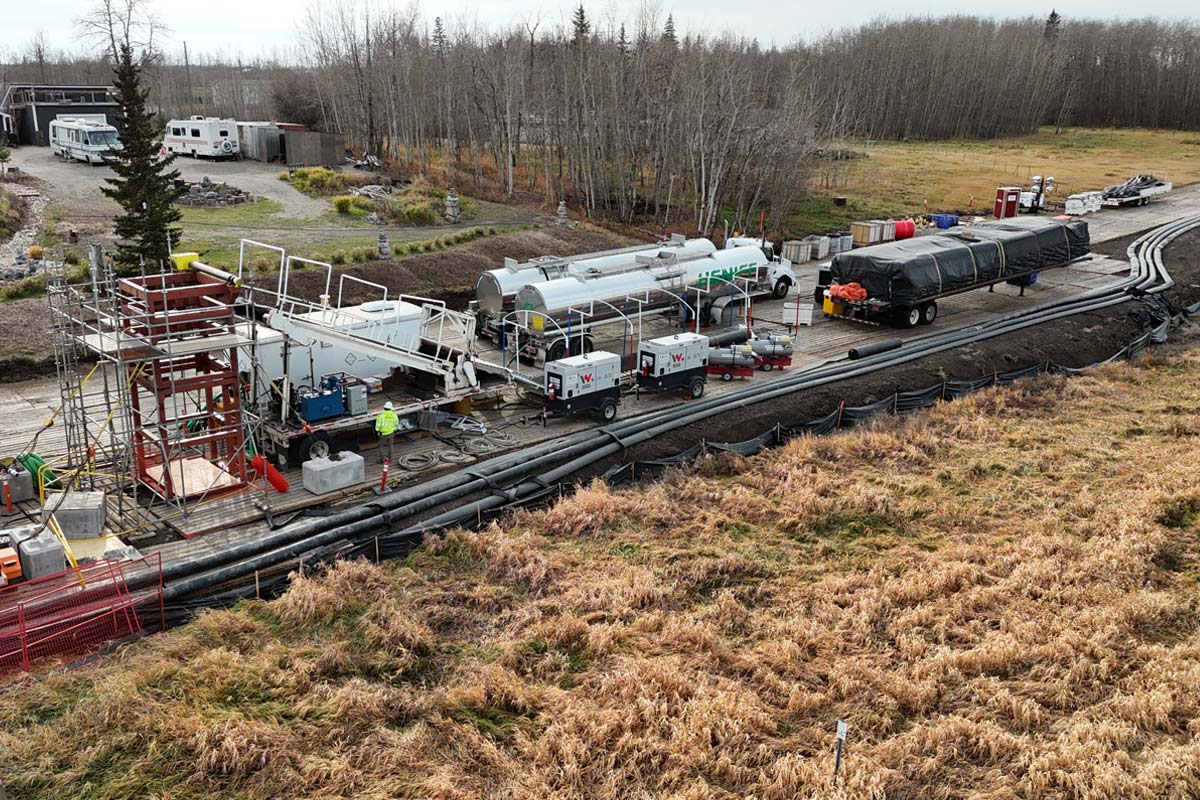
Insituform Technologies Ltd. Continues to Advance Rehab in Canada
One of the earliest installations of cured-in-place pipe (CIPP) relining in North America took place in Canada. The project took place in the late 1970s.
The work was done by a licensee of U.K.-based Insituform Group Inc. As were all those early relining jobs in North America. The first several projects in Canada were completed by U.S.-based licensees of the technology.
A lot has changed in the industry since then. But, one thing is certain, Insituform is still regarded as the king of the CIPP market. In Canada, work is completed under the auspices of Insituform Technologies Ltd., an Azuria Water Solutions company.
