Grouted-in-Place Pipe Method Used to Reline German Sewer Lines
September 18, 2007
Nowadays sewer network owners and operators are faced with a huge number of different trenchless methods, materials and suppliers to seal and rehabilitate their pipes. This applies especially for cross-sectional pipe dimensions up to approximately 1,000 mm inside diameter (I.D.). Above that size, the number of approved systems and qualified installers reduces to a comparably small amount.
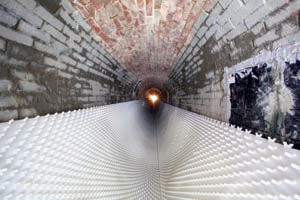
Since the early 1990s, Trolining GmbH, Troisdorf, Germany, has been an internationally recognized expert in the field of trenchless pipe rehabilitation. Its patented grouted-in-place pipe (GIPP) method has been successfully installed in about 20 countries around the globe. The continuously growing demand for reliable methods for the reinstatement of large sewers was a clear sign for Trolining to further increase the effectiveness of its system in that market segment. Pipe sizes between 800- and 2,000-mm I.D. today represent Trolining’s main field of application, regardless of whether the cross-sectional pipe profile to be rehabbed is circular or a special geometry.
In the second half of 2006, Trolining completed a project in the City of Bielefeld, Germany. Bielefeld is a medium-size town with about 330,000 inhabitants and an urban area of 258 sq km. The total length of public sewers herein is approximately 1,840 km. Regular inspections revealed leaking and a variety of other damages at one of the main collectors located along the Mühlen Str., near the city center. Most notably, the joints of the brick sewer, constructed around 1898, were found severely eroded. In some areas, the mortar between the bricks was missing down to a depth of 40 mm.
After assessment of the inspection reports, the municipality decided that 520 m of the sewer needed urgent repair. Whereas 310 m showed the standard egg-shape 1,200- x 1,800-mm I.D., further 210 m measured 1,400 x 2,100 mm. A few months later, Bielefeld’s environmental authority released a call for tender not only containing the trenchless rehabilitation of the mentioned sewer lines, but also a number of other preparatory and adjacent works. Installation of a bypass line, preliminary sealing of major groundwater infiltration, rehabilitation of the adjacent manhole chambers and re-connection of the lateral pipes were just some of the performances requested from the bidders.
The Trolining System
The Trolining trenchless pipe rehabilitation system is based on various high-density polyethylene (HDPE) liner components, which can be combined in a wide range of alternative configurations. The heart of the system is the Troliner with its V-shaped embedment studs. The annular void created by the studs is filled with Trolining Injektor, a specially engineered injection grout. This high-strength grout fixes the Troliner liner permanently in place and provides the load-bearing shell of the system.
Trolining liners are available for pipes ranging from 250-to 2,000-mm I.D. Segmental lining sheets are offered for rehabilitation of lines greater than 2,000-mm I.D. and for elbows and corners in man-size lines. The rehab system improves the host pipe’s flow characteristics and provides exceeding mechanical and chemical resistance.
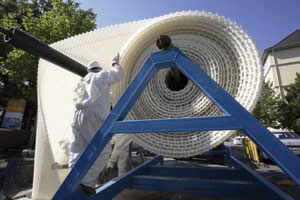
When the required inflation pressure is attained, the annular void is filled with Trolining injection grout fed from the downstream end. The grout’s extremely low viscosity ensures 100 percent grouting of the annular void, even for long distances. Additional grout characteristics are a defined material expansion and an exceeding short-term strength. The latter is decisive to keep the interruption time at an acceptable low level.
The GIPP Method
Despite of the GIPP method’s economic advantages, Trolining’s tender for the Bielefield project also succeeded due to the certified quality assurance and the high experience level in the field of large pipe rehabilitation, especially egg-shapes. The Trolining Double System with a wall thickness of 43 mm was quoted in that case — double meaning due to comprising two layers of studded HDPE liners. Additional reasons for choosing the GIPP method were the environmental friendliness and drinking water approval of HDPE, as well as the material’s compatibility with other lining components. State-of-the-art PE extrusion welding allows absolutely tight connections between the actual pipe liner and manhole rehabilitation sheets or the inverted HDPE saddles used for lateral connection.
