A Longer Life
July 1, 2008
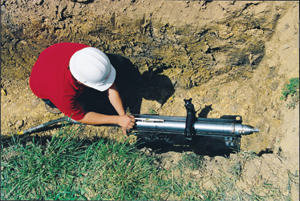
According to piercing tool specialist Rick Bissonette, from trenchless equipment manufacturer TT Technologies, Aurora, Ill., the key to long tool life and reliable service is simple: Keep the inside of the tool clean and operate it within the guidelines of the manufacturer. There are several maintenance procedures that piercing tool operators should perform in order to meet those objectives and keep their tools running smoothly.
Preventative Maintenance
Sometimes preventative maintenance comes in the form of doing some research before a bore. That begins with knowing the ground conditions. “The ultimate goal of a good maintenance program is to ensure operation of the tool,” Bissonette said. “If a tool is lost or becomes damaged because someone didn’t take into consideration how they were using it or what adjustments needed to be made for specific ground conditions, then no maintenance program is going to help that. So I classify doing your operational homework as part of a good preventative maintenance program.”
This includes knowing what the ground conditions are and taking steps such as marking air supply hoses in 10-ft intervals in order to more easily monitor a tool’s progress during the bore. It also means knowing how to operate the tool in these various soil conditions.
“Sometimes crews get into granular soils that collapse behind the tool blocking exhaust air, stalling the tool and halting the bore. Pulling pipe in this case preserves the bore hole and completes the bore,” Bissonette said. “Groundwater is another issue. Groundwater can hinder the performance of a piercing tool and it can also dirty the tool considerably. Being familiar with the challenges that each of these conditions pose is an important step to successfully completing the bore. These tools have been around for decades and there’s a lot of cumulative knowledge out there. If you’re new to boring, a call to your tool manufacturer might prove very helpful in these situations.”
Cleaning & Service
According to Bissonette, flushing the tool is one of the easiest, and most effective maintenance procedures for a piercing tool. When boring in wet, sloppy soils, a lot of dirt and debris can be pulled into the tool. When left unchecked, that debris can cause performance and eventually wear problems with the tool.
“Flushing the tool consists of pouring a cleaning agent into the air hose and running the tool above ground until all the debris is flushed out,” he said. “In the past, diesel fuel was commonly used as the cleaning agent, maybe a cup or so in the air hose. But today, many contractors utilize our environmentally friendly, biodegradable lubricant to clean their tools.” Depending on the condition of the tool, the flushing procedure may need to be repeated several times. But afterward, a quick wipe down and the tool is ready for storage.
Bissonette also said there is no preferred way to store a piercing tool. He said some contractors store them horizontally, others vertically. But with all tools, leaving them out in the elements will hasten their deterioration.
Associated Equipment
Keeping all the tools and equipment needed for underground boring applications running and in good condition is also part of the larger piercing tool maintenance picture. Here’s a quick rundown.
Compressors
Keeping the air compressor in tip-top shape will help keep your piercing tool running at peak performance as well. Bissonette said this is especially critical in cold weather applications. Draining the compressor of moisture is critical to preventing freeze-up in all pneumatic tools, including piercing tools, during cold weather applications.
Lubricators & Compressed Air Heaters
This item would go on the check-before-each-use list. Many pneumatic tools, included piercing tools, need to be lubricated during operation. Simply checking the lubricator before operating the tool is a good idea to help make sure things keep running smoothly. Petroleum-based lubricants are common and perform well in warm weather. Biodegradable lubricants are also common and perform exceptionally well in cold weather.
Cold weather can really have an impact on piercing tool performance and Bissonette suggests using a compressed air heater to prevent frost build up. Several types are available and Bissonette suggests checking with the tool manufacturer for recommendations.
Air Hoses
Checking air hoses on a regular basis can easily mean the difference between a success and a costly breakdown. “While a hose will fail when it fails, regular inspection and proper upkeep can at least extend the life of the hose and hopefully prevent a failure on the job,” Bissonette said. “It’s basically a visual inspection, but it serves to address both tool performance issues, as well as safety issues.” Blowing any dirt and debris out of the hose before use is also recommended.
Locking the couplers during use with a threaded locking ring or even duct tape serves a dual purpose. First, it helps ensure that the couplers remained locked together during a bore, but it also helps keep dirt and debris from packing into the coupler sliding collar. A visual inspection of the seals on the couplers is also recommended to make sure that the tool is working at its best.
“Another good operational practice is to lay out the air hose and blow compressed air through it before final hook up to the tool,” Bissonette said. “Test fire the tool at ground level before placing it into the starting pit. An ounce or two of air tool lubricant poured into the air supply line before connecting to the lubricator will ensure that the supply hose is properly coated and will allow the lubricator to immediately supply the lube necessary for optimum tool performance.”
Following Manufacturer Recommendations
According to Bissonette, any time operator receive a new tool, they should read the operator’s manual to become familiar with the operation and air pressure requirements of this tool. A tool operated at less than recommended air pressure will be severely under powered and a tool operated above recommended air pressure will fatigue some of the parts and cause pre-mature failure.
While each piercing tool operates on similar principles, each piercing tool manufacturer has its own recommended service and maintenance schedule. “Some manufacturers suggest servicing the tool frequently, after every 30 hours of use,” Bissonette said. “That includes disassembling the tool to check seal condition and spacing. Some types of plastic seals become elongated after use and can get to the point where they create resistance in the tool and need to be replaced.
“For other tools, regular service and seal inspection intervals are longer — 400 hours. This can partially be attributed to different types of seals. Teflon-constructed seals have different wear properties than plastic seals and don’t require service as often. Again, it all comes down to reading your manual and seeing what the manufacturer recommends. This is often overlooked, but can make a big difference in the performance and life expectancy of your piercing tool.”
Jim Schill is a technical writer, based in Mankato, Minn.