HDD on Dubai’s Logo Island
March 1, 2009
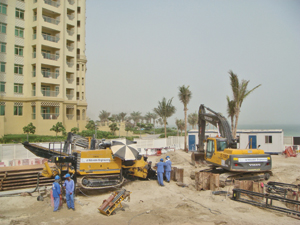
At one of the three complexes, the Palm Jumeirah, developer Nakheel has included two smaller islands shaped like date palm leaves – the development’s logo. Jutting out from the main island’s trunk, the Logo Islands give the Palm Jumeirah an iconic look from the skies above or one of Dubai’s many skyscrapers.
Nakheel began the land reclamation project for the Logo Islands in June 2003 and finished in February 2005. In total, 155 million cubic ft of sand and 1.1 million tons of rock were used to create the two islands, which together cover 1.5 million sq ft. Both islands are intended as highly exclusive residential area. The one on the Abu Dhabi side of the development has been sold to a property developer, while the one on the Dubai side will become home to one of the emirate’s rulers.
For this second island, Nakheel had to supply services like drinking and irrigation water, telecommunication and sewerage from the Palm. That meant creating three 1,804-ft crossings to the island and, for this, the company decided to use horizontal directional drilling (HDD). This method had already been used to bring services to the main Palm Island. HDD proved to be faster and cheaper than microtunneling, while having less impact on the island, its residents and local wildlife than dredging.
Challenging Conditions
The HDD contract was awarded to Al Naboodah Specialist Services LLC, a part of the local Al Naboodah group of companies. Having carried out the HDD project from the Palm, Al Naboodah was already well acquainted with the ground conditions at the site. The first 26 ft of sand sits on a 5-ft layer of cap rock. Beneath that, at a depth of 31 to 89 ft, they would be drilling through sandstone for the first half of the horizontal section and gypsum and clay for the second.
As both the Palm and Logo Island are man-made, the top layer of backfilled material was a major concern for the contractor. Its soft nature meant bentonite drilling fluid blowouts at either end were a distinct possibility. This could have potentially caused problems in achieving an appropriate exit angle when drilling on the Logo Island. Moreover, much of the drilling would be under the sea, so keeping bentonite returns going was not going to be easy either.
Starting out right
The service installation included 10-, 14- and 20-in. HDPE pipes with sub-ducts ranging from 1.5 to 8 in. Al Naboodah designed the drilling project with 17-degree entry and exit angles and 1,310 ft radius entry and exit curves. This design meant the deepest point of each bore would be 89 ft below the surface.
For the drilling, Al Naboodah decided to use its Vermeer NAVIGATOR D300x500 HDD drill rig together with three Vermeer R300 reclaimer systems and a Vermeer SA300 remote high-pressure bentonite pump. This combination had successfully pulled 32,800 ft of 20-in. HDPE piping during the HDD project for the Palm.
The first task was to sink a 6-in. steel pipe on the seabed and determine its exact position using a Reduct DuctRunner. This pipe would house the wire for the Paratrack loop used to guide the drilling of the pilot bores, with return wire laid on the seabed with 246-ft clearance from the pipe. During the backreaming phase, the pipe would also be used to transfer the bentonite drilling fluid from exit to entry side.
Drilling Starts
Drilling began with the bore for the 14-in. pipe. For this, Al Naboodah used a 7-in. mud motor with a 10-in. tri-conal milled-tooth bit. Behind this, two 30-ft non-magnetic drill collars carried the Paratrack tool and pressure sub. The drilling took five days. Then the bore was backreamed using a 20-in. milled-tooth hole opener, which took an additional four days. Finally, the pipe was pulled with an 18-in. barrel reamer in front of the swivel.
Next on the plan was the 10-in. pipe. However the D300x500 was needed for an urgent job elsewhere. So to stay on schedule, Al Naboodah called in its NAVIGATOR D100x120 for this smaller bore.
Again, a mud motor was used for the pilot bore, this time a 4-in. motor with a 5-in.tri-conal milled-tooth bit. Two 20-ft non-magnetic drill collars created a similar bottom hole assembly as for the bigger rig. After five days of drilling, backreaming was carried out using a 12-in. milled-tooth hole opener and took three days. The pipe was pulled the next day.
A Sticky Problem
A couple of days later, the Vermeer D300x500, R300s reclaimers and SA300 high pressure pump returned to the site so work could begin on the bore for the 20-in. pipe. Initially, a mud motor was used again. However, although mud motors had performed well on the previous bores, this time the drilling ran into difficulties when it reached the gypsum and clay in the second half of the horizontal section.

When the first bore was backreamed, the hole opener had some difficulties getting through the gypsum and clay segment. So with the stickier condition in the segment for this final bore, Al Naboodah employed a new backreaming strategy.
First, a 30-in. milled-tooth hole opener was pulled to the end of the exit curve and then pulled back out on the exit side. Next it was removed from the drill string and replaced with a 26-in. flycutter. This was pulled quickly through the 30-in. hole to start cutting the clay at the beginning of the horizontal section. Once the flycutter was through the clay, it was pulled slowly through the sandstone portion of the bore to reduce tooth wear and allowed to complete the backreaming without having to stop and replace the teeth.
This new strategy paid off and backreaming was completed within four days. A 24-in. barrel reamer was pulled through the bore to check it and no problems were found. The 20-in. sleeve was pulled the following day.
Finally, the sub-ducts were installed. These comprised a bundle of utility pipes for the 20-in. bore, and a 4-in. drinking water line in the 14-in. pipe. To do this, the D300x500 was used to push a drill rod through the sleeve, the bundle/pipe and swivel was attached, and the rod pulled back.
The project certainly had its challenges: from blowout risk and changing soil conditions to coordinating the HDD around all the ongoing backfilling and construction activities on Logo Island. But Al Naboodah executed according to plan. It was a vital step in the creation of the Palm Trilogy – which has since become an iconic symbol of Dubai’s rapidly growing tourist industry.
Hester Regoort is a technical writer for Two Rivers Marketing, Des Moines, Iowa.