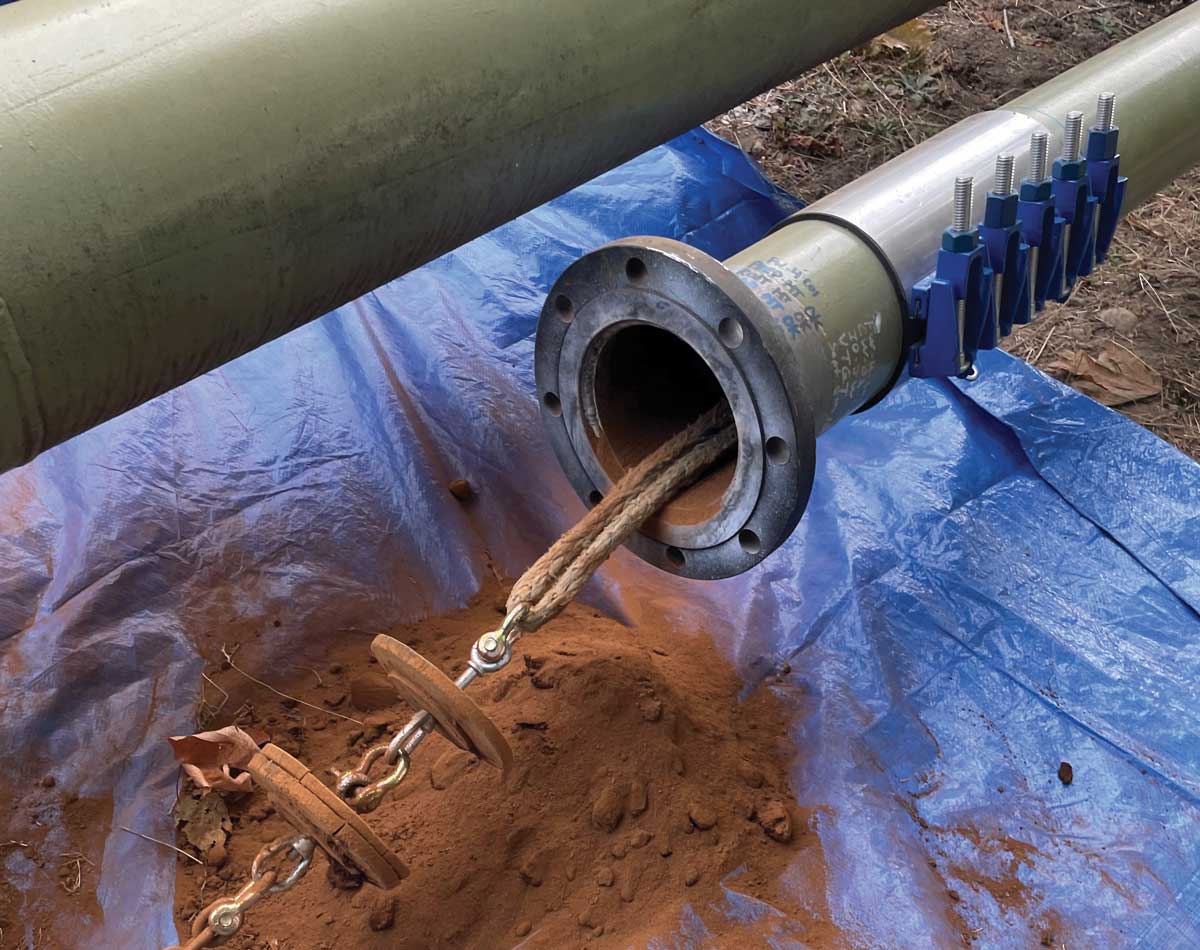
Capital Infrastructure Group Completes Pressure Pipe Project Using FFRP
Panoramic vistas, crisp mountain air, and the augural spectre of the Rockies were all the backdrop for the most recent pressure pipe rehabilitation project, completed by Capital Infrastructure Group.
FFRP Project Background
When a major Western Canadian refinery, identified a chlorine treated wastewater pipeline for rehabilitation, flexible fabric reinforced pipe (FFRP) was chosen as the optimal technology due to its ability to traverse the entire pipe section in one pull, while accommodating the higher-pressure requirements, despite any inherent characteristics of the transported medium.
The subject pipeline was showing signs of prolonged leakage. These failures were due to the significant amount of chlorine which had to be added to the transported wastewater, which was necessary to comply with the local sewer district’s odor requirements. Local repairs with handiband pipe clamps were installed on a regular basis, however, the pipe was due for a complete rehabilitation.