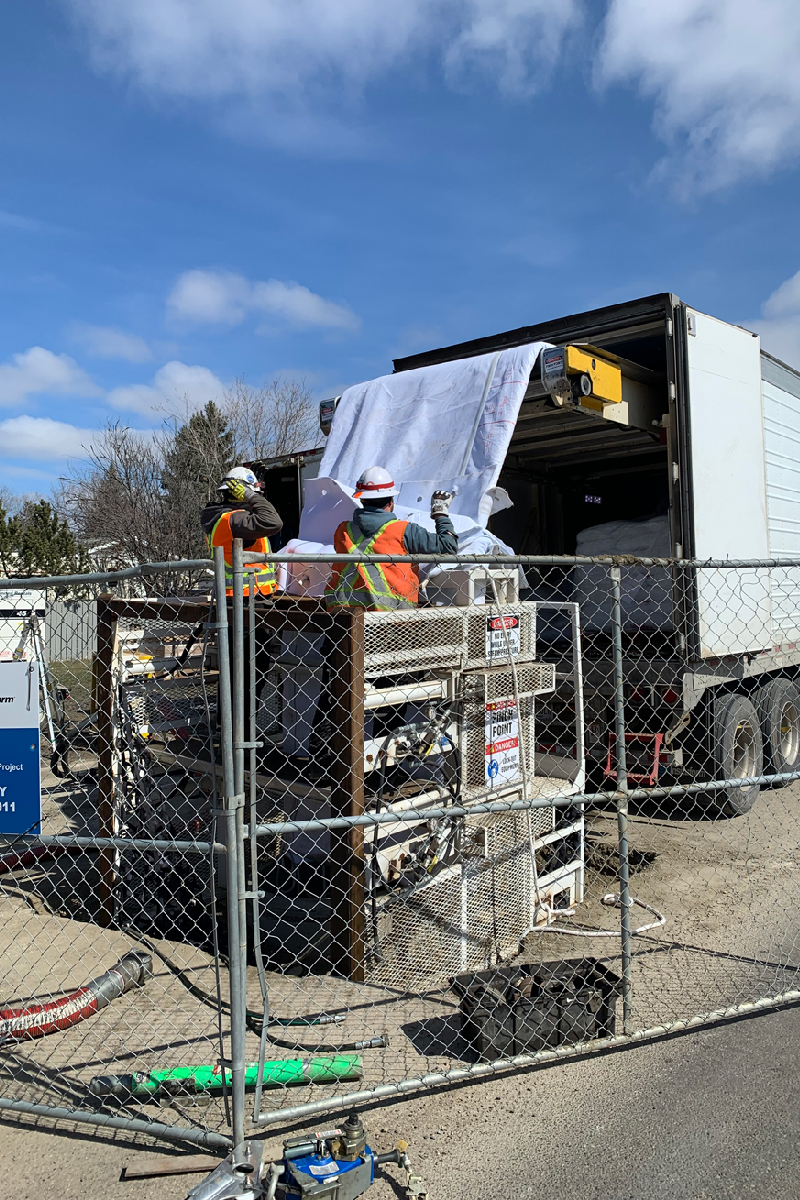
Building a Team in Canada
“Insituform Technologies Limited started life as Insituform of Canada – by the British patent-holder of the Insituform technology – in the mid-1980s in Ontario,” says Ken Foster. “There were three licensees of the technology, one in Quebec, one in Ontario that looked after Ontario and Manitoba and one in British Columbia.”
Though he retired in 2020, Foster’s name is synonymous with the growth of CIPP and the Insituform name in Canada. He joined the team in 1988 and grew to oversee all of Canada as president of Insituform Technologies Ltd.
Foster, a civil engineer, owned a consulting firm in Edmonton when he first learned of the CIPP process. As with many early adopters, he was intrigued by this less-disruptive construction technology.
“I found that Insituform was looking for a licensee in Western Canada. My next door neighbor owned Babachuck Engineering and Construction, so we put that together,” says Ken. “I started work in February 1988 with Insituform.”
In 1989, Ken and his team formed a joint venture with Insituform Group. Thus creating Insituform of Canada based in Edmonton. The Quebec licensee was bought out and a few years later the Ontario licensee followed suit. The last remaining licensee in British Columbia was bought out in 1998.
