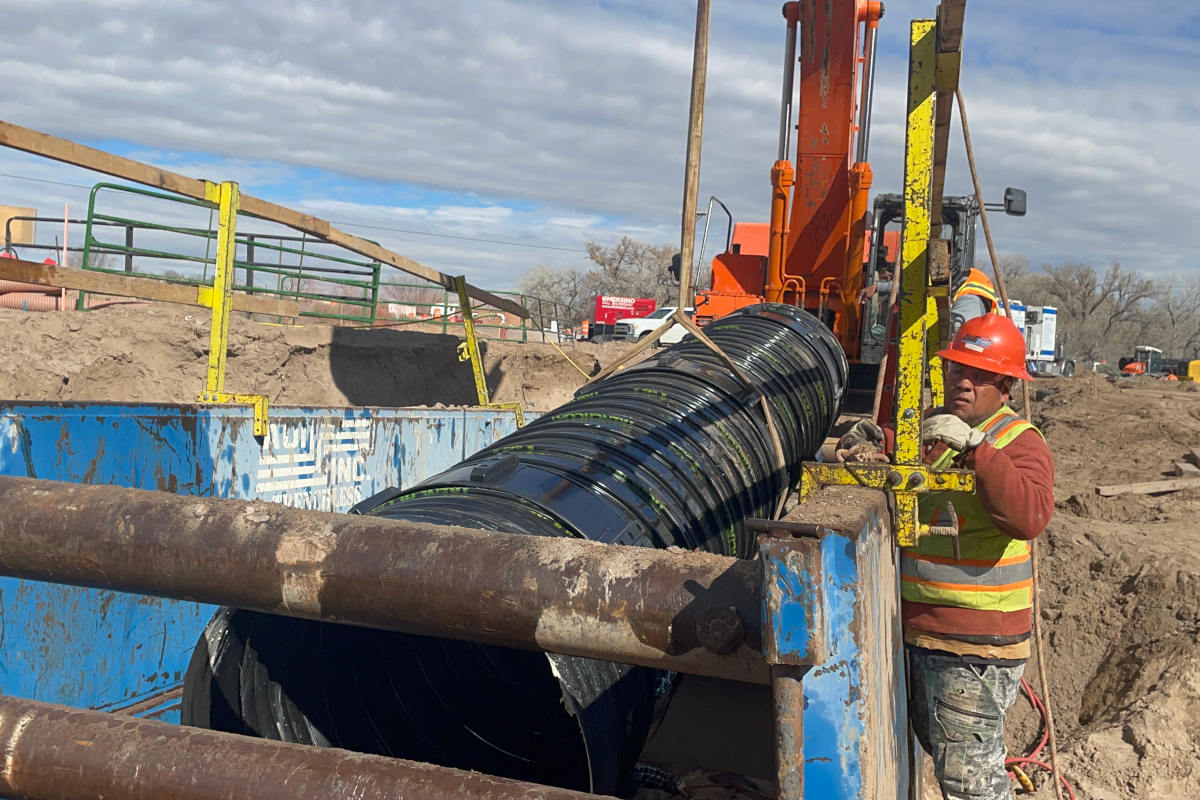
Isleta Pueblo Emergency Irrigation Pipeline Repair
In October 2023, the Middle Rio Grande Conservancy District (MRGCD) encountered a critical infrastructure failure. A 42-in. diameter irrigation pipeline, buried deep beneath New Mexico State Road 147, experienced a catastrophic collapse.
This pipeline, originally installed in 1978, had surpassed its intended service life. Its failure posed an immediate threat to the agricultural activities it supported. The conduit was essential for transporting water from the Rio Grande River to farms on the west side of the Isleta Pueblo. It had the capacity to convey tens of millions of gallons daily during peak irrigation seasons.
Challenges and Constraints
The collapse occurred at the main entrance to the Isleta Pueblo on NM-Highway 147. This is a critical access point for the community. Closing this roadway for a traditional open-cut excavation and pipe replacement was not a viable option. It would have severely disrupted daily life and access for residents.
