New Installation Project of the Year
October 1, 2008
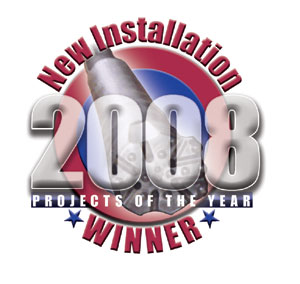
While far from the rainiest city in the United States, Portland receives more than its fair share of rain. Rain falls roughly 100 days each year in the city,which causes wastewater and stormwater volumes to exceed the capacity of the sewer system. When sewer capacity is exceeded, the overflows run into theWillamette River, a tributary of the Columbia River. The East Side Combined Sewer Outflow program is part of a massive program that seeks to eliminate CSOsinto the river.
The West Side CSO portion of the project completed tunneling in 2005 and went online in 2006. When the East Side CSO is complete in 2011, the reduction incombined sewer overflows into the Willamette will be reduced by 94 percent.
The $381 million East Side contract to Kiewit-Bilfinger Berger JV (KBB) includes six miles of 22-ft lined diameter tunnel running between 85 and 165 ft belowthe surface. Also included are seven shafts, 6,000 lf of microtunnel and 3,000 lf of open-cut pipeline construction.The microtunneled portion of the project is divided into drives of varying lengths. As noted, the original section joining Outfall 46 to the Port Center Wayshaft was designed by Parsons Brinckerhoff to be microtunneled in two drives. When the JV suggested combining these drives, BES had to weigh the potentialgains against the risks presented by a longer drive. “The construction contract is a cost-plus-fixed-fee contract, where labor, equipment and materials arepaid by the owner as reimbursable costs,” explains Paul T. Gribbon, P.E., chief engineer of the Willamette River CSO tunnel program. “It was a calculatedrisk taken by BES in accepting the higher risk of the long drive – in what we knew was difficult ground – against the potential cost-savings in eliminationof the intermediate shaft. The decision to take this risk was based on our previous experience with microtunneling on the West Side CSO Project in similarground conditions and with a similar machine.”
Ultimately, the decision to move forward with elimination of the intermediate shaft was a three-way risk-sharing by the owner, designer and contractor –highly unlikely, if not impossible, in a standard low bid contract.
The Drive
Herrenknecht is no stranger to record-setting micotunnel drives. According to Julian O’Connell, Herrenknecht microtunneling sales and technical consultant,the longest microtunnel drive worldwide was roughly 2,600 m (8,500 lf), performed with a Herrenknecht machine. The drive was in Germany, which is importantto note because microtunneling is defined differently in Europe than it is in North America.

A typical North American microtunnel drive numbers in the hundreds, rather than thousands of feet. The originally-specified drive would have been record-setting in its own right, but increasing its length by half made it that much more challenging — and impressive.According to KBB microtunneling manager Scott Wimmer and KBB microtunneling superintendent Matt Roberts, the soil facing the machine on Drive 4 ispredominantly sand/silt/alluvium and fills. Drives 1 through 3 included encounters with Troutdale Formation, which consists of gravel and cobbles withintermittent fine materials.
“We didn’t have many surprises on the first drives,” says Wimmer. “We encountered some wood that the MTBM handled well.”“We have also used a centrifuge to assist in soils separation when tunneling through fine-grained soils, such as clay and silts,” adds Roberts.“Surface access is very restrictive,” says Kiewit’s Bill Mariucci of the span between shafts. “Including the drive running parallel to railroad tracks and atrain yard.”
The alignment also runs near enough to the river to cause groundwater concerns. “We anticipated that the microtunneling conditions would be challenging asthe alignment ran through in-filled ground along the river’s shoreline where extensive timber piling and industrial debris was to be found” says Roy Cook,project manager for the Parsons Brinckerhoff design team. “The record is a true accomplishment for the contractor’s MTBM crew and surveyors who maintainedsuch tight control on line and grade throughout the drive.”
The Machine
The MTBM is a Herrenknecht AVND2000 with a cutting diameter of 104.5 in. Key features of the machine include variable flushing modes to suit different groundconditions, a highly-effective cone crusher and access to the cutting wheel for tool replacement. Additional consideration and adjustments were made in lightof the length of the drive.
“We fitted an electrical trailing sledge with a transformer in the tunnel to accommodate the length,” O’Connell explains. “Also, we installed a Herrenknechtgyro and water level system for guidance.” He notes that the drive length is out of range of the more-typical laser guidance system.Another feature that suits this particular machine to a longer drive length is that the face can be reached through an access door. Cutter wheel inspectionand teeth changes can be accomplished through that access in a pressurized air chamber. “Of course, if cutters become worn and no longer mine properly, drivelength is compromised,” O’Connell says.
The Process

KBB also deployed a Herrenknecht Automatic Bentonite system to ensure good lubrication to the exterior annulus of the pipe. The pipe installed behind theMTBM was 84-in. ID class 4 concrete jacking pipe.
“The key to a drive of this length is keeping the friction low and maintaining low jacking forces,” O’Connell explains.
Once the drive was under way, the crew found ground conditions worse than had been anticipated. Closely-spaced timber piles from long-abandoned docks and oldiron rail spikes slowed progress. Several machine shutdowns were needed to repair and clean the lines. Even so, the crew pressed on and the MTBM completedits drive into the record books. The drive took 60 work days of two 10-hour shifts. The average daily production was approximately 54 ft per day, withproduction on the best day being 152 ft.
Microtunnel drives are not designed to break records. The drive, machine and pipe specifications are dictated by ground conditions and availability of accesspoints among other factors. That said, as longer and longer drives find success in North America, drives will continue to lengthen when necessary.Contractors and designers are finding that the right machine with the best team can achieve drive lengths that would have previously been thought impossible.“KBB’s staff and the MTBM performed admirably through some very difficult mining conditions, including soft ground, wood debris and rail spikes,” saysGribbon. “Under a hard bid contract or a risk-averse project team, the setting of a microtunneling record would have been unlikely.”
Greg Thompson is an assistant editor of Trenchless Technology. Photos taken by Sue Bednarz, Jacobs Associates and used courtesy of Environmental Services,City of Portland.
Project Owner: City of Portland, Ore.
Engineer: Parsons Brinckerhoff
Contractor: Kiewit-Bilfinger Berger JV