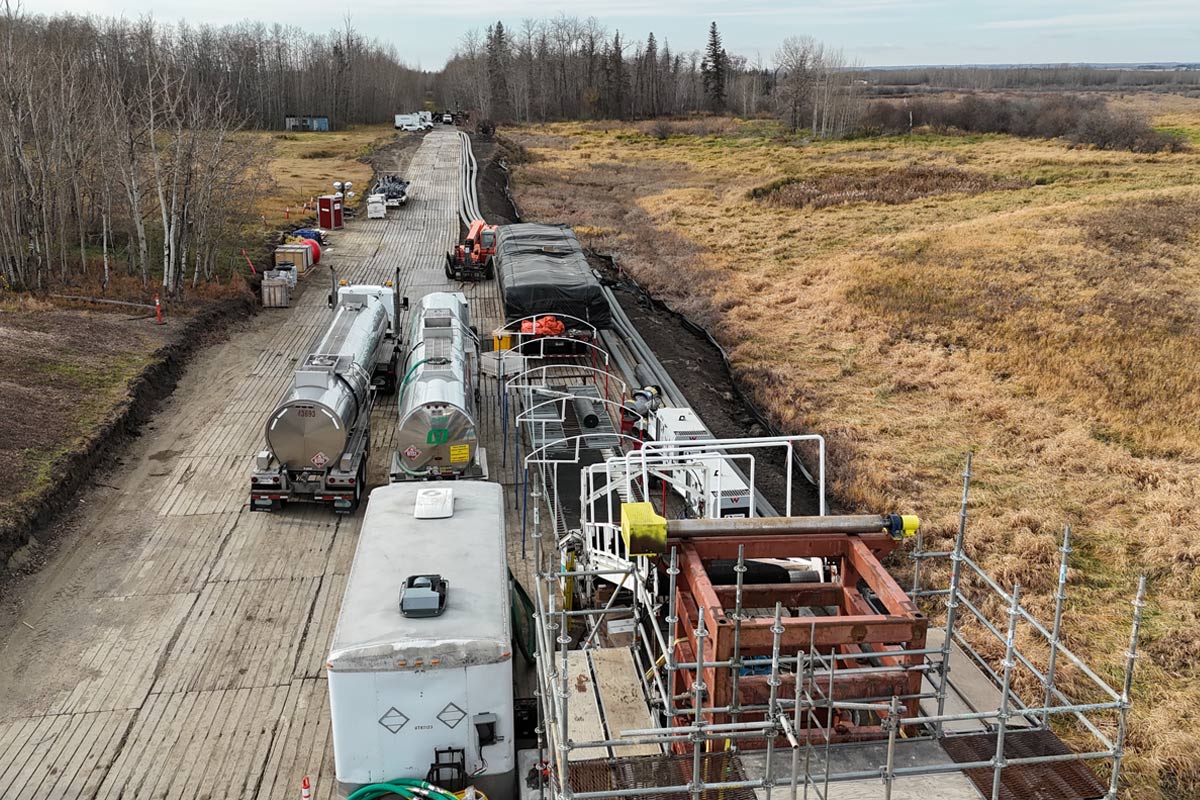
As the patents ran out in 1992, Insituform North America bought out Insituform Group in the United Kingdom. This brought Insituform of Canada into the larger fold where it sits today.
Insituform Technologies Ltd. Today
With a head office and wet out facility in Edmonton, the company has five locations across Canada. The remaining offices are in Calgary, Winnipeg, Hamilton and Montreal. A second wet out facility is in Chamblee, Quebec.
Its total Canadian workforce numbers 174 in Western Canada and 110 in the east. It has seven CIPP crews in the west and six in the east. Crews handle CIPP and manhole rehab work and other aspects of projects are sourced through vetted contracting partners.