Additionally, the pipeline’s location, approximately 20 ft beneath the surface and parallel to the Rio Grande River, presented further complications. These included a high-water table and the presence of culturally sensitive areas. The high-water table made traditional excavation methods impractical. The potential for groundwater intrusion and soil instability posed considerable risks to both the construction crew and the existing infrastructure.
Given the historical and cultural significance of the Isleta Pueblo lands, extensive coordination with tribal authorities was necessary. This ensured that construction activities respected sacred sites and minimized disruption to traditional practices.
The urgency of restoring the pipeline while balancing these constraints required a solution that was both technically feasible and culturally considerate.
Evaluating Options
Given these constraints, the MRGCD, in collaboration with AUI Inc., explored several trenchless rehabilitation methods. This aimed to address the emergency efficiently while minimizing surface disruption.
After a thorough evaluation, the team determined that employing a tunnel boring machine (TBM) would be the most effective approach. This method allowed for the installation of a new 50-inch steel casing beneath the roadway without the need for extensive excavation. Thus, it preserved the integrity of the surrounding environment and ensured minimal impact on local traffic.
Tunnel Boring Commences
The project commenced with the dewatering of the site to manage the high groundwater levels adjacent to the Rio Grande River. This step was crucial to create optimal conditions for the TBM operation. It included the excavation of the entrance pit and ensuring stability during the tunneling process. Without proper dewatering, the high-water table could negatively impact soil stability. This could lead to tunnel collapse or misalignment of the bore path.
During the initial phase of tunneling, the TBM encountered an unexpected obstacle: an abandoned 36-inch corrugated metal pipe, as indicated by as-built drawings from 1958. This unforeseen obstruction necessitated a realignment of the bore path. This required quick thinking and adaptability from the project engineers.
Once the TBM was repositioned, the 50-inch steel casing was successfully installed through the collapsed section. This set the stage for the next phase of rehabilitation. This method not only ensured the stability of the pipeline but also demonstrated the effectiveness of modern trenchless technology in addressing complex infrastructure challenges.
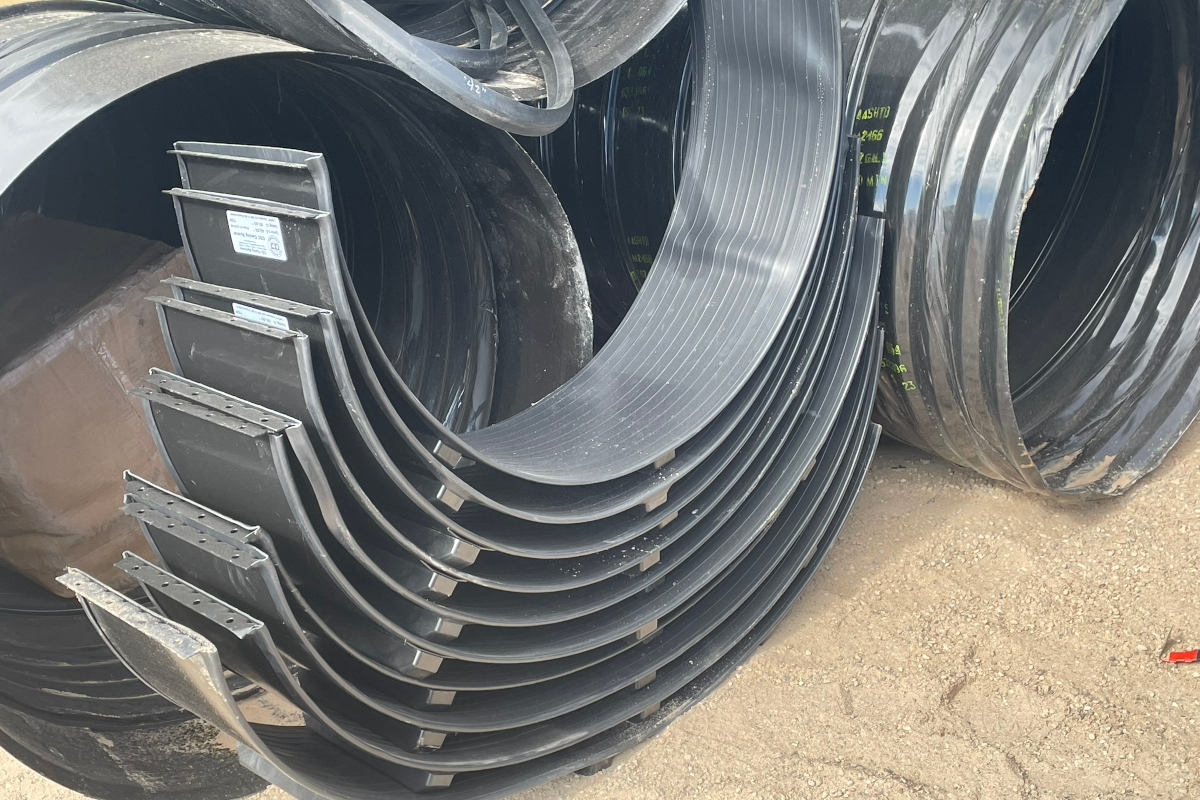
Selecting Polymer-Coated Spiral Rib Liner Pipe
For the relining of the newly installed casing, the team selected a 42-inch polymer-coated ULTRA FLO spiral rib liner pipe system manufactured by Contech Engineered Solutions. This choice was influenced by several key factors:
