Limestone No Match for Auger Boring System
May 1, 2008
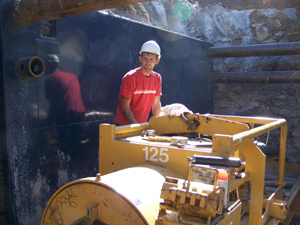
Back in the mid-1980s, the Tennessee Department of Transportation began an initiative to widen this primary east-west route that serves southern Tennessee. The project spanned 10 counties from Memphis to Grundy County’s I-24. In total, more than 266 miles of the highway would be widened to a four-lane route. The goal: help stimulate growth and economic development in the region.
The project has moved along smoothly for 22 years with the help of residents, community leaders and contractors who know how to deal with the ground conditions. Tennessee is known for its music, food, whiskey and rock. That’s right — Tennessee is full of high-quality limestone.
Mike Herren is the president of Mid South Utility Contractor, Baxter, Tenn. Herren got his start in the underground business in 1992. In 1993, he got his first break, taking over the maintenance work for a local water utility district. This project helped to catapult his business and soon he was installing water, sewer, gas and telecommunications lines throughout the region. Today, Mid South Utility Contractor specializes in the installation of water, sewer and gas lines and is known for its expertise in boring — especially in rock.
Mid South Utility Contractor was contracted to relocate all of the water, sewer and gas lines along a six-mile stretch of U.S. 64 that passed through Fayetteville. Crews installed 2.5 miles of sewer, three miles of force main sewer, three miles of natural gas lines, 2.5 miles of waterline and 42 manholes. The project took two years and required Herren to test his boring skills.
“The majority of the lines were open-cut, but we had to complete 20 bores ranging from 60 to 120 ft in length under the highway,” says Herren. “The bores accounted for 30 percent of our work on the project.”
The project required Mid South Utility Contractor to install 20-ft sections of steel casings, ranging from 12 to 30 in. in diameter. The water lines were installed under the highway at a depth of 6 to 8 ft, while the sewer lines had to go in at 15 to 20 ft on grade.
“We’ve been auger boring a long time in rock, but not at the precision that we had to be on these gravity sewer lines,” says Herren. “We knew we needed some help and we called McLaughlin. They came in with their rock system and customized it to our project.”
The McLaughlin rock system was designed specifically for solid rock applications. The system features a pilot head with three roller cones set up to cut 6 ½ in. on the outside diameter (OD). Behind the pilot head are two 5-ft long stabilizers with ribbing on them to bring them up to the OD of the pilot head. When you start to drill forward, the stabilizers fill the void created by the pilot head and steady it for an accurate shot. The pilot head and stabilizers are attached to a drill stem that allows water to flow through to the head, flushing the cuttings and keeping the pilot head cool. Herren used the rock system with his McLaughlin 36-42C auger boring machine.
The sewer bores began by creating and shoring a pit 20 ft deep by 32 ft long. The pit was set 10 ft back from the new road. Once the pit was set, the boring machine was positioned.
Mike Moore, vice president of sales for McLaughlin, was on hand to train the crew on how to use the rock system.
“Since you cannot steer the auger, setting up the machine is key,” says Moore. “It needs to be in a straight line in the direction you want to go and at the grade of the bore. We also had to make sure the machine was square. This takes the most time and the rock will keep you in once you get the machine square.”
Once the pilot head was square, the crew began boring and continued to add drill stem until they reached the other side of the road. When they reached the receiving pit, the crew continued to rotate the pilot head forward and began pulling the stem back out of the hole.
During this process, we pumped water from the receiving pit back toward the machine to help flush out any remaining cuttings,” says Moore.
When the pullback was complete, the rib stabilizers and pilot head were left in the hole and a 16-in. reamer head was attached. The reamer head featured a series of roller cones up to the OD. On the back side of the reamer, the crew attached a standard auger and the first 20-ft section of casing. The crew began to ream the hole and continued to pump water from the receiving pits back into the boring machine to keep the head cool and flush the cuttings back into the pit. The 20-ft sections of casing were welded together as the bore progressed.
“The pilot hole is the slowest part of the process,” says Herren. “It takes a couple of days to get the pilot hole completed and a total of four days to complete each bore.”
Once the new main lines were in place, the contractor began the process of laying new service lines to each home and business along the route. The new lines and old lines were in service until all customers were connected to the new lines. The old lines were then abandoned to keep service disruptions to a minimum.
“It was a pretty mean job, I’ll just put it that way,” says Herren. “This project was right in the middle of town among all the homes and factories, so we had limited work space. But the system worked well and helped us successfully complete the project. I can’t say enough about the support we received from McLaughlin — they are good people, good teachers and have excellent products.”
Greg Ehm is a technical writer in Des Moines, Iowa.