“When we started we had two crews in Canada and [we were] using the old system of hot water and scaffoldings, which was pretty simplistic and quite slow,” says Ken. “The productivity rate was nowhere close to what it is today. That was the basic system that started in the U.K. and done the same way for the better part of eight to 10 years without any significant major improvements.”
Foster adds that with the advent of air inversion and steam curing and improvement in resins; the changes have been dramatic.
“A lot of growth [in the industry] happened with the change to air inversion and steam curing That’s when the production really ramped up,” says Andrew Foster, vice president and Canada West area manager for Insituform. Andrew joined his father at the company in 1996. “I think when you [Ken] started it was almost a shot a week.”
“If we had a really good week, we’d get two shots in, but most weeks it was only one and then we only worked basically six or seven months a year,” says Ken. “We didn’t know how to fight the winter conditions in Canada. It took us a few years to understand how to operate year-round.”
It wasn’t uncommon for one Edmonton crew to go to the United States to work while waiting for the weather to thaw in Edmonton. Early on Ken notes, most of their work was in the west, with Eastern Canada lagging.
Improved Technologies = Growth
Andrew, like his father, saw a lot of the growth spurred on by the improvement in equipment and awareness of CIPP. In 2000, before going to air inversion, he estimates the crews were performing a shot a day. “When air inversion came in we saw that rapid growth,” he says.
Looking at the early data in 1987/88 Insituform completed 6.3 km of CIPP. Since 1995, the company has grown over 1,400 per cent in terms of installations.
“A lot of that came air inversion and steam curing. We went from doing that [single] shot a day in the late 90s early 2000s, to having the capability in smaller diameters of doing three shots a day, basically 1 km a week,” says Andrew. “That was a huge jump for us and with that [came] increased productivity and the costs come down. The communities saw that.”
This has made CIPP more attainable for communities. It changed it from the tough sell of new technology in the early days, to now basically the default choice. The Fosters note that the bulk of this shift happened from 2005 to 2010 as the installers shifted to air inversion and steam cured CIPP.
“Now we rarely use water except in certain situations where it is necessary,” says Andrew.
Getting Noticed
With so many projects in the portfolio, Ken found it difficult to pinpoint one or two that put the company on the map.
McKnight Boulevard
One that stands out is a major rehabilitation project on McKnight Boulevard immediately south of Calgary International Airport.
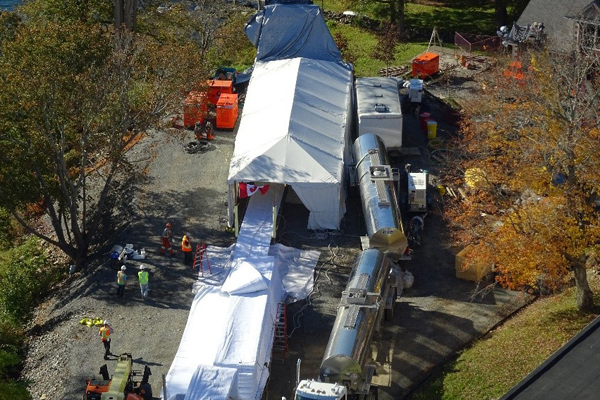
is the longest single CIPP install completed in Canada to date.
The work was done in 1993 and 1994 and involved the CIPP lining of 630 m of a 900-mm concrete pipe.
Ken recalls that the pipe was severely corroded partially due to the deicing fluid used by airport. The pipe was approximately 8 to 9 m deep and ran down the middle of McKnight Boulevard. A typical install would not be possible.
“We had never done what is termed an over-the-hole job where all the resin mixing is done onsite. We decided we’d do that, and it was the first over-the-hole job in Canada. It was a tough job. We did it quite successfully,” he says. “We had some issues with the resin, where it came too hot and we had to cool it down, but that was just one of those little things you must deal with from time-to-time. And we completed the job basically on time and on budget and really impressed the City of Calgary. From that time on, we’ve worked with the city every year.”
Work in Saskatoon
Another project in Saskatoon sticks out because of its location and the pieces Insituform had to incorporate to make it a success. It was also one of the earlier projects that the company performed after starting to work year-round.