- Hydraulic Efficiency: ULTRA FLO spiral rib pipe features a smooth interior surface, resulting in a Manning’s n value of 0.012. This low friction coefficient enhances hydraulic capacity, allowing for efficient water flow even under high-demand conditions.
- Structural Integrity: The pipe’s exterior is designed with box ribs that provide exceptional structural strength. This ensures the pipe can withstand external loads and internal pressures without compromising performance.
- Corrosion Resistance: Given the site’s soil analysis, which indicated slightly corrosive properties, the polymer-coated ULTRA FLO offered enhanced resistance to chemical corrosion. This extends the pipeline’s service life.
The decision to use a polymer-coated solution was also driven by its longevity and low maintenance requirements. The polymer coating provided an additional protective layer against environmental degradation. This ensures that the pipeline remains functional for decades without the need for frequent repairs or replacements.
Installation Process
The ULTRA FLO spiral rib liner pipe was manufactured in 20-ft sections. This facilitated rapid installation and reduced the overall project timeline. Each pipe segment was fitted with casing spacers—one in the middle and two positioned 2 ft from each end. This ensured proper alignment and support during insertion.
Using a 120,000-lb excavator, AUI Inc., positioned each pipe segment at the entrance pit and segmentally pushed it into the steel casing. This methodical process involved stopping the insertion just before the segment was fully in place. This allowed for the subsequent pipe section to be aligned and securely banded. This sequence was repeated until the entire pipeline was successfully installed over a span of two days.
Following the sliplining procedure, the annular space between the steel casing and the spiral rib liner pipe was filled with lightweight cellular grout. This grouting operation ensured a secure and stable fit, preventing potential issues such as pipe deformation or water ingress.
Cultural and Environmental Considerations
Throughout the project, the team remained acutely aware of the cultural significance of the Isleta Pueblo lands. Coordination with tribal leaders was paramount. Construction activities were adjusted to accommodate cultural ceremonies and events, ensuring minimal disruption to the community’s traditions and daily life.
Environmental factors, particularly the proximity to the Rio Grande River and the associated high-water table, required meticulous planning. The dewatering process was managed carefully to prevent adverse effects on the surrounding ecosystem. All activities were conducted in compliance with environmental regulations. The project team also implemented sediment control measures to prevent runoff from contaminating nearby water sources. This further demonstrated a commitment to environmental stewardship.
