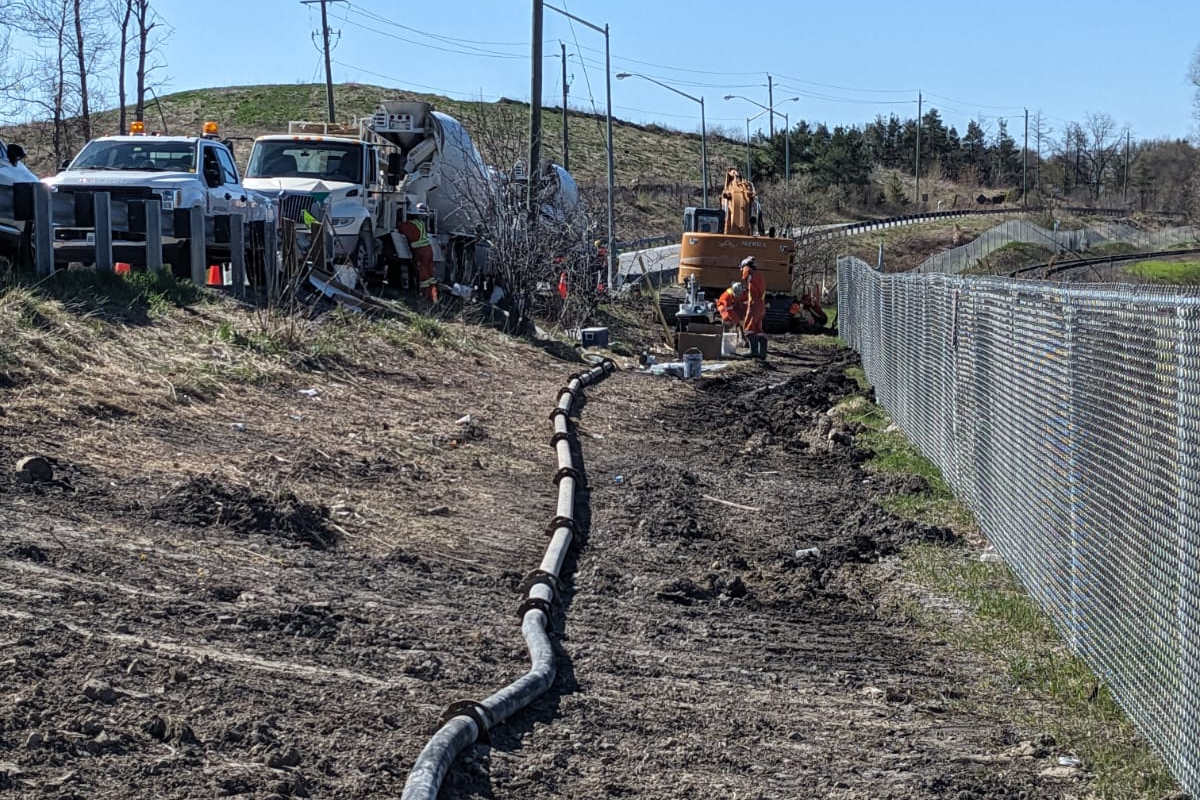
Fluidized Thermal Backfill Grouting for Managing Heat with Underground Transmission Lines
Railway and data center expansion throughout the Greater Toronto Area (GTA) and surrounding areas require underground power infrastructure. This infrastructure houses the high-voltage (HV) transmission lines needed to keep up with their high-volume electrical requirements.
Electrical transmission cables that run underground produce heat, which, if not properly managed, can reduce transmission efficiency and infrastructure longevity.
Thermal backfill grouting is used to fill the annular space between the transmission line conduits and casing. This helps conduct heat from the HV lines and disperse it into the surrounding ground.
Low thermal resistivity and high thermal conductivity are integral when backfilling duct banks. These factors ensure efficient heat transfer away from the conduits housing the electrical infrastructure.
When trenching is unavailable, horizontal directional drilling (HDD) is required to install underground HV electrical utilities. At this point, typical thermal backfill methods are not available due to the backfill material’s pumpability.
The annular space within casings for underground utilities is usually backfilled with pumpable cellular cement grout or neat grout. However, when HV lines are electrified, they generate significant heat. This makes these backfill methods insufficient when the lines are under load.
Cellular cement grout is flowable and pumpable for great distances. However, the air trapped in the closed cell foam acts as an insulator, trapping heat from the transmission lines.
Neat grout is also used to fill annular spaces. However, the thermal resistivity of neat general-use Portland cement does not adequately meet the thermal resistance of less than 1mK/W.
