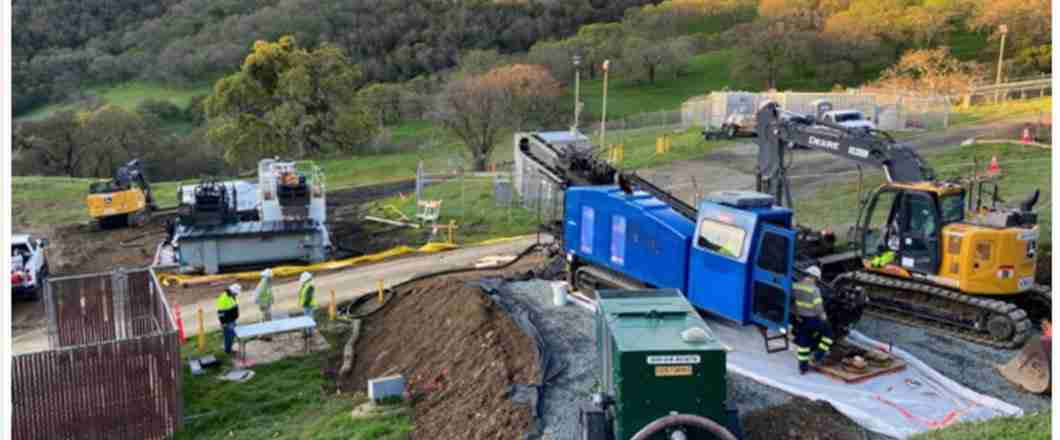
Gyroscopic Navigation and Smaller HDD Rigs
The Horizontal Directional Drilling (HDD) industry is in a constant state of evolution in all aspects with improved drilling processes and practices, improvements to existing technology and the development of new technology.
Along with these advances in the industry, HDD bores are being drilled in a wider variety of applications where there is a need for a high accuracy guidance system in highly congested urban areas, on deeper crossings and with more complex profiles. Smaller rights of way are becoming more common. Customer and regulatory requirements are also becoming stricter.
There are an increasing number of situations where conventional walkover systems or magnetic steering tools with secondary tracking are not viable or cost-effective options. A wide variety of conditions exist such as proximity to existing underground infrastructure, drilling under busy highways and large intersections, limited access on the surface for a secondary tracking coil, proximity to railway or tramways and in highly congested urban areas where rig access is limited.
Having the ability to accurately steer effectively and with a high degree of confidence in these situations allows smaller HDD contractors without the larger rig horsepower to drill more complex bores, as well as to satisfy any customer contractual requirements on navigation.
A small, extremely versatile, and highly accurate gyroscopic navigation system has been developed by Sharewell HDD to meet this growing demand. The Opti-Trac gyroscopic guidance system incorporates three state-of-the-art proprietary optical gyroscopes and three solid-state accelerometers. The gyroscopes were designed specifically for borehole survey and steering applications allowing for the small outside diameter size of the system in its pressure housing without compromising the accuracy.
RELATED: Ins and Outs of HDD Tooling Life
Integrated into the complete downhole system is an independent high accuracy magnetic steering probe. The magnetic steering probe is used primarily for ranging on bore-to-bore intercepts as well as providing secondary tracking when desired at the exit. Additionally, a second redundant inclination measurement is produced from the magnetic steering tool independent from the gyroscopic module.
The Opti-Trac can also be configured without the magnetic probe and is often used on small drilling rigs where the overall downhole assembly length is limited. The system is modular in design, additional devices such as annular pressure can be added, and all sensor modules communicate on a single communication bus.
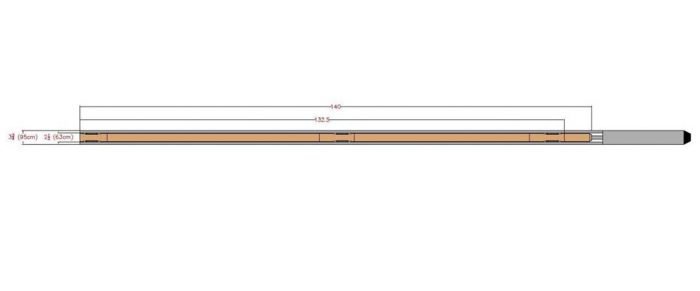
The gyroscopic module has two distinct operating modes. In the first mode, the gyroscopes are used in conjunction with the triaxial accelerometers to perform an earth-rate gyrocompass. In this mode, with the tool stationary, the three orthogonally aligned gyroscopes measure the rotation of the earth while the accelerometers determine the gravity vector. The sensor data is then used to calculate the inclination and the azimuth of the tool relative to true north completely free from any external interference.
RELATED: HDD Guidance Technology: Risk vs. Reward
Following the gyrocompass reading, the tool automatically switches into an inertial navigation steering mode similar to an airplane or missile guidance system. In this mode, as the tool moves, the sensors are used to continuously measure any relative change from the initial attitude as in real-time as the drilling process progresses. Internally the system is calculating position at 500 times per second with advanced Kalman filtering estimating and correcting for any errors.