Replacement of the carbon steel pipe was not an option, and HDPE or PVC materials were ruled out due to the risks of thermal expansion. Even though the subject pipe was an above-ground line, a decision was made to select relining as the best-fit solution.
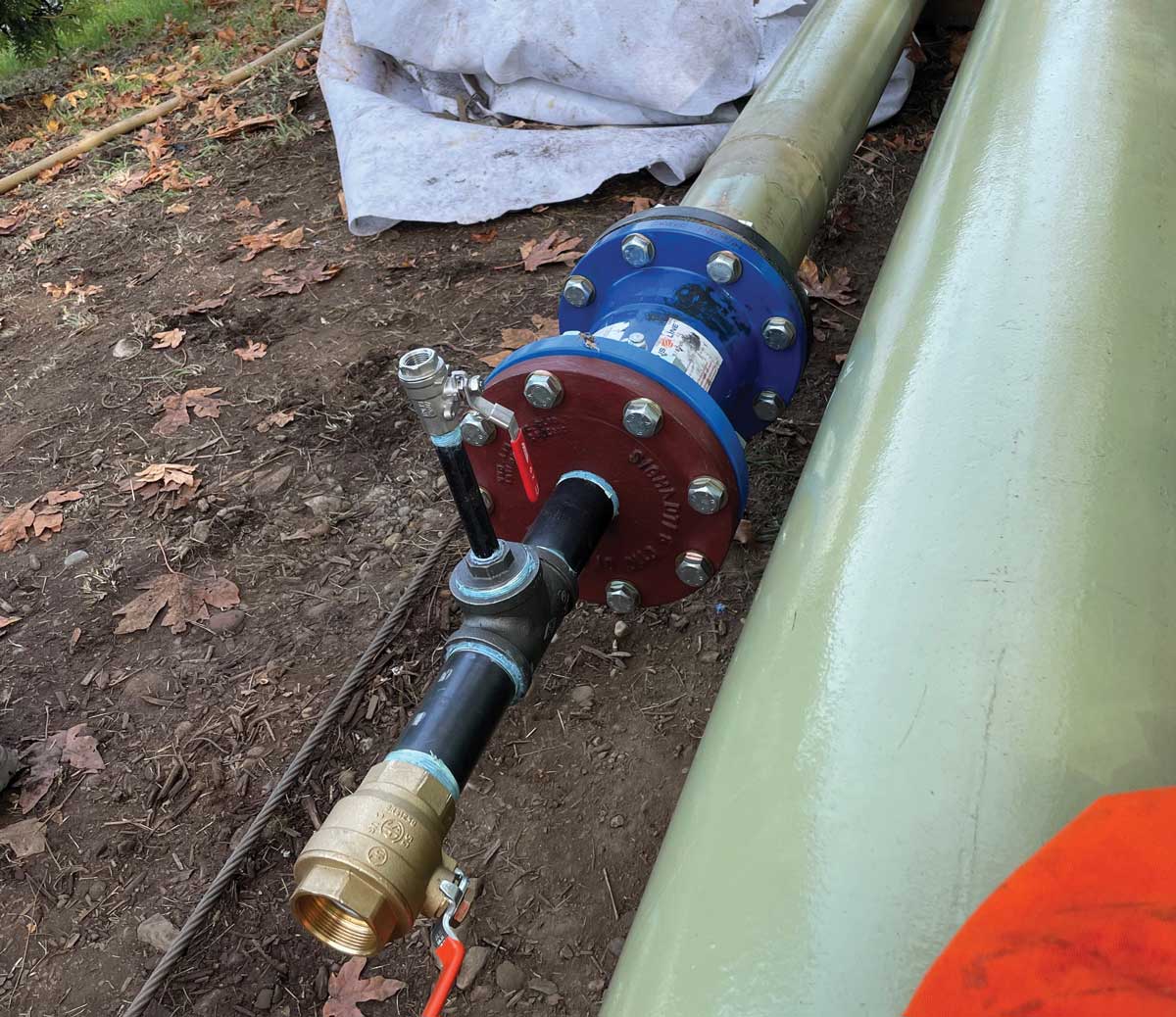
On-Site
“The job site was awesome, and it was total teamwork, right from the get-go,” says Neil Murray, director of trenchless for Capital Sewer Services who was on-site for the duration of the project. “One of the challenges we faced, was using brush pigs to clean the existing 150 mm pipe, but that’s only because the process was new to us. Once we got the hang of it, the operation went off without a hitch.”