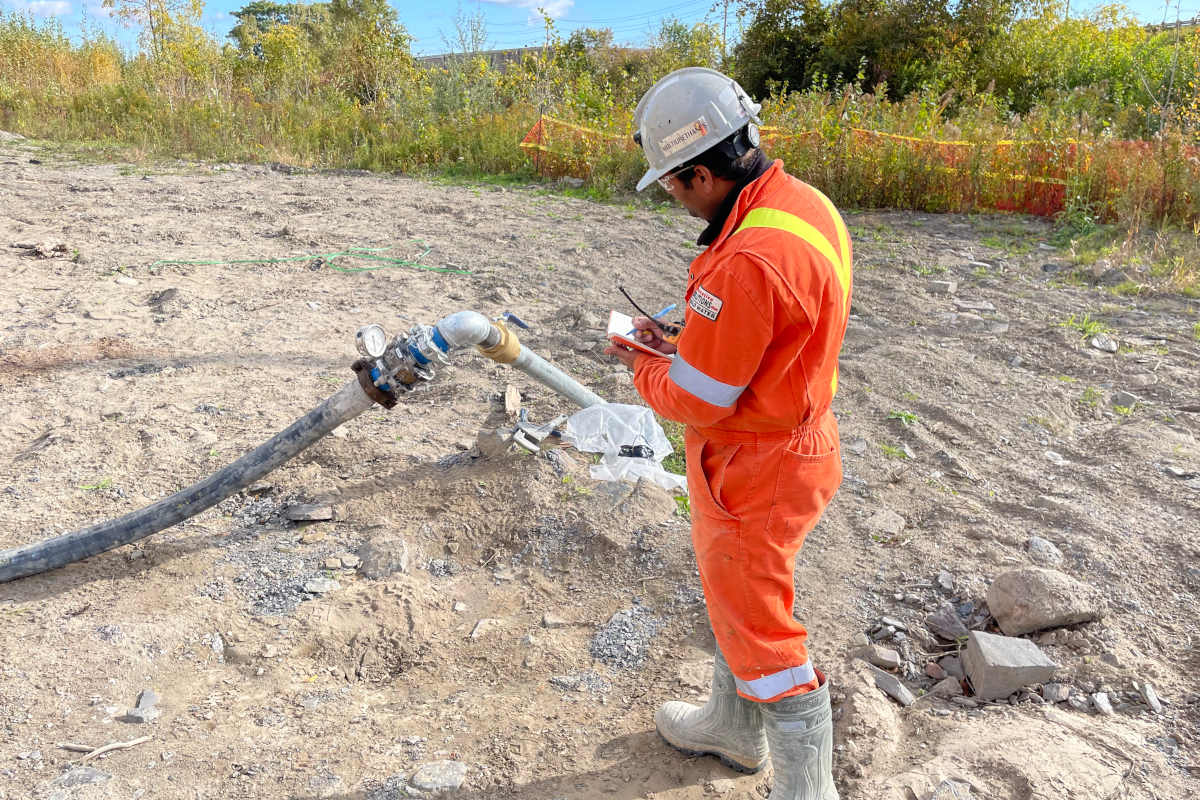
R&D of Pumpable Thermal Grouts
The Multiurethanes design team, led by Nav Stevens P.Eng., project manager, and Grant Davis, senior director of field services, was tasked with formulating a fluidized thermal backfill material. This material needed to be easily pumpable and achieve low thermal resistivity.
When designing the mix, the backfill material needed to meet three major requirements. These requirements were low thermal resistivity, adequate flowability, and utilizing locally available materials.
The thermal resistivity standards need to meet technical specifications. High flowability allows us to pump long distances with relatively low pressure. Locally available materials help with cost control and scheduling.
“Thermal backfill material usually has large aggregate but that inhibits its pumpability,” says Stevens. “We wanted to design a mix that was easily pumpable and still hit our mark on thermal resistivity.”
Careful selection of materials and rigorous lab testing led to our successful, custom thermal grout. Partnering with the right batch plant to create our custom ready-mix formula was a necessity. This partnership ensured a quality end product.
“Water content dictated everything… finding the right amount of water was what took time… you can mess with the ratios of sand and cement, but a touch of water too much and the segregation started,” says Stevens.
Within the first six months, 20 to 30 variations of grout mixes were created and tested. Hundreds of samples were cast and sent for testing. Team members were dedicated to casting, sampling, and in-house testing strictly to keep up with the demand for better results.
