Huge CIPP Project in California
March 1, 2009
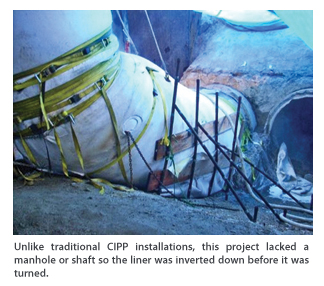
This two-year, $60 million wastewater project was fraught with many obstacles. Even before the project began, project superintendent Jack Bowling said that “Due to the high risks involved, it took awhile to get approvals to go forward,” yet the 88-year-old existing three concrete siphon barrels were deteriorated and unable to handle today’s usage.
Among the high risks that needed to be addressed was the location, as the pipeline lies under the 405 Freeway at the Fox Hill Mall and proceeds through to Culver City at Rodeo Road and Jefferson Avenue. Another problem was the size — the Centinela Siphon at the The Lower North Outfall Sewer (LNOS) is 18,200 ft long, consisting of three 78-in. diameter concrete siphon barrels, which are 1,772 ft long, all in need of rehabilitation.
It was decided that the best method of rehabilitation for this project would be CIPP, a process that is designed to cause the least amount of disruption to the surrounding areas. The contract provided 14 different material options for the CIPP system and the contractors, Colich and Sons, with J.R. Pipeline joining together in this venture. Spiniello Co. was hired to take charge of the CIPP portion of the project.
“When we arrived at the site, instead of an open-cut, there was an inversion hole that was really a pit that the general contractor had excavated for the demolition of a large junction box that transitioned the flow from the LNOS to the triple 78-in. siphons,” Spiniello construction manager Sam Silva said.
It then became necessary to coordinate with Colich’s Brad Sims, P.E., who then designed a platform of iron capable of supporting half of the wet-out trailer and an installation tower, which had to be built in order to gain access into the 42-ft fall line area where the work would take place.
Unlike traditional CIPP installations, this project lacked a manhole or shaft; therefore, the liner was inverted down before it was turned. “This created another unique situation,” reported Silva.
It became a “concert hall show” to witness an inversion down below the platform. Frank Levy, with the City of Los Angeles, invited most of his new engineers to see the liner get inverted and then turn into a tricky operation. Once the liner was turned and inverted into the 78-in. siphon, Bowling devised a means of holding the liner in place by adding water into it, causing enough pressure to make it move. By the third inversion, Bowling and his crew had met all of these challenges.
The CIPP lining casts a corrosion-resistant, epoxy vinyl ester resin into an existing pipe using a felt host. In this case, the felt was required to have a minimum of l.295-in. thickness and a long-term tensile strength of l,200 psi and flexural modulus of 100,000 psi. The felt is inverted and cast within the pipe with the use of cold water to prevent a reaction. Here, a special chilling unit was needed to maintain a temperature of 42 F in order to prevent a reaction of the resin — Ashland Q6405 vinyl ester resin — to harden or cure before the inversion was completed.
The CIPP liner is made of a plastic cover sheet and seven layers of felt, which is made of polyester staple fiber. The liners are manufactured 450 ft in length and two pieces were spliced to make a 900-ft long liner bag before shipping to the project site. The liner bags were then spliced again at the jobsite to make a l,800-ft long liner for one siphon barrel. The total weight of one completed liner bag was approximately 57,600 lbs. Vacuum pumps were used to remove air from the liner. The resin for the liner was delivered and tested for an optimum gel time of 13 to 16 minutes at 180 F, which causes the resin to harden and become the new pipe.
While this process is taking place, l,800 ft of liner bag is still sitting on the roller bed. Approximately 255,000 lbs of resin was used to complete one siphon barrel lining. The liner bag is then tied-off, sewn with ropes and ready to be inverted, as mentioned above. The inversion of the bag is a non-stop process and must not be delayed due to the time and temperature sensitive process; therefore this goes on right around the clock and there is no delaying of this process.
Two large boilers mounted on trucks were used to heat the approximately 440,000 gals of water in the installed liner bag by pumping hot water through the three installed large vinyl hoses. The cooking segment of this method continues until the temperature in the liner bag reached 180 F. It takes about eight hours of curing before it becomes a hard, solid material, after which the cooling process begins and temperatures drop to 100 F. A hole is then made at the downstream side of the liner, allowing the excess water to drain. The result of this entire process provides a gas-resistant, thick, solid hard liner that will service the community for many years to come.
This project was so unique in many ways. Many times large pieces of equipment had to be moved in and out to gain access in the shopping mall where the project took place.
Alice Steinbacher is a freelance writer based in Bernardsville, N.J.