After cleaning and verification of the inner diameter via a second CCTV inspection, the installation of the Primus Line FFRP system could begin.
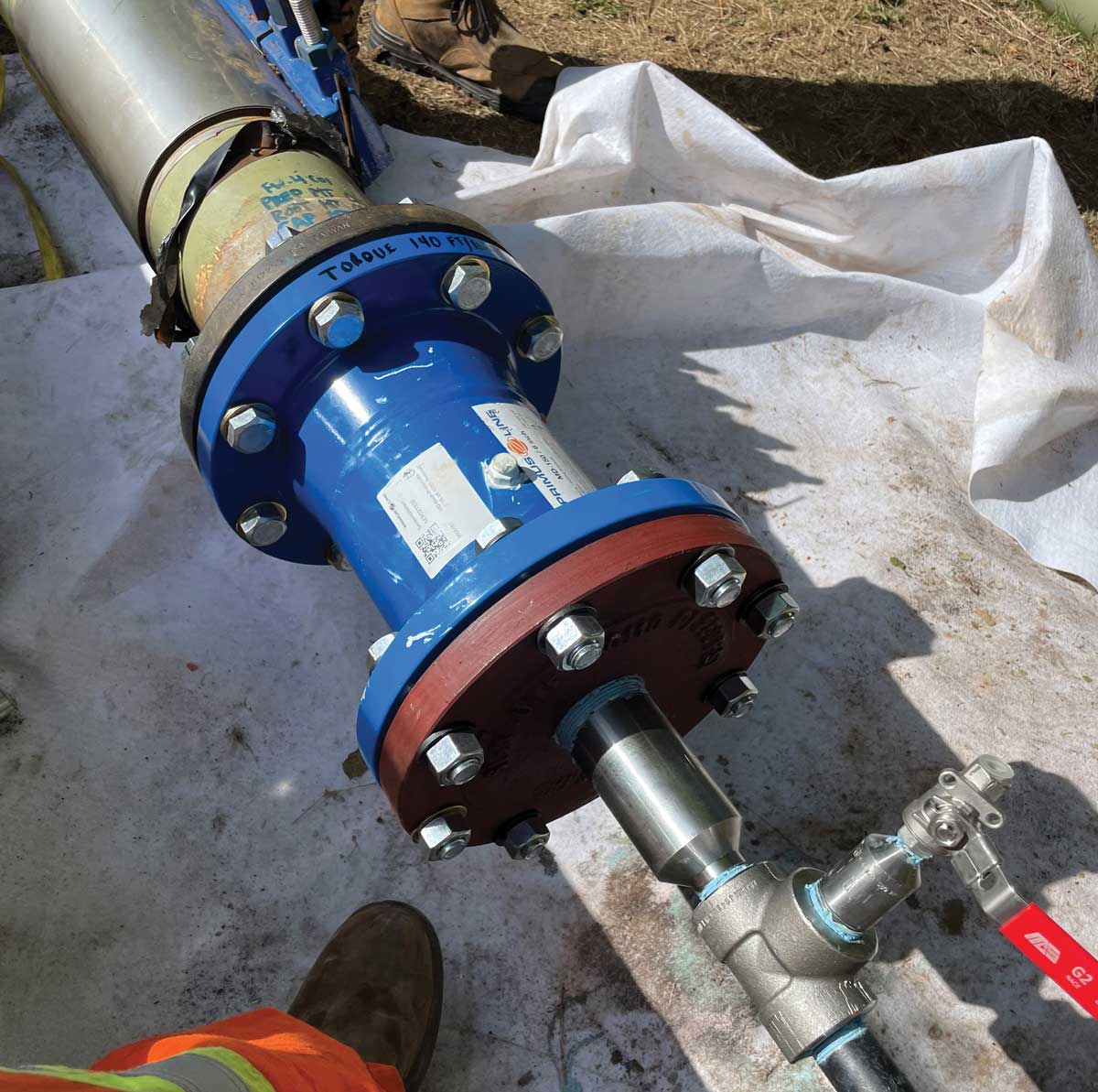
Flexible Fabric-Reinforced Pipe
FFRP systems have been used in pressure pipeline rehabilitation for more than two decades. The system consists of a flexible aramid-reinforced pipe, and specially developed end fittings. These systems have design applications for the rehabilitation of water, sewer, oil and gas pressure pipelines.
