A Curvy Situation
July 1, 2008
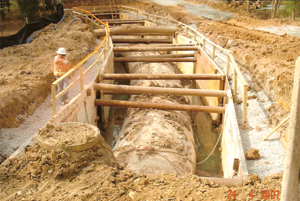
Anticipating a rehabilitation of the sewer line, the department engaged the engineering firm of Greeley and Hansen, with Roger Cronin and William Judy doing the leg work. Their investigation revealed considerable corrosion due to the release of hydrogen sulfide inside the pipe.
“This combination mixed with water develops sulfuric acid, which could cause the deterioration and breakdown of the 84-in. concrete pipe,” said Judy. Given the many complications of keeping this major, active interceptor sewer flowing, Judy and his team determined that sliplining would be the best method for this project because sliplining eliminated the need to bypass pump. There was never a need to stop the wastewater flow to install the pipe.
A bid was posted for the rehabilitation of the 84-in. trunk sewer line by sliplining with 4,022 ft of 72-in. fiberglass pipe, including rehabilitation of an existing 27-in. sewer by sliplining with 325 ft of 18-in. pipe. The contract also called for new reinforced concrete junction chambers and manholes, providing traffic control on I-295 and the crown spray treatment of 29,780 ft of existing 60-, 70- and 84-in. sewer with magnesium hydroxide. Crown spray treatment has been applied to sewers in the western part of the United States, but has rarely been applied in the East.
The winning bidder was Spiniello Companies of New Jersey, headed by the team of Sam Silva as construction/project manager and his superintendent, Kent Meier. This project became quite a challenge — which upon further examination would throw them many curves.
While most sliplining jobs are done with a straight line length of pipe, this pipe had six curves consisting of chords created by using concrete pipe with five-degree bevels on one end. Existing curves were short radius (168 ft), with a maximum total deflection of almost 50 degrees. There were many joints involved, including 150 pieces of 20-ft joints and more than 600 ft of 3-ft lengths for the curves.
Spiniello suggested an alternative method to slipline through the curves, thereby reducing excavations near critical structures. The county and the engineer reviewed the alternative method, which was allowed to proceed.
Silva and Meier met the challenge head-on. Safety was paramount for two primary reasons: the proximity of I-295 to the existing sewer and the safety of the crew that would be working in excavations that required shoring. Silva and Meier then proceeded to install excavation shoring and prepare a trench that was 40 ft long by 45 ft wide and 25 ft deep that was fully secured by a shoring system. It was Meier’s job to install the traffic system, which included the use of attenuators or impact cushions to help prevent drivers from going off the road into the nearby work zone. Even with those precautions, there were a few incidents, including one where a car slid on black ice into an excavator.
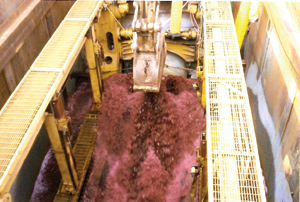
“Each pipe to be pushed into the original pipe weighed about 50 tons due to the weight of the water and working conditions,” Silva said. It took a powerful hydraulic pushing machine to place each section inside the old pipe — a painstaking effort by all.
Silva said that there would have been considerably more digging had not the pushing of the sections been so successful, particularly the use of short lengths of pipe for the curves. The short lengths of pipe included the 3-ft sections, with special couplings. A cleaning and sizing mandrel or “wagon wheel” was then used to clean the inside of the new pipe before completion.
Pushing a 72-in. pipe into the old 84-in. PCCP pipe required the installation of grout to compensate for the 12-in. difference in pipe size. In order to do this grouting, an excavator was used to temporarily back-up the flow.
Another suggestion by the Spiniello team was to use cured-in-place pipe (CIPP) for rehabilitation of the existing 27-in. sewer instead of sliplining, as proposed by the contract. It proved to be a cost-effective method for this portion of the project.
The project was unique in that the curves were pushed into place rather than installing the pipe by excavation and removing of the top half of the existing sewer. Sliplining of curves similar to this project was never done before on the East Coast. The precision and skill of the Spiniello team helped to make this difficult project go smoothly and to finish on time.
Silva and Meier took charge of this unique and challenging sliplining project. “These guys were great. They had never handled a job like this before. They really came through,” Silva said.
Alice Steinbacher is a freelance writer based in Bernardsville, N.J., and has been working with the construction trades for more than 20 years.