Auger Boring Challenges in the Virgin Islands
Saint Croix is an island in the Caribbean Sea and a county and constituent district of the United States Virgin Islands (USVI), an unincorporated territory of the United States. As the largest of the U.S. Virgin Islands, being 28 by 7 miles, it hosts one of the world’s largest and most modern oil refineries — Hovensa.
Construction of the 45,000-barrels per day (BPD) refinery began in October 1966. Substantial expansion occurred in the period 1966 to 1974 to increase the refinery’s capacity, making it the largest refinery in the world at that time. Heavy oil upgrading capacity was gradually added beginning in 1981,eventually increasing the refinery’s capacity to 485,000 BPD.
To accommodate the original 2,000-plus acre facilities on the south shore of St. Croix, a quarter-mile of wetlands was dredged and contained by a 120-ft long by 20-ft high dike that eventually became home to a service road, power and fire lines, and four major fuel lines that connected the refinery to adjacent holding tanks.
Many years and four major hurricanes later, two of the four major fuel lines had to be shut down due to leaks. At a cost of $800,000 per day in lost revenue, immediate upgrades were required.
Lack of as-builts and supporting documentation for the original facility and containment areas proved an immediate challenge on this project. Although it was known that a 30-in. fire line, a 12-in. water line and a 12,000-kv electric line existed in the area of the newly proposed pipelines, their exact location and depth was unknown. Initial soil investigation revealed moderate clay and coral at 15-ft, however, soil conditions beyond that point were also vague.
To minimize cost and risk, horizontal auger boring was selected as the most suitable trenchless method for replacing the leaking fuel lines. Four 120-ft auger bores to install two 30-in. OD steel casings and two 48-in. OD steel casings were required, since two additional fuel lines had begun to leak just prior to construction, which began in early October 2007.
Installation challenges were immediately apparent as the first of the two initial bores to install 48-in OD steel casing failed. Extreme weather had stripped the binding material from the outer layer of coral causing the loose material in it to cave in. Dropping a foot below grade, a second bore successfully cleared the loose material but became bound in dense, sticky clay at approximately 60 ft. Water was pumped in and around the auger to loosen the clay and allow the auger to glide for another 40 ft. Once again, the auger encountered the outer layer of coral as it exited the dike, making turning the auger impractical. It was then shut down and used as a jacking device for the remaining 20 ft, successfully avoiding a nearby overflow oil drain.
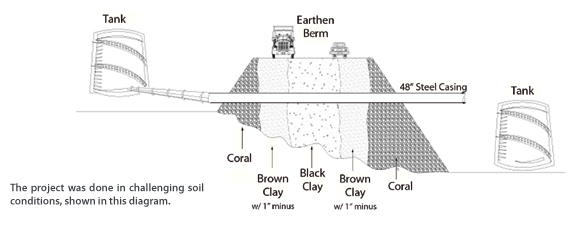
With little room to maneuver and little time to spare, each of the three remaining casings were installed successfully and the project was completed in mid-October 2007, amazingly eight days ahead of schedule.
Although the lack of as-builts did prove detrimental initially, Specialized Services Co. was able to employ a combination of innovation, technology, and experience that resulted in success.
As demonstrated on this project, the lack of as-builts and documentation will be the initial hurdle for any project. An excellent set of as-builts can save much time and money for an owner and contractor, helping them to make more informed decisions and reduce risk. It is common for changes to be made during construction. What becomes the challenge is making sure those changes are reflected in the as-built records.
Arvid Veidmark III is executive vice president of Specialized Services Co., which is headquartered in Phoenix.