Crossing Italy’s Po River
February 1, 2009

A 10-in. diameter product pipeline operated by SIGEMI — a joint venture controlled by Shell — runs from Genoa on the Mediterranean coast to a distribution terminal just south of Milan at Lacchiarella. The pipeline crosses the Po River, near Pavia. Built in the 1970s, the Po River crossing was constructed using open-cut methods. Historical records dating back to the 19th century indicated that the Po River channel at the pipeline location has meandered across a 1.24-mile wide flood plain. Deepening of the river bed had also been observed, most likely due to excavation of the river bed gravels for construction materials. Channel movement over the last 30 years was threatening the integrity of the pipeline river crossing. A pipeline break could cause catastrophic environmental damage to the extent that repercussions could threaten the viability of SIGEMI’s business unit in northern Italy. In 2005, SIGEMI began planning the replacement of the pipeline across the Po River flood plain.
Gravels presented the greatest challenge to construction of the new crossing. The soils of the upper and middle sections of the Po River are comprised of a thick, sandy gravel alluvial deposition. More than 23 million cubic meters of gravel are commercially excavated annually from the Po River.
Preliminary Investigations
To better evaluate the viability of various construction methods, four rotary drill holes were undertaken along the 6,600-ft alignment at a 99-ft depth; 10 additional auger borings were also taken and the soil strata were visually classified. Sieve analyses confirmed that the strata were mainly comprised of gravels and gravelly sands. Nearly all of the gravels identified passed a 1.6-in. sieve and gravels exceeding a 0.8-in. sieve made up 30 percent of the in-situ material.
Various construction methods were considered. The local public authorities wished for the replacement section of the 10-in. diameter pipeline to be a minimum of 19.8 ft beneath the existing river channel and maintain this elevation across the entire 1.24-mile flood plain. The depth, along with the danger of major excavations near the operating pipeline, precluded using conventional cut-and-cover methods. Both horizontal directional drilling (HDD) and microtunnelling were considered. Although it was recognized that the high gravel content would challenge either method, HDD appeared to be significantly less expensive and would be readily approved by the local public authorities because HDD is less invasive.
Pre-Construction Activities
Italian pipelay contractor Impressa Tre Colli of Fidenza was chosen as the general contractor. Tre Colli would procure the line pipe, undertake site preparation and restoration, fabricate and test the pipeline string and perform all testing and tie-in work. Tre Colli subcontracted the HDD activities to LMR Drilling GmbH, Oldenburg, Germany.
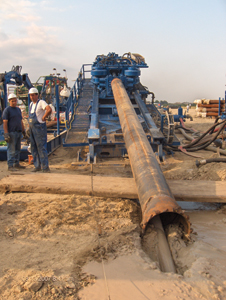
The line pipe, 10-in. diameter by 0.365 in. w.t. API 5L X52, was thoroughly analyzed for stresses resulting from construction loads, hydrostatic testing and operating pressures. However, there were concerns about the corrosion coating being pulled through 6,600 ft of abrasive soils and the steel casing. The pipe was coated with a three-layer polypropylene protective coating and an internal layer of fusion bond epoxy coating.
Right of way limitations would not allow for the fabrication of the pullback string into one piece. A tie-in weld, referred to as the “Golden Weld,” would be necessary during pullback operations. The location of the Golden Weld would allow continued pulling of several hundred feet even if there was a weld failure or other delay.
Construction
Tre Colli began site preparation activities in early July 2007. The rig site on the south bank was leveled and work areas prepared with packed gravel. LMR began mobilization and rig setup in early August. LMR employed a seldom used drilling technique with the pilot hole drilled with 2 7/8-in. diameter drill string and then washed-over with the 6 5/8-in. drill string. This method is advantageous in gravelly soils because it reduces pushing forces and minimizes fluid loss to the surrounding soils. The pilot hole was drilled through approximately 660 ft. The 20-in. casing was run through a length of 541 ft and a 99-ft depth. The casing was cemented in place. Significant gravel content was observed in the mud returns during the casing installation.
Pilot hole drilling recommenced and the 6 5/8-in. washover string was regularly advanced behind the pilot string. LMR used a Paratrack II survey system with its Pressure While Drilling (PWD) data gathering tool. Since the annular pressure was monitored, LMR was able to make remedial efforts before the mud surfaced. The mud properties were carefully measured and controlled. There were full returns of mud and cuttings to the HDD entry as the pilot hole advanced through a drilled length of more than 5,940 ft.
After 13 days, the pilot hole exited 3.6 in. from the HDD exit stake. Unfortunately, the pilot hole was completed 15 days ahead of schedule — meaning the pipeline strings would not be ready for pullback for at least two weeks. In most instances, this presents many problems for the HDD process, as the hole can deteriorate over time and collapse. However, the washover system and management of the mud properties mitigated these problems. After completing the pilot hole, the washover drill pipe was fully retracted from the hole and the LMR crew was demobilized until the pipeline strings were ready.
In early September, the LMR crews began the reinsertion of the washover pipe. Torque forces were similar to when the washover pipe was originally installed. Once the washover pipe was completely installed, the 2 7/8-in. pilot hole drill pipe was retracted and preparations were made for the pipeline pullback operation. Pullback of the pipeline string began at 10 a.m., Sept. 12. The pullback continued throughout the night and was completed at 9 a.m., Sept. 13. The pullback took 23 hours, including 4 ½ hours to complete the Golden Weld.
The project was a success: HDD provided the pipe replacement with significant cover across the entire flood plain. There is minimal likelihood of damage from future river channel movement and no significant environmental impact.
Eric Skonberg is with Trenchless Engineering. Andrea Stagni is with Shell Italia. Giovanni Polloni, Luciano Adinolfi, Gunter Kruse and Jens Groninger are with LMR Drilling.