FFRP is characterized by a three-layer composition with a polymer inside and outside coating, as well as reinforcement fabric. The system is comprised of two main components: a flexible, seamlessly woven aramid liner and specifically developed end fittings with standard ANSI flanges. The liner itself, is a factory-manufactured round pipe that is modified into a “C” or “U” shape, and then coiled onto reels which can be anywhere from 1.5 m to 12 m wide, and can accommodate over 5,000 m, depending on the pipe diameter and project needs.
Developed in Germany during 1990s, the Primus Line system was originally designed for use with for high pressure gas pipelines. The product holds numerous international, potable water certifications including NSF/ANSI 61, with a design life of at least 50 years.
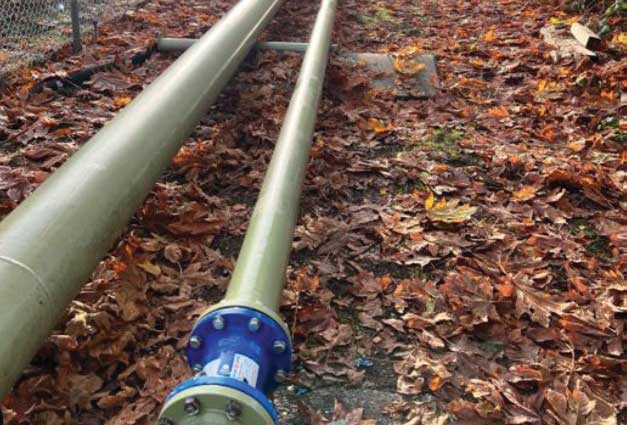
FFRP Installation
“The pull-in and the actual install were a breeze,” says Murray. “The supplied fittings made our life easy. While the pressure testing was something new for us, it was challenging, but also very manageable.”
To facilitate the installation, a transport drum carrying the liner material was placed at the entry point of the subject pipe. And due to the uneven terrain – a scaffold – on which the transport drum was placed, had to be set-up.
As a first step, the liner was pulled through the host pipe using a winch that was positioned at the exit pit.
Subsequently, the liner was inflated using compressed air. To complete the installation, the specialized fittings referenced below, were utilized and assembled on each end of the subject pipe section. All components are produced at an ISO 9001 certified production plant in Germany. In this case, a 150 mm FFRP, and two Primus Line R1-connectors were used, for reintegration into the Refinery’s existing wastewater network.
Installation follows the modified sliplining method of pipe rehabilitation, however, FFRP enables installation through bends in the host pipe, and the product is brought to the construction site cut to its installation length. Furthermore, only a minimal footprint is needed, due the limited on-site equipment needed for installation which results in quick execution times. The flanged, force-fit end connectors, streamlines the process.
As previously mentioned, the product can be installed regardless of the host pipe material with the proviso that the subject pipe be able to accommodate all external loading – a wide range of internal line pressures can be completely accommodated.
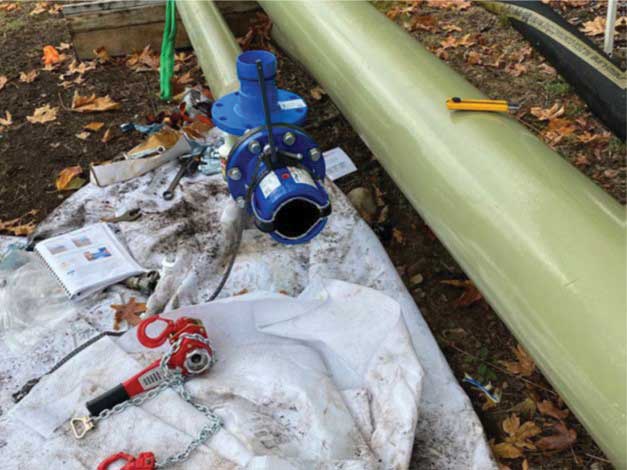
Observations
“We see a future in the pressure pipe market, and because of the technology and its ease of use, this application is a natural fit for us,” says Brian Ratchford, chief operating officer of Capital Infrastructure Group. “We hope to complete a few more projects, as company looks to expand its service offerings for our key clients.”
These sentiments are echoed by Tyler Leeming, Capital Infrastructure Group’s vice president of infrastructure. “As we ramp-up and increase our bandwidth, strategically situated opportunities will bode well for the long-term future of Capital Infrastructure Group,” he says.