It was 305 m of relining work. However, that 305 m was the last section before the pipe entered the city’s sewerage treatment plant. This required bypassing sewerage from the entire city.
“We had to bypass the whole city for that project, and we did that in February and the temperature dropped to -35 degrees and had to deal with the Western Canada winter weather conditions,” says Ken. “That was an impressive project which gained a lot of attention. These are two [projects] that demonstrated the success of our system and our capability to tackle those kinds of jobs. That helped us quite a bit.”
Since forming the company in Edmonton, in 1987 what has really helped the company grow is the legwork by its employees to educate system owners on the benefits of CIPP.
“It started in 1987, and there was slow growth over 15 years where municipalities tried it out again, and again, and slowly built up their programs,” says Andrew.
He notes that during this slow build up phase the system owners saw that CIPP is quicker, less disruptive, the product lasts and it’s less expensive overall than digging. Especially in the prairies where pipes are buried up to 6 to 8 m deep.
“To dig, the price really grew astronomically [especially] when you get to the early-mid 2000s,” he says. “The longevity proved that this technology worked, and it is the best size-for-size replacement for sewers.”
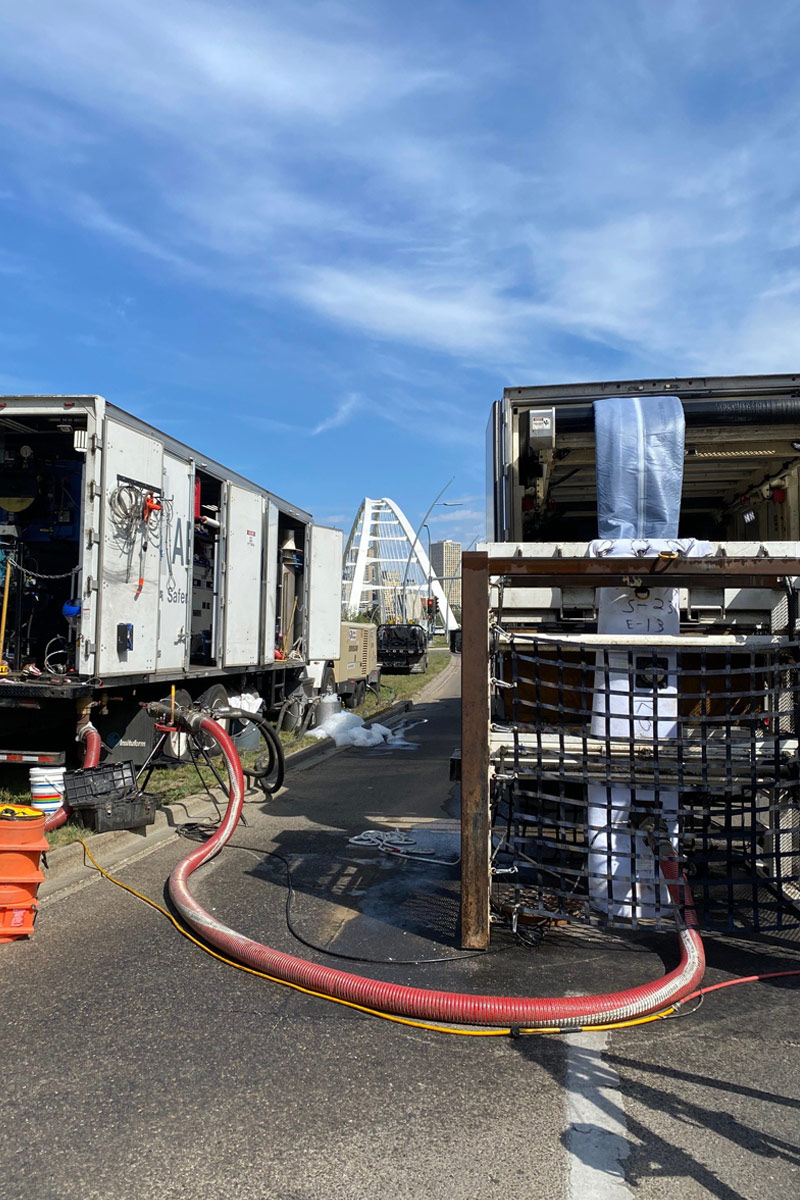
Educating the Public
Growing the company required a lot of footwork on the part of Ken and his team. And it’s a cornerstone of Insituform Technologies Ltd. and Azuria’s overall success today.
