CIPP Technology Used on Sewer Lines in Germany
May 1, 2008
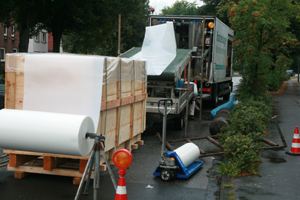
The easy handling of the factory-saturated pipe liner — BlueTec UVA light-curing technology — and the use of conveyor belt equipment proved to be a great advantage. The speed and quality of the rehabilitation impressed the client.
The Problem
A total of 1,040 m of rainwater pipes were in need of rehabilitation in Elmshorn, which is located just north of the City of Hamburg. During routine inspections, damages such as cracks and broken fragments, leaks, tree root intrusions and protruding supports were discovered underneath three streets.
In addition to the price, important for the submission of tenders for the renovation slated for August 2007, was the quality of the assigned work. Only those candidates that met the high standards of the Elmshorn water works were taken into consideration. The Brandenburger Co. based in Landau, Germany, in the Rhineland-Palatinate, provided the most economical offer while fully meeting the required technical characteristics.
The Solution
The greatest challenge awaited the sewer rehabilitation company on the busy street of Ansgarstraße, as 136 m of DN 1,000 and 583 m of DN 700 rainwater pipes needed to be rehabilitated, including the residential connections.
“The sewer construction on the Ansgarstraße is not contiguous. We divided the work into five construction sections,” explained Stefan Jensen of Brandenburger Liner GmbH & Co. KG on the rehabilitation project. “The longest pipe liner laid out in one piece was 198 m long, with a diameter of 700 mm.”
Despite the length of the sections to be rehabilitated and the size of the sewer diameters, the assignment would be completed at an unusually high speed. “The rainwater pipes on Ansgarstraße were rehabilitated within five work days,” according to Jensen. “None of the construction sections took more than 12 work hours.”
The fast implementation of the rehabilitation with the curing of longer segments, as well as in the course of just one work day was primarily attributed to the Brandenburger BlueTec light-curing technology by UVA light and a mobile curing unit. The average hardening speed was 60 m per hour for DN 700 and 42 m per hour for DN 1,000. As a time-saver, the use of Brandenburger conveyor belt equipment also proved its worth while drawing in the liner.
“Employing the conveyor belt makes it possible to install the pipe liner quickly and prevent damage to the material,” explained Jensen. “We use this technique generally to bridge greater installation lengths spanning several conduits. This makes it easier for the workers and damage to the material is avoided.
“Thanks to the quick curing, a significant amount of effort and thereby time and money could be saved,” concluded Jensen, noting that “up to 1,200 liters of water rushes through the pipe per second when
it rains.”
Based on the light-curing technology used, the rain-free timeframes could be optimally exploited as they were determined in cooperation with the weather forecast service. The water drainage, prepared in advance in case of an emergency, was not needed.
In light of the rainwater problems, the simple handling of the pipe liner also proved its worth.
“The factory-produced and pre-saturated liners are distinguished by high-storage stability. Packed in UV-proof material, the material does not react,” Jensen explained, allowing for greater planning reliability. “In case it would have started to rain unexpectedly, before the beginning of a rehabilitation section, we would not be forced to react on that day,” said Jensen. “Thanks to the uncomplicated features of the Brandenburger liner, your timing remains flexible and no material is lost, even due to unforeseen delays.”
Reaction
Martin Röseke, project manager at the Elmshorn water works, also had a positive review of the Brandenburger technology. “We were impressed foremost by the speed of the rehabilitation and of its high quality,” he said. “Using light curing, the project could be completed much quicker than when using warm water curing.”
In addition, the Brandenburger liner was impressive in the lower K-values in comparison to the older concrete pipes, even in the hydraulic values. Thus, the almost same maximum drainage was reached during flow rate measurements during comparable rain showers even though the diameter was reduced.
“We sent material samples of the rehabilitation project to various engineering offices for material inspections. All were returned with uniform good results,” said Röseke.
Based on the positive experience, Röseke also assigned Brandenburger with the rehabilitation of a 300-m long, DN 300, sewage, rainwater, mixed water conduit in the neighboring street.
Benedikt Stentrup is with sales management at Brandenburger Liner GmbH & Co. KG, which is headquartered in Landau, Germany.