long to install 78- to 96-in ID pipe.
“The biggest challenge of the crossings was the fact that they were very shallow — in some cases there was as little as 6 ft of cover,” said Bradshaw Construction microtunneling manager Grahame Turnbull.
Another difficulty was the size of the crossings and a requirement that there could be no more than 2 percent overcut between the OD of the microtunneling machine and the OD of the jacking pipe. Because of the different sizes of pipe that needed to be installed, that meant that Bradshaw would have had to use two different microtunneling machines or use a machine that could be “skinned up,” which involves putting a larger shield and cutterhead on a machine.
Given the limitation on the amount of allowable overcut, Bradshaw did not have a machine in its fleet that could accommodate the diameters of both bores. Additionally, microtunneling equipment manufacturers that supply the North American market build standard sizes that did not meet the requirements of the job. So, Bradshaw turned to RASA Industries Ltd. of Japan to custom-build a new microtunneling machine.
RASA is a longtime builder of microtunneling machines in the Asian market, and Turnbull had known of its capabilities from past experience “We looked around the world for any manufacturer we could find, and RASA committed to building the size we needed within the timeframe we needed it.”
The schedule was critical because the tunneled portions of the Lower Catoma Interceptor Replacement needed to be done in advance of the open-cut.
The unit supplied by RASA was a Unicorn 1900 slurry machine with an electrically driven cutterhead with face access to change the cutters. The base machine had a diameter of 2,105 mm (82.87-in) with a factory-built skin set and cutterhead that enlarged the diameter to 2,470 mm (97.25-in). The machine provides 340,000 Newton meters of torque. The main jacks provided 1,000 metric tons of maximum thrust, upgradable to 1,500 metric tons. The jacking frame steel fabrication and entry and exit seals were manufactured by Microtunneling Inc.
Going Underground
The microtunneling portion of the project involved two crossings of the CSX railroad, Old Selma Road and Mobile Highway. Ground conditions ranged from poorly graded sand and gravel to clayey sands with poorly cemented sandstone in the invert in some crossings creating a mixed face condition.
The first crossing, under Old Selma Road, consisted of installing 202 ft of direct jack 78-in ID HOBAS pipe. The ground conditions ranged from well graded to silty sands and gravels. The first crossing was completed without incident so Bradshaw’s team set its sights on the first railroad crossing.
Bradshaw wanted to complete the first drive using the base machine to get a better feel for how it would handle skinned up to the larger diameter. Steering was critical, as the tunnel was not only under shallow cover, but also had a 0.00062 slope angle.
“With the machine skinned up it weighed in excess of 60,000 lbs, with most of the weight toward the front of the machine,” Turnbull said. “We were concerned about how the machine would steer, but it performed very well.”
Turnbull said the crew used a laser-guided system aided by computer interpretation to steer instead of using stroke sensors in the steering cylinders.
The first CSX crossing (CSX-1) involved a 114-ft crossing using 96-in. Permalok casing (with 78-in. HOBAS carrier pipe) through well graded to silty sands and gravels. The team constantly monitored slurry pressures and settlement points to help identify any potential settlement concerns. Despite the team’s effort, settlement occurred that was promptly addressed by CSX railroad crews. On the advice of the manufacturer, Bradshaw reduced the face opening from 50 to 25 percent open prior to the next crossing. The purpose of reducing the face opening was to help limit ground loss and help reduce damaging settlements. The modifications proved successful in reducing ground loss and limited settlements to acceptable levels on the remaining crossings.
One key to success when dealing with settlement induced by tunneling was to maintain communication with CSX railroad crews so that the settlement did not hamper railroad operations. “We were in constant contact with the railroad,” Henderson said. “They had a representative onsite at all times and a flagman with a radio to help direct train traffic.”
Originally, the contract called for the first crossing to be the CSX-1 crossing, but because of completing the Old Selma Road Crossing first, the machine only had to be reconfigured and the skin swapped once rather than twice as the original schedule dictated. “The process of changing the skin took two working days,” Turnbull said.
After getting approval, Bradshaw moved forward with the next CSX railroad crossing (CSX-2), a 122-ft railroad crossing through clayey sands and gravels, again installing Permalok casing with a HOBAS carrier pipe. Based on the experience gained from the previous crossing, the crew was able to complete the drive without incident.
Bradshaw then removed the skin and reset the machine to its original configuration keeping the 25 percent face opening on the cutter head to complete the final drive, a 213-ft shot under Mobile Highway through poorly graded sands and clay, with weakly cemented sandstone in the invert. The mixed face conditions posed some challenges for the crew in steering, tunnel advance rates and face control but the drive was successfully completed without incident.
All pipe has been laid and crews are preparing manholes and final surface work in advance of diverting flows into the new interceptor, which is expected to be online by April 2009.
James W. Rush is editor of Trenchless Technology.