Resulting Thermal Grout Mix
Multiurethanes’ Thermal Grout is a cement-based, pumpable fill material designed and tested to achieve low thermal resistivity for electrical transmission infrastructure. Thermal grouts are used to infill annular space between liners that carry electrical transmission cables. The heat generated by transmission cables under load needs to be efficiently transferred to the surrounding ground to control cable temperatures and extend the life of cables contained within underground carrier systems.
The flowable consistency effectively fills voids around cable ducts and spacers within the liner, providing an efficient heat-conducting medium. Carefully selected and balanced ingredients reduce the segregation of sand aggregates, providing more uniform consistency throughout the annular fill.
The thermal grout is blended at a partnering ready-mix plant, where each ingredient is carefully weighed and batched using clean potable water. On-site testing of each truckload confirms the delivered material meets our specifications. Modifications can be made onsite to ensure flowability requirements are met.
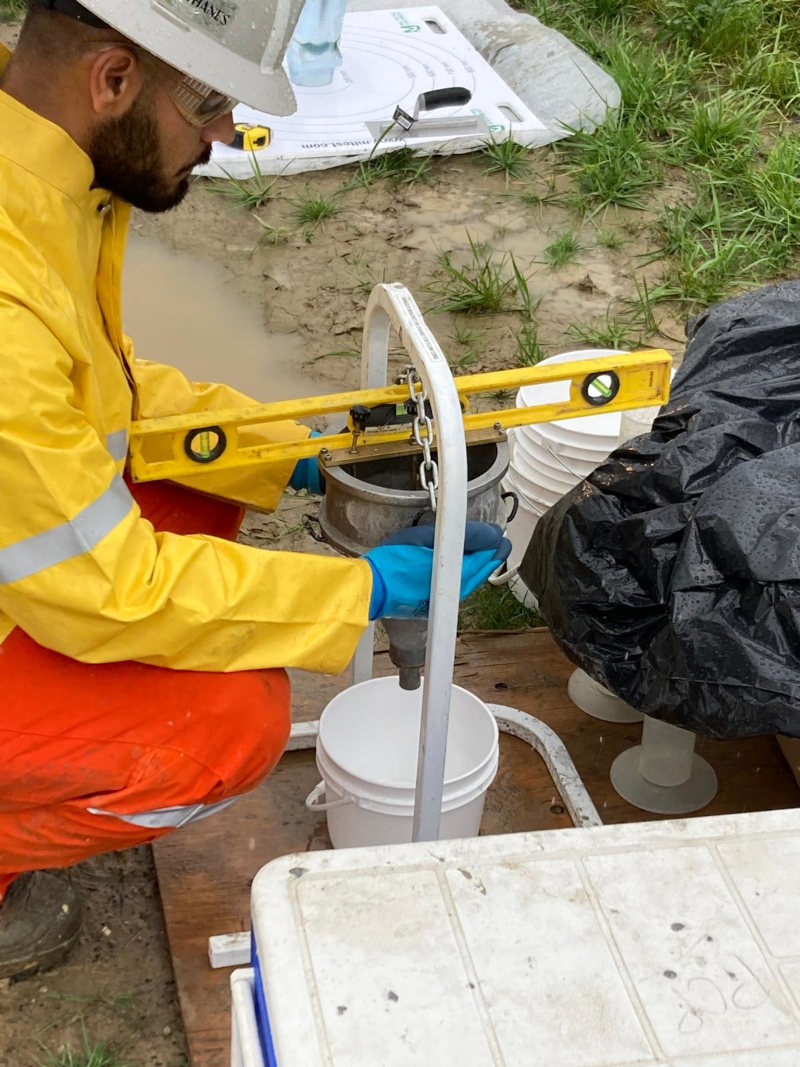
The materials used by the ready-mix company must be carefully stored with excellent quality control in place to prevent larger aggregates from contaminating the thermal grout mix and causing blockages of grout hoses and slick lines during the grout placement operation.
Properties
Areas with a high water table are prone to groundwater intrusion into casings and liners. The specific gravity of mixed Multiurethanes’ Thermal Grout is 2.13 kg/L to 2.19 kg/L. This makes the grout capable of displacing standing water within the annular space, ensuring uniformity with minimal segregation of fine aggregates.
Choosing improper backfill materials with high thermal resistivity and low thermal conductivity can cause the material to act as an insulator.
The low thermal resistivity of the Multiurethanes’ Thermal Grout tested (ASTM 5334/IEEE 422) is 0.50 – 0.60 mK/W (Wet/moist condition) and 0.70 – 0.8 mK/W (oven-dried), allowing for effective heat transfer generated from the electrical cables.
The cured thermal backfill material will have a compressive strength greater than 20MPa, providing adequate structural strength.
Mac Palomares is a grouting specialist at Multiurethanes.