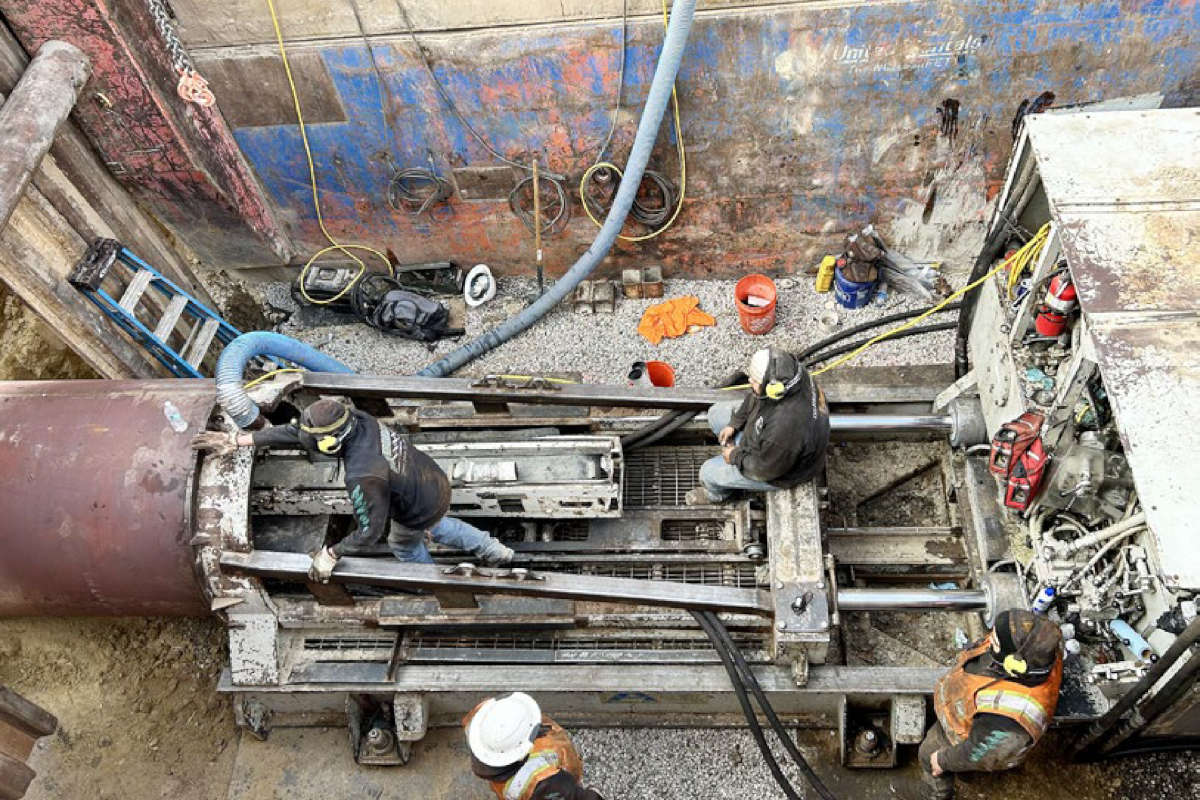
Outcome and Long-Term Benefits
The successful rehabilitation of the irrigation pipeline restored a critical water supply to the agricultural lands of the Isleta Pueblo. The solution not only addressed the immediate structural failure but also provided a durable solution with enhanced hydraulic performance.
The polymer-coated interior ensures long-term resistance to corrosion, reducing maintenance needs and extending the pipeline’s life.
This project serves as a testament to the effectiveness of combining advanced trenchless technologies with culturally sensitive and environmentally conscious practices. By selecting appropriate materials and methods, the MRGCD successfully navigated the complex challenges presented by the pipeline collapse. This ensured the continued prosperity of Isleta Pueblo’s agricultural endeavors.