Crossing the Elbe River in Germany Results in Record Project
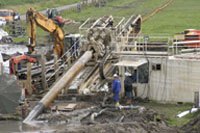
A 55-km long ethylene pipeline must connect the chemical plant of Sasol,Brünsbuttel with the plant of DOW in Stade. For this, the Elbe River needed tobe crossed by horizontal directional drilling (HDD), in accordance with thefollowing requirements:
• Reduction of impact on the nature reserve areas atthe river sides near the dykes. The entry and exit point were chosen outside ofthe river dykes. This resulted in a crossing length of 2,626 m.
• Heavyshipping traffic on the Elbe River. This did not allow measuring and steeringcables in the shipping lanes.
• Cobble layers at the river’s sides,endangering the stability of the drilled hole.
• The project team consistedof: project owner, chemical company Sasol; the feasibility study was made bybureau Dr. Kögler; primary contractor was Vorwerk; and the HDD contractor wasLMR Drilling.
Pressure Balance Swivel: An Important Component in the Record-breaking Elbe RiverCrossing A long reach horizontal directional boring followed by back reaming theutility pipe more than 2,626 m demands much from both personnel and materials.All equipment for the proposed crossing had to be engineered to the higheststandards to reduce risks that could lead to failure. One important componentwas the connection between the utility being installed (12-in. steel pipe) andthe reamer. The demands for the swivel were clear: The conventional shackle connection between swivel and product pipe wasdeemed unsatisfactory due to the lateral play, which could offset the productpipe and allow it to hang-up whilst entering the casings that were used at bothentrance and exit point. The design solution was engineered by BoreTech Hollandand connected the pipe directly to the swivel by means of a universal joint,which kept the pipe in line and prevented these lateral movements. It was also a major concern that there should be no risk of the reamer itselfnor any connections between the towing head and the swivel that could cause ahang-up especially when the assembly enters the spud casings. The reamer component is a solid steel ring with a diameter of 18 in. withnozzles and cutting surfaces. This reamer adaptation slides over the 6 5/8-in.FH connection and is mounted directly on the swivel, making it an integral partof the swivel. The bentonite is pumped through canals in the front part of theswivel to the reamer. This design allows BoreTech to build any size of reameronto the swivel, ensuring proper mud distribution onto the cutting face of thereamer. At the rear end a double clevis universal joint is attached directly tothe shaft and product pipe. The triple bearing arrangement of the swivel allows severe radial and axialloads in any direction. The bearings are lubricated with heavy-duty oil, whichhas far better lubricating and thermal distribution properties than grease. Theoil lubrication also made it possible to use the unique pressure-balance seal,mainly used in large HDD swivels in Europe since 1991. This pressure-balanceseal equalizes the pressure difference between the mud down hole and thelubricant inside the swivel, preventing any pollution to enter the bearing area.This seal is based on the simple principle that fluids will not move unlessthere is a pressure differential. Pressure balance also means that the seal can withstand almost any pressure,regardless of down hole mud pressure or drilling depth. A rock guard with areturns separation seal and a labyrinth seal protects the pressure-balance seal. This construction forms a multi-stage barrier between the bentonite andlubricant. The simple construction of the rock guard and outer seal makes iteasy to check and service the seal on the jobsite without dismantling theswivel. This sidebar was submitted by BoretechHolland. |
Feasibility Study
Because of the graveland cobble layers at either side of the river, it was proposed to install 48-in.sleeve pipes at both sides of the crossing prior to the commencement ofdrilling. A general methodology was devised to:
• Mobilize two drill rigs, each with a pull capacity exceeding 567,000 lbs tosites on either side of the Elbe River.
• Drill 48-in. sleeve pipes at eachside.
• Commence drilling at the north side to a target area some 2,000 maway.
• Commence drilling at the south side and intercept the other drilledhole within the target area.
In the engineering phase, LMR further developed this general methodology todetermine the best technical solution for final installation.
Soil Investigation
Due to the extremelength (aproximately 2,700 m) and depth (45 m) of this crossing, it wasextremely important to have extensive and reliable soil information. Despite theconsiderable expense, this was essential to ensure that the crossing could bedone and could be engineered to the best standards. In particular, the coringsunder the Elbe River involved some extra but well spent soil investigationcosts. Next to these geotechnical field investigations, geophysical andlaboratory tests were executed.
It was in every party’s interest to have this reliable soil informationavailable in order to let LMR Drilling find the optimal engineeringsolution.
Contract
Despite the considerable soilinformation, the length of the crossing and the depth at which the drillintercept had to be made meant that it was still conceivable that the groundconditions might make the crossing impossible. As such, the contract protectedLMR Drilling against this risk during the early stages of the drillingoperation. Beyond this point, the contractor had to continue at its own risk onthe basis of the ground conditions that had been discovered to date. Only aftera certain period, would more compensation be provided, which means extra daystimes a day rate. Still a maximum limit was set to the total cost for theproject.
Meeting in the Middle
The pilot hole wasexecuted with a 2 7/8-in. drill pipe, which subsequently was washed-over with a6 5/8-in. wash-pipe. Because of this and a perfectly drilled hole, the pushforces and torques were kept to a minimum. Special, heavy-duty, 13 3/8-in. drillpipes were used. The “Meeting in the Middle” went as follows:
Due to the successful drilling from the north, the north pilot bore wasdrilled to 2,100 m and the wash-over some 100 m behind. The south pilot bore wasdrilled in to the target area. The pilot pipe from the south side wassuccessfully steered into the wash-over pipe from the north. This activity wasexecuted at a depth of more than 40 m and some 2 km from the north side. Thesurvey equipment indicated that the pilot heads had initially approached eachother 4 m apart and with a 1 m difference in elevation. The angle from the onehole to the second hole was less than 1 degree. The south pilot was then pulledback and re-routed so as to intercept the north pilot hole and produce acontinuous, 2,626-m long hole beneath the Elbe River.
This approach of the two drill strings was assisted by sensors in the drillheads combined with an additional magnet sub at the end of one of the strings.The sensors could detect the other string when the magnets were activated (byway of rotation). Furthermore, this project also used “benchmarks” complementingthe modern Paratrack II system. Benchmarks act as “magnetic lighthouses” for themeasuring sensors in the pilot string. They were temporarily placed on thebottom of the Elbe River.
Upon completion of the pilot hole, the hole was reamed to a diameter of 18in. in order to pull in the 14-in. diameter product pipe. During this process,both drill rigs were engaged in order to operate the reamer and pump thedrilling fluid. In this way, fluid transports and return pipelines can beeliminated. The measured push forces and torques stayed under 500 kN and 50 kNm,respectively. In order to reduce the risk of hitting the edge of the casing atthe exit side, a customized swivel from Boretech Holland was used.
On July 11, drilling of the first pilot hole started from the north side. OnJuly 29, the second pilot hole commenced from the south. The pullback happenedon Aug. 25. The net drill time amounted to six weeks. To minimize the influenceof the drill activity on the environment, the work was executed in double shiftsand during seven days of the week.
The success of this project, which has extended the limits of horizontaldirectional drilling, was only possible with the full understanding of allparties of directional drilling and acceptance of all parties of the remainingrisks. This risk had been limited by an extensive, costly and reliable soilsurvey. In addition the remaining risk had been fairly distributed over theparties.