Ken is considered one of the forefathers of the North American Society for Trenchless Technology (NASTT) and a member of its Hall of Fame. Other members of the company work diligently with NASTT, AWWA, ASCE and more to help promote and grow the industry.
One of those team members is George Bontus, P.Eng., director of engineering, chair of NASTT’s Northwest Chapter and a key member of several AWAA standards committees.
“We do spend a lot of time meeting with clients – because there is turnover in those organizations,” he says. “[We’re] educating and trying to give them a good understanding of what is involved and the overall product and process.”
The concept of CIPP is well known which means that Insituform is no longer in the selling stage, but rather the solutions phase. “Now it’s trying to come up with the best solution for them [system owners] using different [trenchless] methods,” says Ken.
As the knowledge base of owners and consultants has grown, Insituform has reaped the benefits.
“We’re vertically integrated and we know the product from the bottom up,” says George. “That makes it a lot easier for us to educate and help with understanding how it works. We get a lot of requests for information that are repetitive because of the influx [of new people] into the market.”
There is plenty of room for growth in Canada. The trio alludes to ultraviolet (UV)- cured CIPP and pressure pipe (primarily watermains) as the two big areas for growth. They also see more system owners creating more all-encompassing projects that include manhole and lateral work, as well.
Growing UV Work
“Whereas in the past, the contracts were strictly CIPP, now there is a lot more that come up which combine manholes and other aspects [like lateral rehab] to it. They’d rather have one contract than two or three different contracts working in the same vicinity. It’s easier for them to administrator,” says Ken. “In addition to sewer work, we do water rehab as well. That started out in the east where, particularly Montreal and Toronto, were getting into some fairly large contracts.”
According to Andrew, pressure pipe rehab market is here and it’s catching up the gravity lining side. He jokes that George was talking about the coming boom in pressure pipe rehab when he joined the company 20 years ago.
“At the outset there wasn’t a good template or guideline that you could use to qualify your liner as an AWWA Class IV or Class III,” says George. “We’ve seen in the last five years for sure that there has been a great effort in standardization of the designs and products that are used for watermains. It’s going to really focus the market.”
As for the UV work, it’s something the company looks at on a case-by-case basis. With the group acknowledging that for a straight-forward lining project air inverted and steam-cured CIPP is still the most cost-effective option.
“We’ve done UV work in Ontario for about the last six years…it’s growing, but it’s somewhat of a niche market,” says Ken. “There is a need for it and there is a place for it, and we recognize that… and we see more of it coming along.”
Port Moody
Bontus highlights the niche nature of UV CIPP and the growth of pressure pipe rehab for the company in one project – the Port Moody Shoreline Trail Force Main Rehabilitation in 2022. The project is the first UV cured forcemain rehab project in Canada and was the 2023 Trenchless Technology Project of the Year Rehab Honorable Mention.
“In Port Moody, we looked at air-steam and UV and it came down to the logistics of getting the inversion equipment in made UV a much more palatable alternative,” he says.
What Lies Ahead?