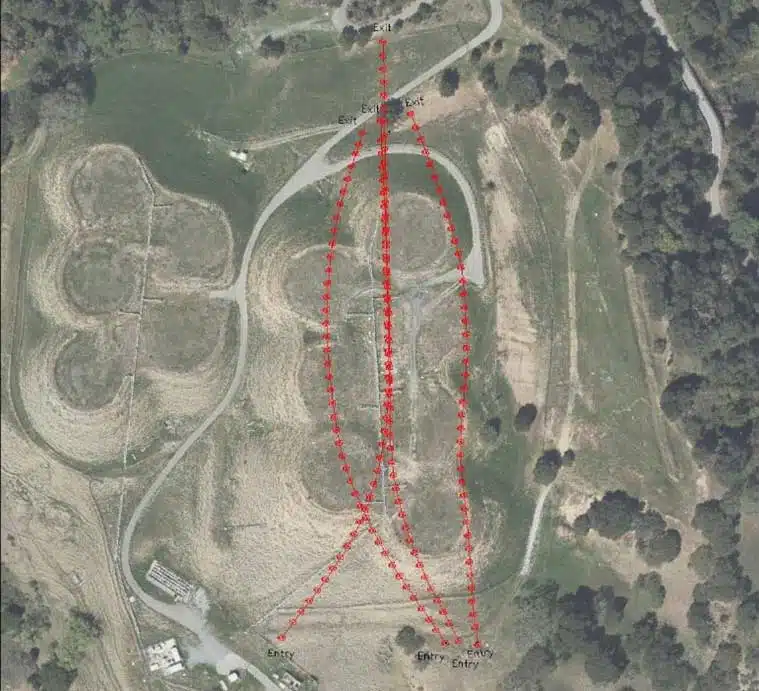
The Opti-Trac system does not require any special downhole tooling and is designed to be run in any customer-supplied standard non-mag drill collar 4.75 in. and above. A custom drill collar assembly is available with a 3.75 in. OD for use on smaller rigs.
The Opti-Trac system is regularly used to provide steering services on 100 rigs and is fairly easy to adapt to 60k rigs. With the custom 3.75-in. downhole assembly design and protocols it has been used with good success on rigs as small as a 15T Tracto Technik.
RELATED: HDD Job Requires Power in Small Footprint
The ability to employ a small rig is inherently more economical. In some cases where a gyro is required, it allows a smaller rig to drill the bore than would otherwise be required if a larger guidance system was used. There are significant savings in fuel costs for a small rig versus a big rig, savings in mobilization and demobilization costs and lower personnel costs with a smaller crew generally needed to operate with a smaller crew.
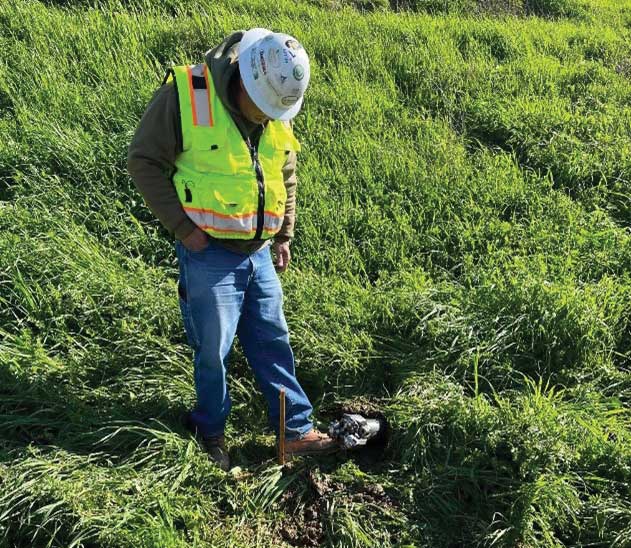
HDD Case Study
The Opti-Trac gyroscopic system was selected by Ellingson-DTD to provide guidance in the installation of four horizontal wells with lengths of 800 to 930 ft on an environmental remediation project. The four wells were drilled beneath existing, semi-buried fuel storage tanks. Three of the four wells were used for soil vapor extraction and the remaining one used for groundwater drainage. The tank locations were on a relatively steep hillside which presented significant challenges for the equipment staging. The existing infrastructure and topography limited the space available to construct suitable pads to support the rig for each well.
Crews used an American Augers DD-110 and a 6-in. hole drilled using 3.5-in. drill pipe. A 4.75-in. mud motor was used to address drilling conditions with the metasedimentary rock underlying the site. The Opti-Trac Gyro was run in a standard 4.75-in. non-mag drill collar behind the mud motor.
The semi-buried tanks under which the bores were drilled were constructed of a unique steel liner, embedded in concrete, and wrapped in steel cable. This construction prevented the use of a typical walkover or magnetic guidance system and necessitated the use of the gyroscopic guidance system. Because of the limited space available for rig placement, the well profiles were fairly complex considering the short distance. In order to correctly place the screen sections some of the wells needed to be drilled with large lateral turns and a relatively tight small radius of 475.
The four wells were successfully drilled using the Opti-Trac system with no secondary tracking.
Robert Lampert is gyro project manager with Sharewell HDD.