HDD in Russia: “Treasure Island”
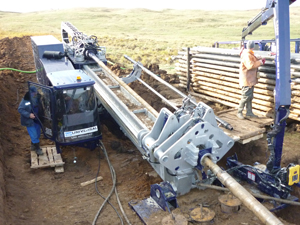
In 1976, Niznekamskoe reservoir was formed with several scenic islands in Menzelinsk region (Public of Tatarstan, Russia) as a result of artificial elevation of water level in river Kama. Oil extraction is conducted on one of the islands with curios coast line. Considering that transportation of oil was rather primitive: extracted raw materials were pumped into oil truck, which was transported on water by a barge and further driven to oil collection station.
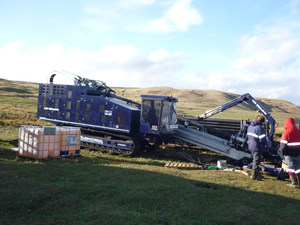
Because of the long winter weather cycle, the project could only be worked during the period of early May until the first freeze-over. Finally, it was decided that the only solution would be to use HDD technology to install this urgently-needed pipeline. On top of all that, project terms were strict: After the New Year holiday, oil “must be flowing through the pipeline” and it was already end of September.
By this time EcoTEK had purchased a new machine by Universal HDD, UNI-220×240, with 220,000 lbs of thrust and pullback force, 24,000 ft-lb of rotation torque and UNIMUD 325 off board mud delivery system with 325 gal/min, all supplied by the UNIRUS Group.
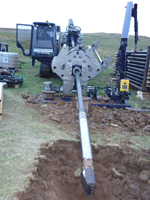
However, the customer had its own arguments, which soon outweighed ours … I think contractors will understand us. Immediately, job site surveys began on the shore of the Kama rive.
Preparations for the project were practically simultaneous with final decision on design and construction of the pipeline. There was little time with significant pressure from the client, and it was not hard to guess that with time the pressure would only increase.
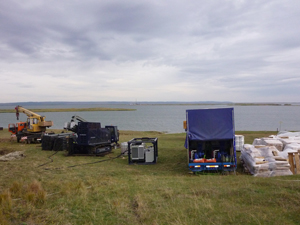
Engineering and project analysis was conducted by Geomaster to further understand geological conditions of bore path using geo-radar. In the end, we had the following parameters and calculations for the jobsite: the average depth of the bore hole was 45 ft (32 ft under the bottom of the river) in fatty, low water clay. These parameters were quite acceptable in view of aforementioned high risks with regards to rig’s capacity of only 220,000 lbs.

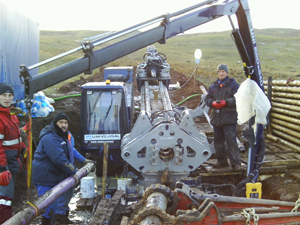
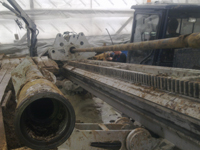
Despite the significant loss of time and shaken mood of the team, there were several options on how to proceed:
- Continue drilling in gravelly soil (this option was not considered for obvious reasons)
- Go under the layer of gravely soil, but in this case there were fears of failing in the last stages of pilot hole boring.
- Pass in small corridor between bottom of the river and top portion of the layer of gravely soil without allowing the pipeline to float up.
The decision was made to go with the last option, despite the fact it involved high precision and did not rule out possibility of gravel on the individual sections of the path. Drilling fluids had to be adjusted according to new conditions of the crossing. The new formula specified doubling of DUO-VIS additive in the final section of the bore. Additionally, the depth of the pilot hole allowed for using a wireless transmitter with Eclipse.
It seemed that nothing was preventing the start of the second attempt. However, winter came, and the first ice appeared. The thin ice was preventing the use of walkover locating system. It was unclear how long we had to wait and when it was safe for a person to move across the ice. The answer came unexpectedly – fishermen. Ice fishermen were also eager to start fishing on first ice, and that would signal to resume the job.
On a December morning, the work resumed. After eight days of continuous work with two 12-hour shifts, the drill head exited the ground at the exact spot on the island. The pipeline with 6.25-in. in diameter and 5,250 ft in length was already waiting on the island.The first ice on the river Kama was abundantly covered with snow and the ice was gaining strength slowly. By the time the pilot bore was ready for the initial reaming, there was no way to transport drill rods from the rig to the exit point on the island. Reverse reaming process was used to complete the remaining parts of the job. The reaming was completed by pushing the reamer and chain on drill rods away from the rig. Complete expansion of the bore to 11.85 in. was completed successfully right before the New Year.
Pullback of the pipeline went without a hitch. On average, pullback of one 20-ft rod took about three minutes (specifically one minute for a pullback and two minutes for break-out and unloading of a rod). In 28 hours, the job was completed.
Anyone who has worked on complex oil and gas pipelines knows that final completion of the project is dependent upon the customer’s approval and acceptance tests. The pipeline underwent three different tests. The first test was designed to find any deformation in the pipeline by pulling a metal sphere through and through. Second assessment was done under pressure – 80 atm. The final and third test was completed under 80 atm after connecting to the small section of pipeline on the island (the island section of pipeline was completed EcoTEK earlier that year using a Universal HDD UNI 60×70). All tests were completed successfully. A week later oil was flowing from the island though pipeline to collection station across the river Kama.
This article was submitted by Universal HDD.