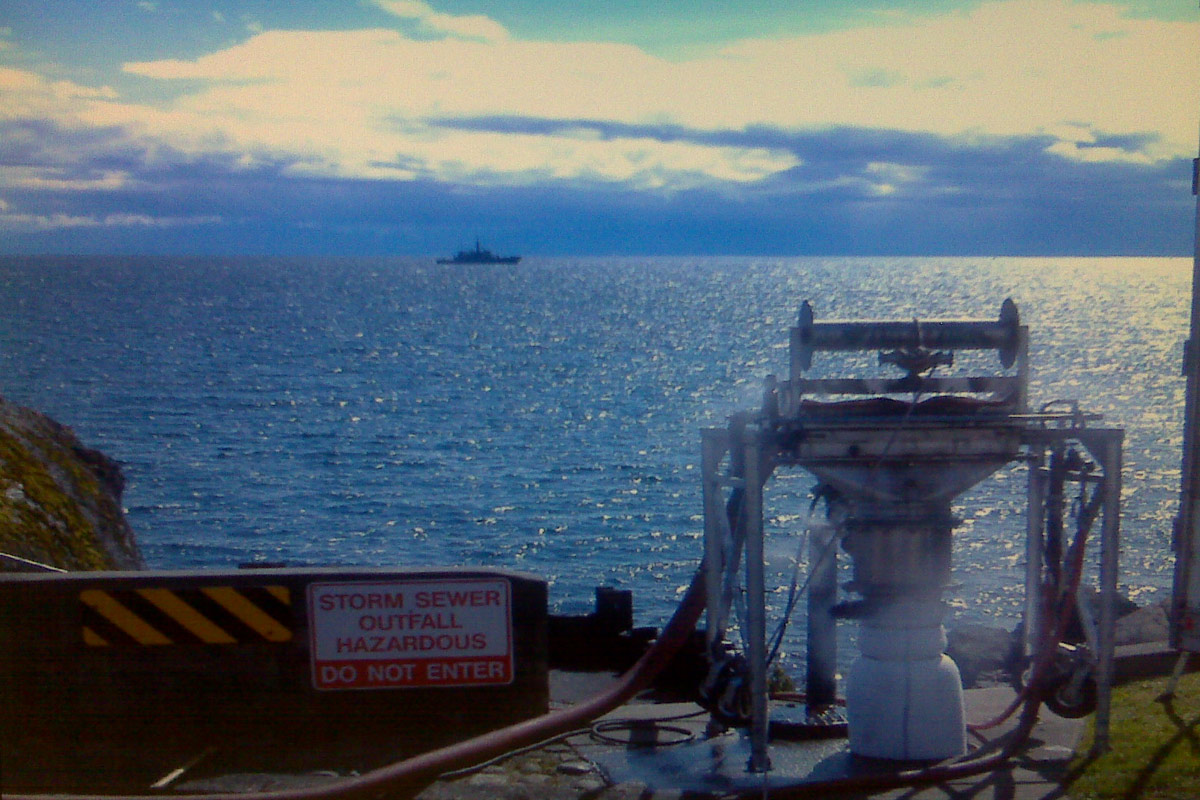
As Insituform Technologies Ltd. looks to the future, its legacy is firmly rooted in decades of innovation, resilience and leadership in trenchless technology. The company prides itself in becoming a trusted partner for municipalities across the country and helping to shape the industry in Canada.
Insituform’s commitment to education, collaboration and technical excellence continues to set it apart. By staying engaged with industry organizations, the company ensures it remains at the forefront of evolving technologies and best practices. Whether it’s through expanding UV-cured applications, advancing pressure pipe rehabilitation, or integrating comprehensive project scopes, Insituform is focused on delivering solutions that meet the complex needs of modern infrastructure.
The next chapter promises to be as impactful as the last, driven by the same spirit of innovation and dedication that has defined the company since its inception.
Mike Kezdi is managing editor of Trenchless Technology Canada.
Latest Posts
- Epoxytec Announces Winner of Manhole Photo Contest
- Watts Announces 2025 Backflow Hero Award Recipients
- 4CE Engineering Group Launches with Financial Backing by Quad-C
- NASSCO Report – CIPP Lining of Elliptical HDPE in Omaha
- 35 Years of Innovation, Partnership, and Progress: Celebrating Sprayroq’s Legacy in Trenchless Technology Sprayroq Celebrates 35 Years