An exceptional difference to other lining systems was the special system configuration Trolining was able to provide for dealing with Bielefeld’s specific project needs. While the common Trolining Double System involves an outer Preliner and a smooth HDPE liner that gets inserted prior to the studded ones, it was omitted in that case. Omitting the Preliner means that the outer annular void of the Double System was limited at the outside by the host pipe itself, while the first studded liner represented the inside boundary. In that way, it was possible to properly re-fill all defective joints between the brick work and embed the whole interior host pipe wall into a highly protective alkaline milieu by direct adhesion of the cementitious grout.
One year before, in August 2005, Trolining had successfully rehabbed a comparable host pipe, a pear-shape brick sewer, sized 1,800- x 2,250-mm I.D., by application of the same method. Drilling cores taken at this project proved the deep and reliable penetration of the Trolining grout into deteriorated brick wall joints.
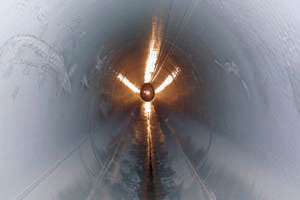
Project Implementation
Before the actual system installation could start, a number of essential preparations had to be done. A major item was the erection of a bypass line to divert the arising sewage around the construction area for the period of work. A steel pipe measuring 800 mm in diameter was laid over the ground to provide sufficient capacity for keeping the rehab sections dry. After dewatering the entire 520 m, technicians could access the host pipe and evaluate the further steps. Intensive cleaning and the provisional stopping of strong water infiltrations were required. At the same time, subcontractors enlarged those manholes that were designated for the HDPE liners’ insertion, to chambers of 2 x 2 m.
About three weeks after starting the preparations, the first liners were installed. The common manhole distances for the 1,200 x 1,800 mm were 60 m in average, which is a standard pipe length to rehab in municipal areas. More challenging were the manhole distances of the 1,400- x 2,100-mm host pipe; 103 and 107 m were the lengths that had to be lined in one step. While liner production for diameters of 1,200 mm was limited to 85 m in the past, the mentioned distances required additional efforts from both Trolining’s liner manufacturer and the installation crew. Trolining engineers and site experts tackled the situation and presented the solution after a number of technical meetings and process improvements.
Insertion of the 2.5-ton weighting liners occurred from the intermediate manhole, which separated the 210 m of egg-shape pipe into 103 and 107 m, both into the up-stream and downstream direction. Large triangle stands were placed next to the insertion pit to hang up the liner coils. For drawing the liners into the pipe, diversion rollers had to be placed right above the manhole chamber. After insertion of both studded liners, the resulting annulus was sealed by manual extrusion welding. Inflatable egg-shape packers were then used to plug the liner-package at both ends and water was fed in to build up a defined hydrostatic pressure. Special attention had to be given to the plug bracing — with a water column of 8 m (equal to 11.6 psi back pressure) and a cross-sectional area of 2.45 sq m. An equivalent horizontal force of approximate 20 tons had to be taken by the construction that held the plugs in place.
The 103- and the 107-m long pipe sections were rehabbed separately. Grouting of both occurred with the Trolining-specific mixing technology. Three standard mixing units were employed to prepare the injection grout. The Double System’s outer annular void space was filled first, needing approximately 1.5 hours for completion. The inner annulus could then be grouted within just one hour. After an additional 16 hours of curing, the high-strength grout attained the necessary short-term strength necessary for releasing the inside pressure from the lining system. Right afterward, the incoming house connections could be re-opened and connected.
Jens Kirste is with technical sales at Trolining GmbH, which is headquartered in Troisdorf, Germany.